Controlling speed from a tachometer feedback, Controlling speed from a tachometer feedback -18, 3 controlling speed from a tachometer feedback – Delta RMC101 User Manual
Page 562
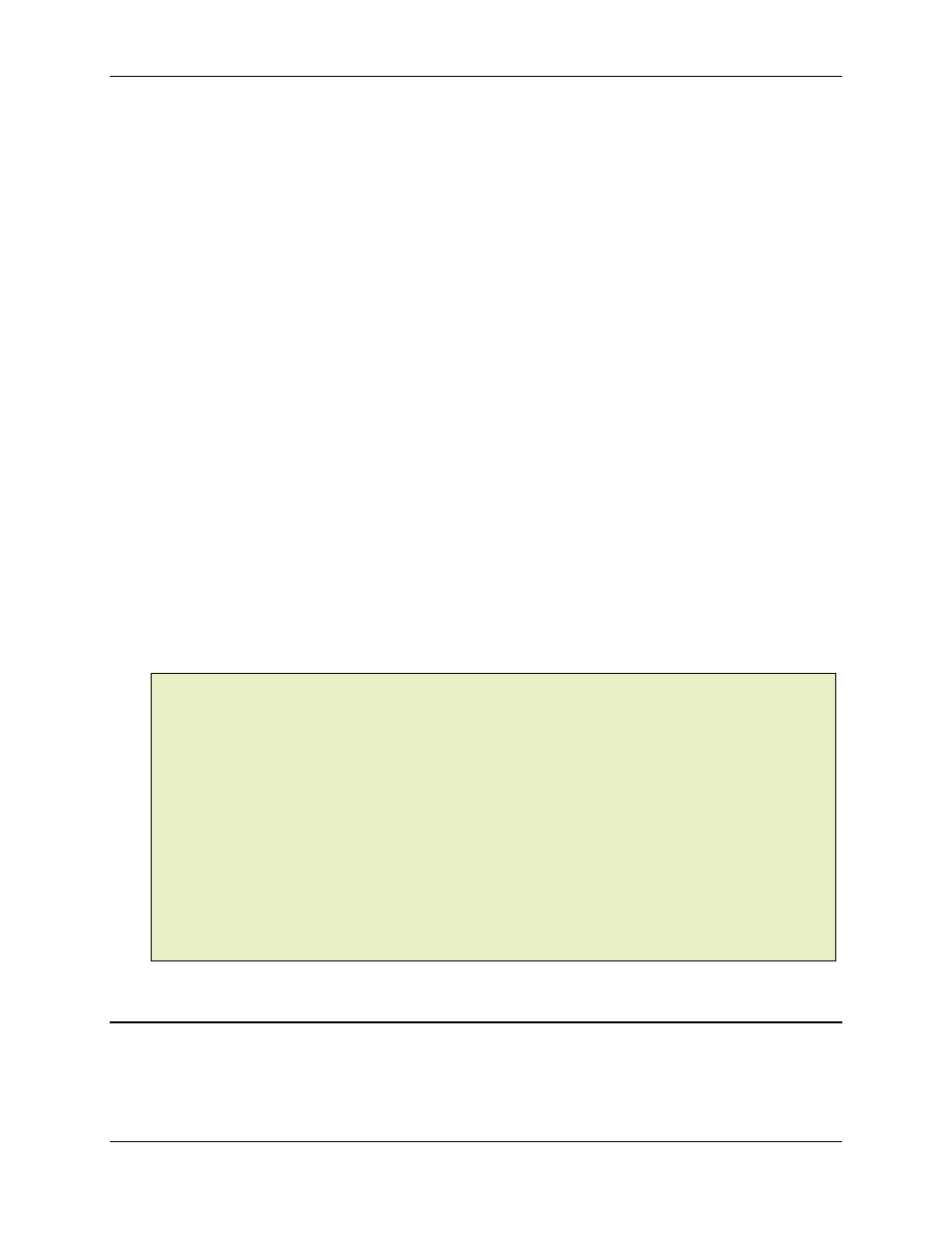
RMC100 and RMCWin User Manual
6-18
Step-by-Step External Target Generation
Follow these steps to set up a system using an external target generator:
1. Assign the Analog Axes
Each of the channels on the analog module(s) must be assigned to a role. The reference input
must be assigned to one of the three reference types (position, velocity, or pressure). Refer to
Analog Transducer Configuration for details on assigning channels.
2. Configure the Reference Input
Analog inputs must be configured to select the type of the input. These options include 0 to 10V,
±10V, 0 to 5V, ±5V, and 4 to 20mA. See Analog Transducer Configuration for details on setting this
value.
3. Configure the Control Axis
See the configuration topic of the transducer type you are using.
4. Determine the Position Units and Limits of the Reference Input and Control Axis
Use the Scale and Offset parameters to select position units on the reference input and control
axis. Remember that these position units will be used in the gearing ratio defined in step 6.
5. Initialize the Control Axis and Reference Input
Send the above parameters followed by a Set Parameters (P) command to the control axis and
reference input.
6. Slave the Control Axis to the Reference Input
Use the Go (G) command to configure the control axis as a gearing slave. This is done by setting
the Gearing bit in the Mode command field, and the numerator and denominator of the gear ratio in
the Command Value and Speed command fields of the Go command. For details on Gearing, see
Gearing Axes.
Note:
This does not align the control axis with the reference axis. It just ensures that any further
moves of the reference input will cause the control axis to move the same amount adjusted by the
gear ratio. You must use a separate move command to align them.
Example:
Suppose you scaled the reference input so it will move between 1,000 and 10,000 position units.
You want the control axis to be geared to the same range. However, after you do steps 1 through
5 the positions of the two inputs will most likely not be equal.
For example, assume the reference input's actual position is 1,500 and the control axis's actual
position is 5,500. If the axes were geared together at this point with a 1:1 ratio, then the control
axis's position will always remain 4,000 position units higher than the reference input's position.
Therefore, you will need to move the control axis's position back to match the reference input's
position before gearing them. The simplest way is to use one of the Move Relative to An Axis
(0xC0-0xCF) commands to move the command axis relative to the reference input.
6.1.8.3 Controlling Speed from a Tachometer Feedback
In addition to controlling speed with position feedback, the RMC100 is able to control speed with
a tachometer feedback. To do this, an analog module with drive outputs is required. For details
on configuring the module for your control and transducer type, refer to Using Analog Channels
as Velocity Inputs, and Configuring the Analog Transducer Type.