Principle of operation, Principle of operation -3, 2 principle of operation – Delta RMC101 User Manual
Page 25
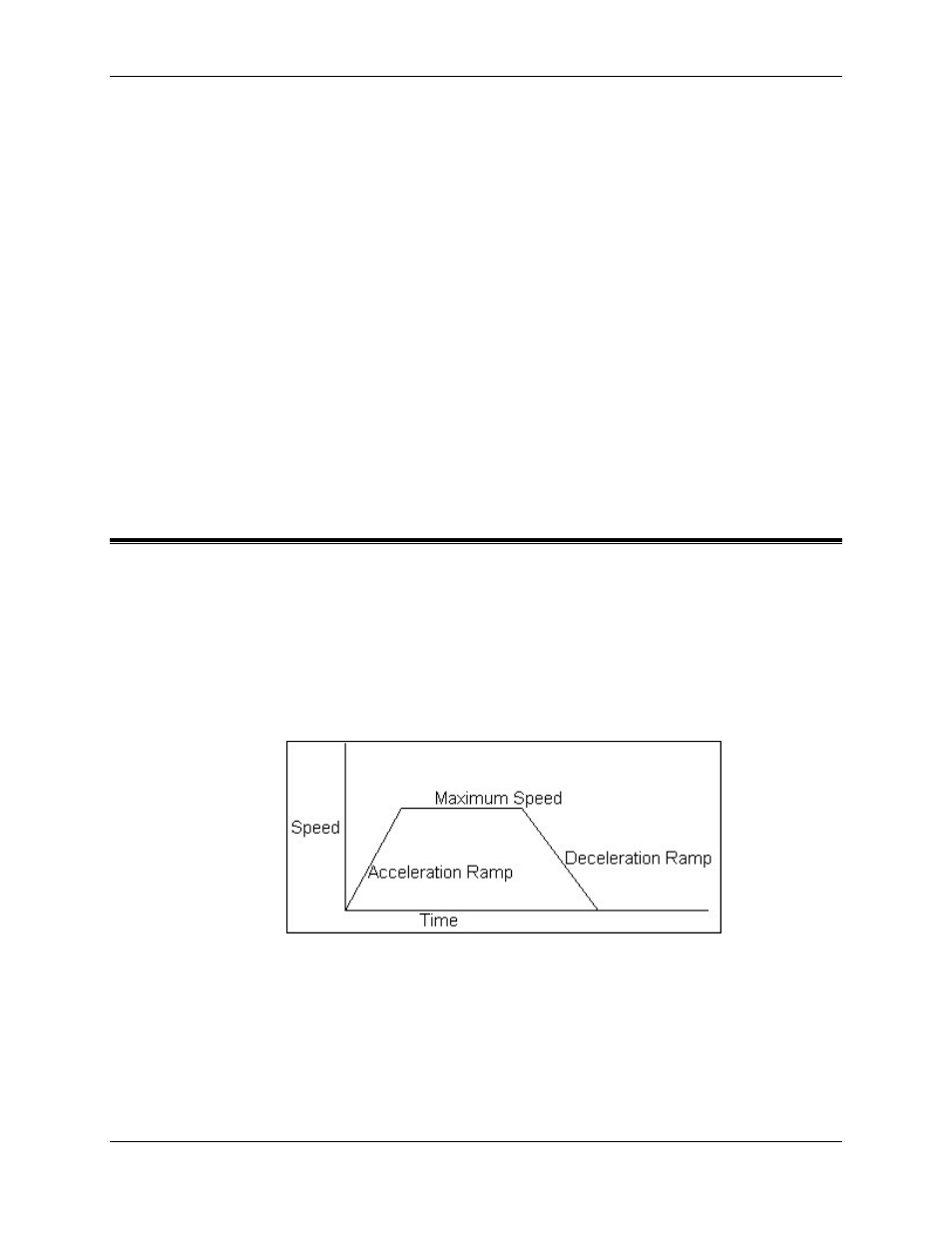
Principle of Operation 1.2
Introducing the RMC100 Series
1-3
• Quadrature Encoders
See Quadrature Overview for encoders for servo motors.
See Stepper Overview for encoders for stepper motors.
• Synchronous Serial Interface (SSI) – Absolute encoders and MDTs
See SSI Overview for all transducers with SSI interfaces.
Pressure/Force Options
• Control pressure or differential force at 12- or 16-bit resolution
• Transition between position and pressure/force while in motion
RMCLink ActiveX Control and .Net Assembly
Control the RMC from your Visual Basic, Visual C++, Java, or VBA (e.g. Excel) programs. See
the RMCLink topic for details.
1.2 Principle of Operation
Control Loop
This motion controller is a targeting controller; the onboard microprocessor updates the Target
Position and Target Speed values each control loop (1ms or 2ms, depending on the number of
modules). For point-to-point moves, Target Positions are generated so the target speed follows a
profile. The Mode, Acceleration, Deceleration, Speed, and Command Value (requested position)
are used to generate the profile. They are specified by the user, and can be changed while the
axis is moving. A trapezoidal profile is shown here.
The Actual Position, measured by any of the RMC’s position transducers, is compared with the
Target Position to determine the position error. Every control loop the position error is used to
calculate the closed loop components of the drive output. It is multiplied by the Proportional Gain
to calculate the proportional component of the drive output. The accumulated position error is
used, along with the Integral Gain, to calculate the integral portion of the drive output. The change
in position error, along with the Differential Gain, is used to calculate the differential portion of the
drive output.