Using parallel position mode, Using parallel position mode -18, 5 using parallel position mode – Delta RMC101 User Manual
Page 268
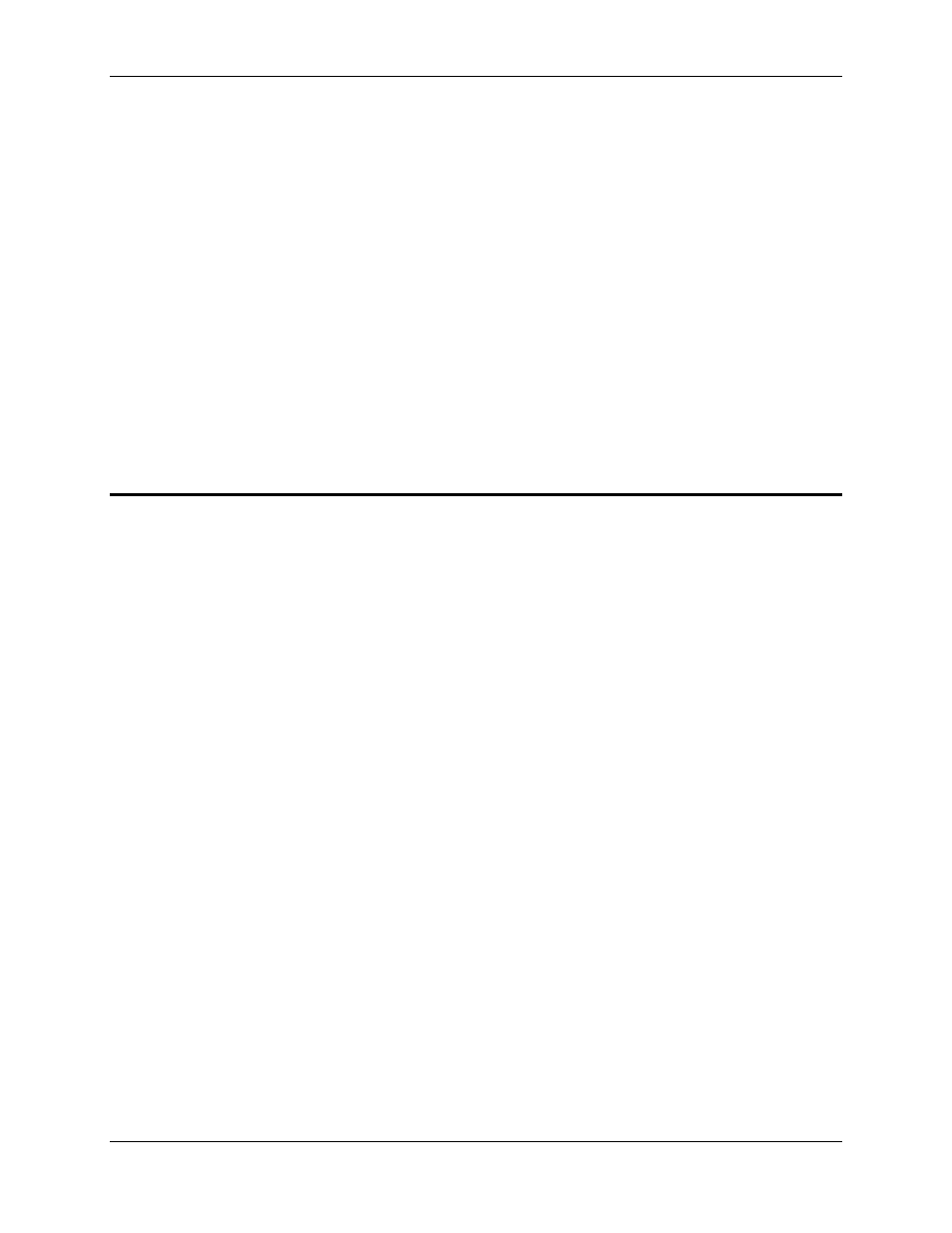
RMC100 and RMCWin User Manual
5-18
1
0
2*
1
1
3*
Axis Select Bits when Quadrature Counter is Used:
CPU
Input
1
Axis
0
0
1
1
* When an axis is selected that is not present on the motion module, the single-axis input is
ignored.
5.1.6.5 Using Parallel Position Mode
In this mode, the user can give simple Go and Open Loop commands using discrete inputs. Refer
to Features Shared by All Modes for details on input and output assignments that are common to
all modes.
Basic Operation
Before any moves may be made, you must do the following to store the proper parameters. It
only needs to be done once because the parameters and profiles will be read from the Flash on
power up:
1. Tune the axes by adjusting the parameters.
2. Set up the Profile table to hold all the motion profiles you plan to use (including MODE, ACCEL,
DECEL and SPEED). Refer to the charts above for determining which profiles you will use.
3. Save the parameters and profiles to Flash using the Update Flash command. This command can
be sent from RMCWin.
You must do the following on each power up to initialize all the axes:
1. Energize the Run/Stop bit (CPU input 0).
2. Wait for the Ready bit (CPU output 0) to go to a logical 1.
You must continue to hold the Run/Stop bit high. If a move is in progress when you make the
Run/Stop
go low, the move will stop immediately. If a move is requested when the Run/Stop is
low, the request will be ignored.
To request a move, you must select the axis and profile using Digital inputs 16-17 and CPU input
1. You must also set the position or drive on Digital Inputs 0-15. These must all be done
simultaneously. The new value is not processed until all axis, profile and position/drive select bits
have been held at the same values for the duration set by the Input Filter field described below.
At this time if any of the values are different from the last command, then a new command is
issued.