Delta RMC101 User Manual
Page 274
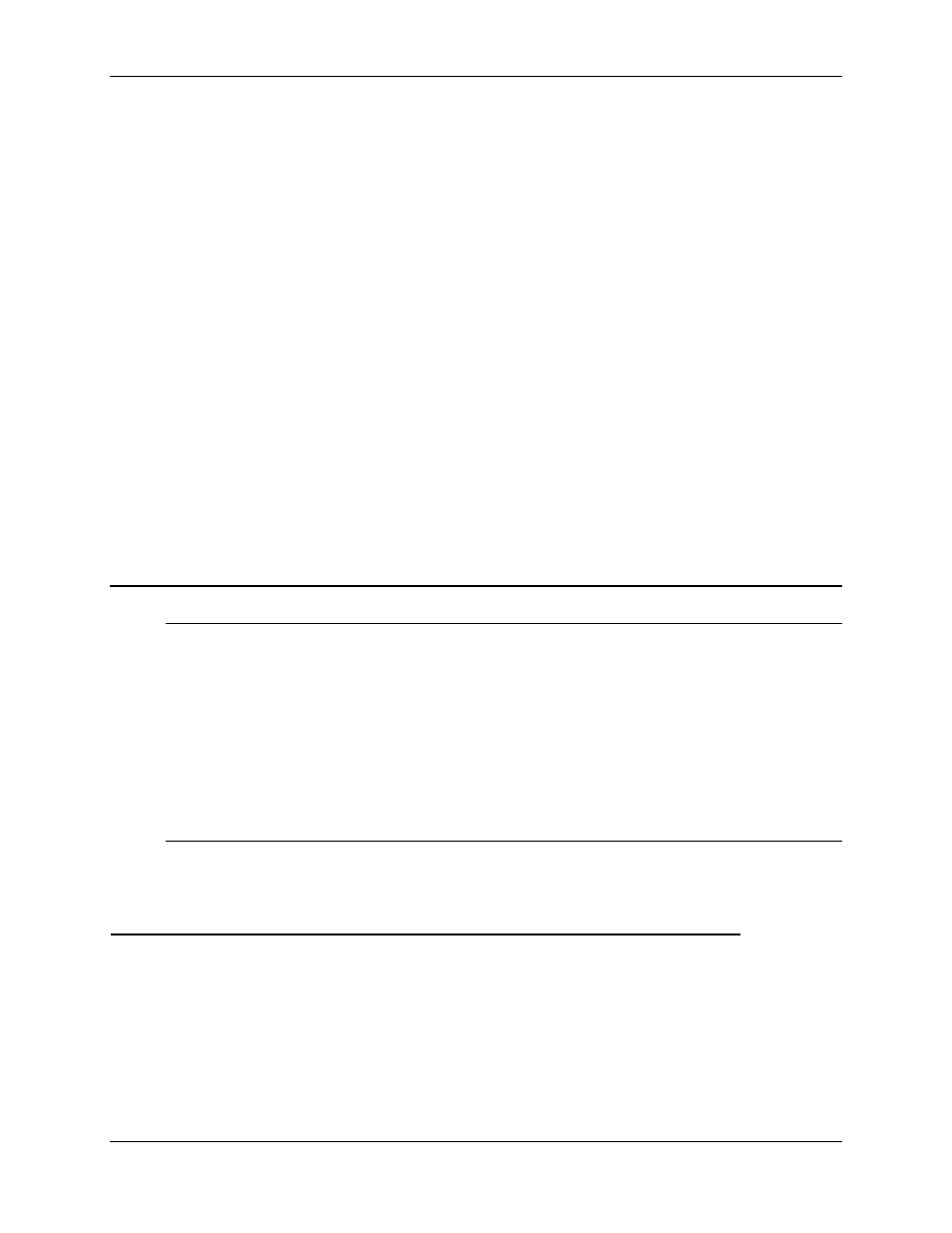
RMC100 and RMCWin User Manual
5-24
7. Click OK.
8. Click Update RMC.
9. The Update Module Configuration dialog box will be displayed to indicate the progress. If the
module could not be reset automatically, you may be prompted to reset the module manually.
To Set the Input Filter
When a new event number is written to an axis, all eight event-number bits plus the trigger bit for
the same axis must be updated simultaneously. This will never happen exactly at the same time,
so an input filter must be used. The input filter setting is used to configure the number of
milliseconds over which all nine inputs for an axis must hold their values before the new value is
considered a command.
User-defined Outputs
As described in Features Shared by All Modes, many of the digital outputs are pre-defined, as
described in that topic. However, under Parallel Event mode, it is often useful to reserve one or
more of these outputs to be triggered explicitly by the event step table (for example, when a
sequence of events finish, an output can be set high). Check the boxes of the output numbers
you wish to reserve for this purpose. Depending on the number of axes your RMC model offers,
one or more of the outputs may be unavailable but checked. Since these outputs are not
predefined the user must define them.
5.1.6.7 Technical Brief: Using the RMC Discrete I/O Command Mode
Abstract
The RMC-DI/O is capable of sophisticated motion control using small and inexpensive
Programmable Controllers with simple discrete I/O. An RMC with a DI/O communication interface
is capable of four discrete I/O interfaces: Command Mode, Input to Event Mode, Parallel Position
Mode, and Parallel Event Mode. Of these four communication modes, Command Mode is the
most flexible; it allows changing parameters and retrieving positions, speeds, errors and other
status information from the motion controller using simple discrete I/O.
This technical brief will compare the four discrete I/O interfaces of the RMC100 series product-
line, describe implementing Command Mode, and finally provide a sample application using
Command Mode.
DI/O Communication Mode Comparison
The following chart lists the advantages and disadvantages of each communication mode. Each
word or phrase in bold print appears in RMCWin’s online help index.
Interface
Mode
Advantages
Disadvantages
Command
Mode
• Any RMC command can
be issued
• Any status information
can be retrieved
(including Actual
Position, Actual Speed,
Drive, Error Bits, and
other Status Bits)
• Requires a PLC
• Requires 2 PLC scans
per command
• Gives commands to only
one axis per command
cycle