Gearing axes, Gearing axes -3, 3 gearing axes – Delta RMC101 User Manual
Page 189
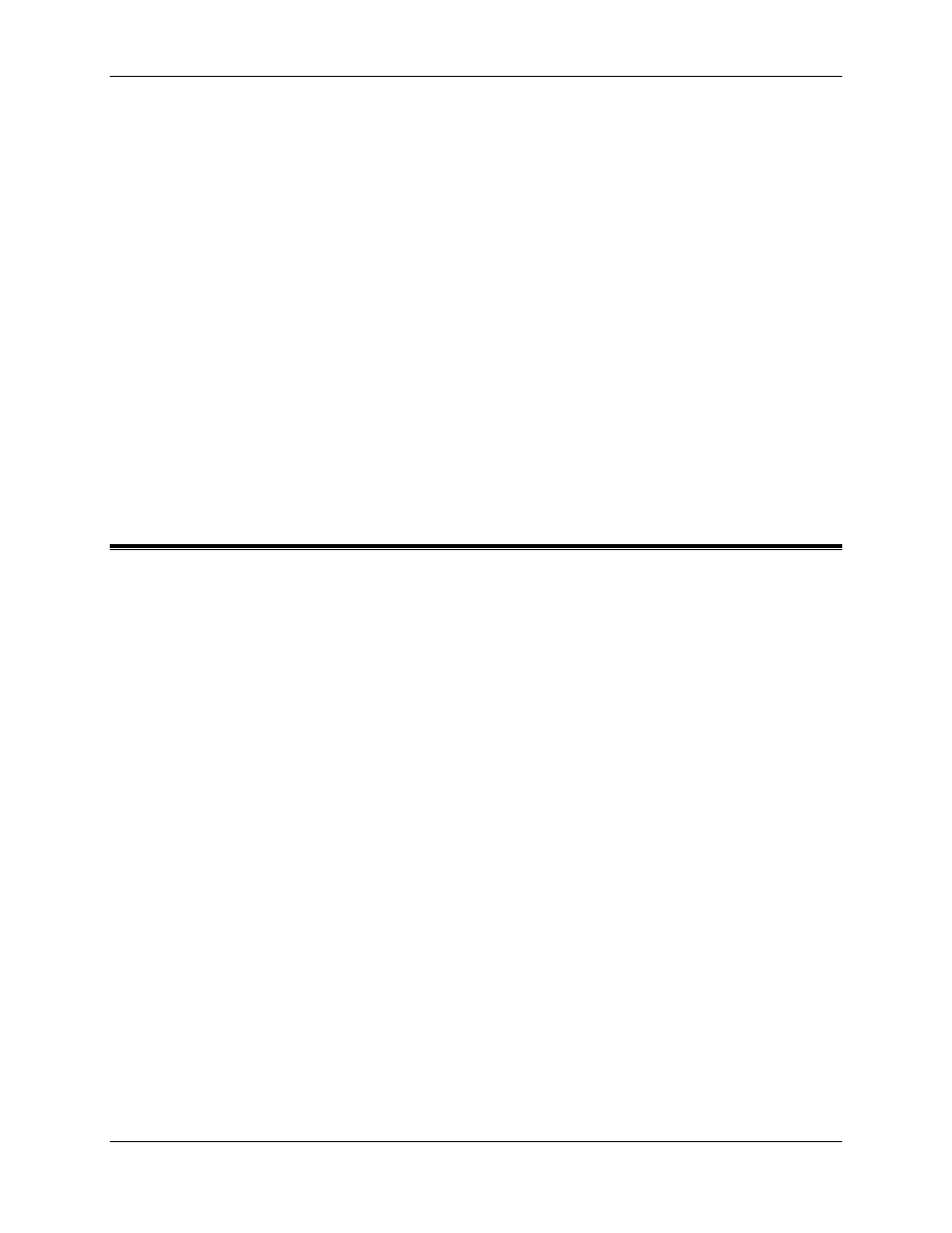
Gearing Axes 4.3
Controller Features
4-3
table in the Flash without storing all the other data in that section listed above. This will not be a
problem as long as you ensure that all data you want to be stored is set correctly before saving
the data in the Flash.
To update the first Flash section, issue the Update Flash (U) command to any axis, or use the
Save to Flash
toolbar button in RMCWin's main or LCD Screen Editor windows.
To update the second (spline) Flash section, use the Save Splines to Flash toolbar button in
RMCWin's Curve Tool window. Notice that this section cannot be updated without using
RMCWin.
While either Flash section is being updated, the green CPU LED will flash. During this time
motion control will continue, but removing the power from the module will result in all parameters
being stored in the Flash to be lost.
The disadvantage of storing configuration data in the motion controller is that, when one module
is replaced with another, the parameters and profiles must be loaded into the new module.
Because of this, all parameters, profiles and event step table data must be stored either in the
control program or in RMCWin files so they can be later transferred to the motion controller when
needed.
4.3 Gearing Axes
Gearing is used when one axis (the geared axis) must move incrementally and proportionately to
another axis (the gear master). This topic describes a method of gearing one axis to another by
using a gear ratio. There are three other types of gearing available, described in the following
topics:
• Sine Move Command
• Follow Spline Segment Command
• Follow Axis with Offset - see the SoftPID Position Move Command
The gear master axis can either be controlled by the RMC (internal) or just a position input from
an encoder or transducer that is not under the control of the RMC (external, also called an half
axis). A numerator and denominator specified in the geared axis's command area determines the
ratio of the movement between the gear master and the geared axis.
The only limitation for gearing axes together is that axes must not be geared in a loop (that is, if
axis 0 is geared to axis 1, axis 1 cannot also be geared to axis 0).
The Gear Master Axis:
An axis does not need to do anything to become the master of a gearing relationship. That is, the
axis may be controlled in open or closed loop, or it may even be only an input (in the case of a
velocity or position reference such as a joystick). The geared axis will select its gear master axis.
Setting up a Geared (Slave) Axis:
The slave axis starts gearing when issued a Go command with the command parameters set up
as follows. It continues gearing until another motion command is issued to the same axis.
1. Specify the Gear Master and Type.