Delta RMC101 User Manual
Page 296
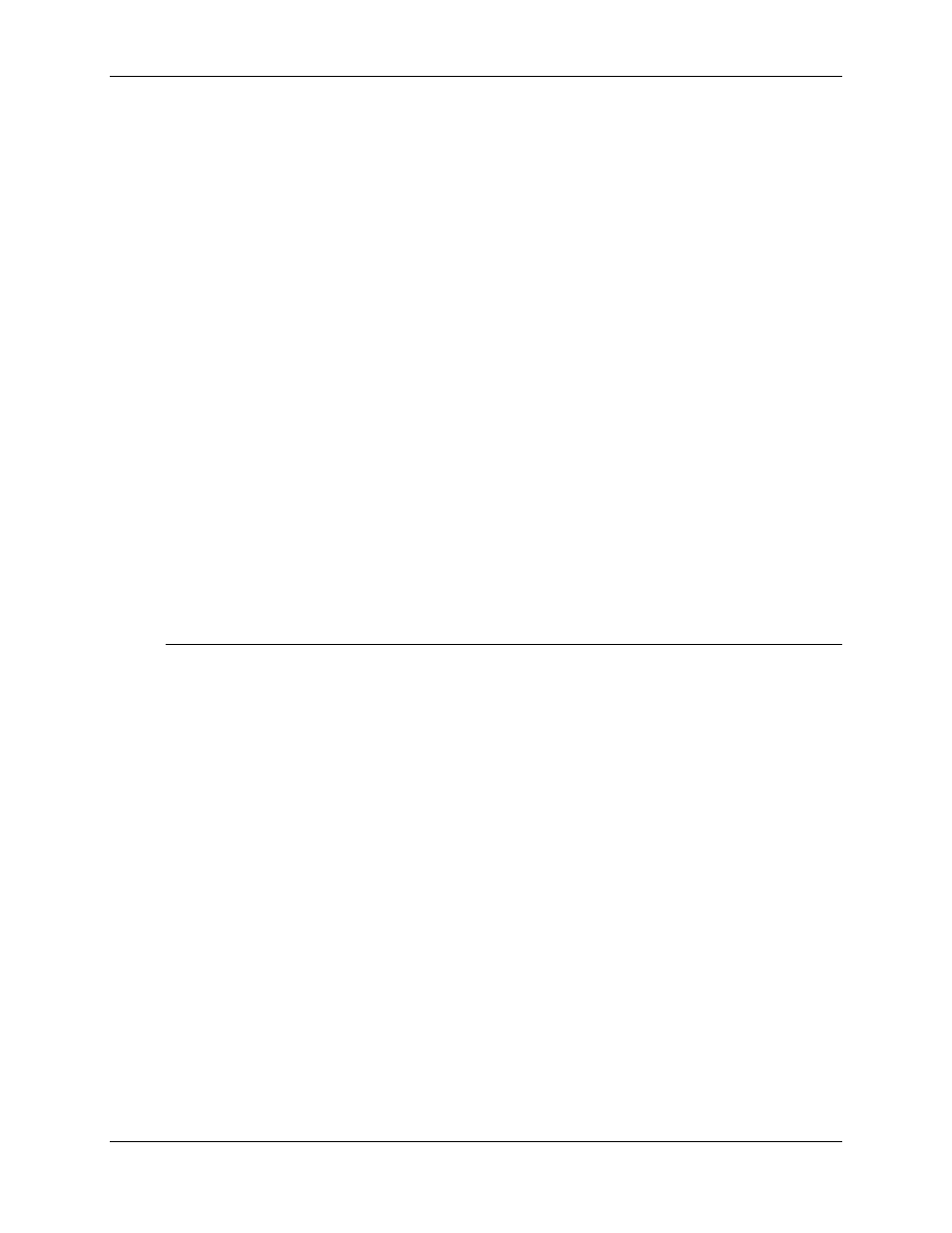
RMC100 and RMCWin User Manual
5-46
5. If you need to invert any inputs or outputs to match your hardware, select the appropriate
check boxes in the Invert inputs and Invert outputs areas.
6. Click Mode options.
7. In the Input Filter box, enter the number of milliseconds you wish to have the RMC wait for
the inputs to settle. You may need to change this more than once if you are not sure how
long you should delay. If you don’t need the speed, it may be wise to be conservative and
select 20ms.
8. If desired, you may select to control any of the outputs by selecting the appropriate User-
controlled outputs check boxes.
9. Click OK.
10. Click Update RMC.
11. The Update Module Configuration dialog box will be displayed to indicate the progress. If the
module could not be reset automatically, you may be prompted to reset the module manually.
4. Wire, Test, and Tune the System
Wiring and testing should follow your design. Tuning the system is described in the RMCWin online
help. Be sure to save your tuning parameters both in the RMC Flash memory and on disk from
RMCWin.
Sample Application
The customer needs a single axis to move between two positions. The user will select one of ten
different positions to which the cylinder will extend and then retract back to a home position. The
home position will be defined at 0”. The ten extend positions are required by different products
that may be produced and are known ahead of time (half-inch steps between 4” and 9.5”). The
user wishes to use a thumb-wheel to select the set (sequence) and a button to initiate the motion.
We will assume that the customer decided 5 inches per second was the maximum safe extension
speed, and that 10 inches per second was the maximum safe retracting speed.
1. Design the System
The RMC controls based on the transducer or encoder counts received. However, counts rarely
correspond to meaningful engineering units. Therefore, the RMC allows the user to convert counts
into meaningful position units by using Scale and Offset parameters. Refer to RMCWin’s online
documentation for details. In this application, the position units used will be thousandths of an inch.
Therefore, speeds will be given in thousandths of an inch per second.
Because only one axis of MDT feedback is used, the smallest RMC module available—an
RMC100-M1-DI/O module—will be used.
Using Parallel Event mode, the thumb-wheel can be used to trigger an event sequence and will
select the starting event step number. The following wiring diagram is used: