Delta RMC101 User Manual
Page 352
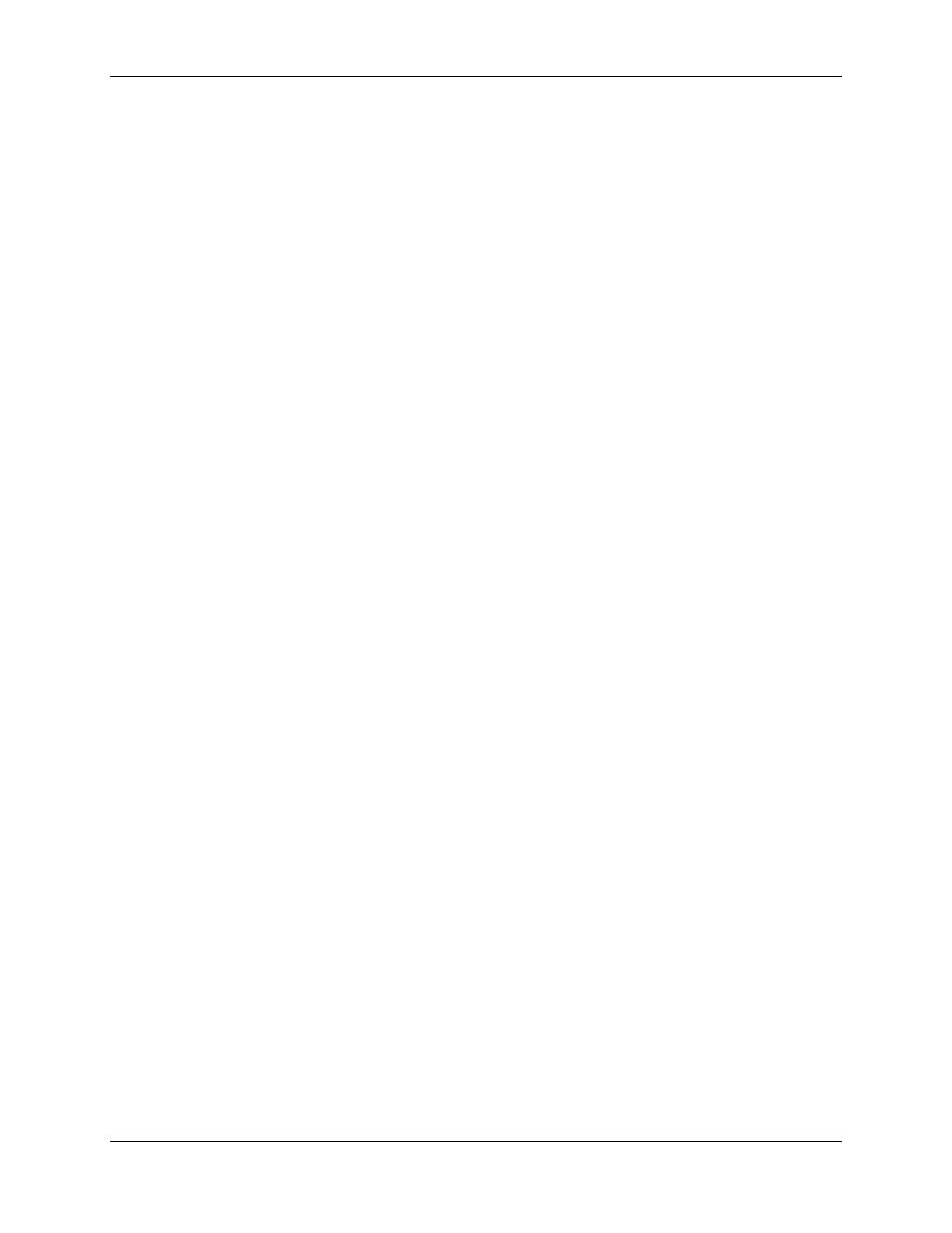
RMC100 and RMCWin User Manual
5-102
for details.
1
10
Axis 0 Status.
These ten registers correspond to the ten
status registers displayed in RMCWin for an axis.
11
10
Axis 1 Status.
Same as for axis 0.
21
10
Axis 2 Status.
Same as for axis 0.
31
10
Axis 3 Status.
Same as for axis 0.
41
10
Axis 4 Status.
Same as for axis 0.
51
10
Axis 5 Status.
Same as for axis 0.
61
10
Axis 6 Status.
Same as for axis 0.
71
10
Axis 7 Status.
Same as for axis 0.
The Input Data is updated and sent at the RPI by the RMC regardless of the state of the Sync
Registers. As described below under Using the Sync Registers, the Sync Registers only apply
when issuing commands.
Using the Sync Registers
The RMC ENET does not look at the command registers in the Output Data it receives until the
Sync Out Register changes. When this register changes, then all commands for all available axes
are processed.
The Sync In Register will change to match the Sync Out Register after the command(s) have
been received by the RMC and the status registers in the Input Data have been updated.
Sync Registers are used for the following reasons:
• To avoid splitting up of commands issued to the RMC.
Example:
The ControlLogix does not synchronize its I/O with the PLC scan. Therefore, in the time it takes to
place values in the command words for one or more axes, the Output Data could be sent out to
RMC, mixing some old and some new data. By having the RMC ignore command changes until
the Sync Out Register changes, this problem is avoided.
• To coordinate when the status in the Input Data has been updated to reflect a command that was
issued.
Example:
Suppose an axis is in position, and therefore the In Position bit is set in the axis's Status word.
The PLC sends a Go (G) command to this axis to move it to another position. As soon as this
command is received by the RMC, the In Position bit will be cleared, and it will not be set again
until the axis reaches the new position. However, if the In Position bit in the Input Data is checked
before the client receives Input Data reflecting the Go command, then the In Position bit will still
be set, possibly leading the PLC program to think the axis is in-position prematurely.
Here is the recommended sequence for issuing commands:
1. Wait until the Sync In and Sync Out Registers match.
If they do not match, then this means that another command or set of commands is in progress.
2. Clear any old commands from the Command registers for each axis.