Delta RMC101 User Manual
Page 280
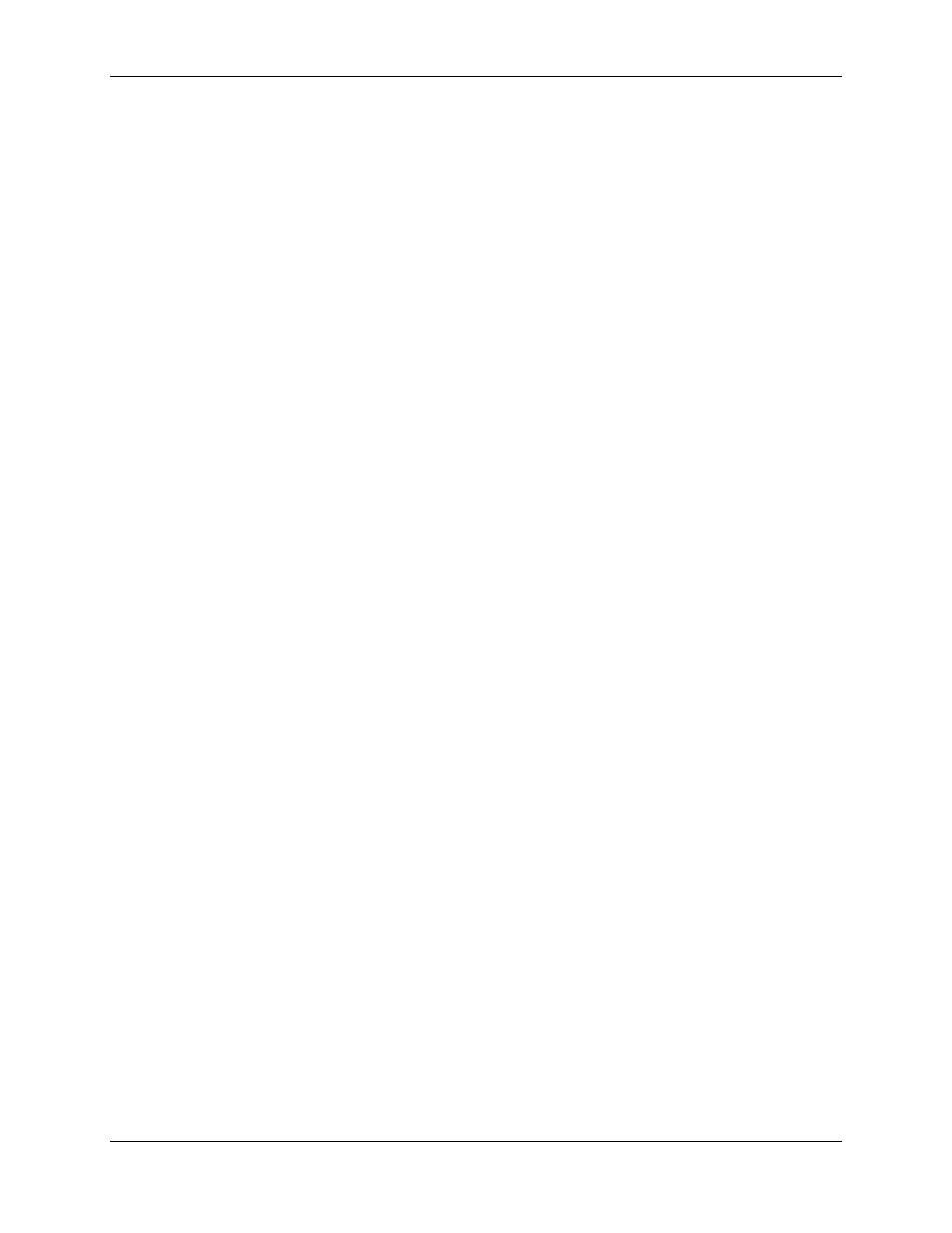
RMC100 and RMCWin User Manual
5-30
good reference for this information.
Input to Event mode does not require multiple inputs to be switched simultaneously. For this
reason, many applications can use the RMC without a controlling PLC. The following points
describe the operation of Input to Event mode:
• Parameters and tables used by the RMC are configured using the RMCWin software and stored
in the RMC Flash memory.
• All axes are initialized by raising the Run/Stop (CPU input 0) line on the RMC, and all axes are
immediately stopped by the falling of the Run/Stop line. Therefore, the Run/Stop input is often
connected to the system’s emergency-stop button.
• The Ready (CPU output 0) line echoes the Run/Stop input line to notify the controlling system
when the RMC is initialized.
• When the Run/Stop line is raised and a Trigger (DI/O inputs 0-15) input rises or falls, the Input to
Event table is used to determine which axes receive an event sequence.
The Input to Event table has a row for each edge (rising and falling) of each Trigger input (32 rows
total). Each of these rows has a field for each axis; each field may either be left blank or hold an
Event Step number (0 to 255).
When an edge occurs on a Trigger input, each axis’s field in the row corresponding to the input
edge that took place is checked. For each field containing a valid value, the axis starts executing
the event sequence beginning with the Event Step number given by the Input to Event table entry.
• Each time the Run/Stop or a Trigger input transitions, the Acknowledge (CPU output 1) line
toggles. Stand-alone applications generally ignore this, but PLC-controlled applications may wish
to use this signal.
• The eight Status outputs (DI/O outputs 0-7) default to being used for the following:
•
DI/O
Output
#
2-4 Axis
RMC’s
5-8 Axis
RMC’s
0
Axis 0 In
Position
Axis 0 In
Position
1
Axis 1 In
Position
Axis 1 In
Position
2
Axis 2 In
Position
Axis 2 In
Position
3
Axis 3 In
Position
Axis 3 In
Position
4
Axis 0 Stop
on Error
Axis 4 In
Position
5
Axis 1 Stop
on Error
Axis 5 In
Position
6
Axis 2 Stop
on Error
Axis 6 In
Position
7
Axis 3 Stop
on Error
Axis 7 In
Position