Delta RMC101 User Manual
Page 211
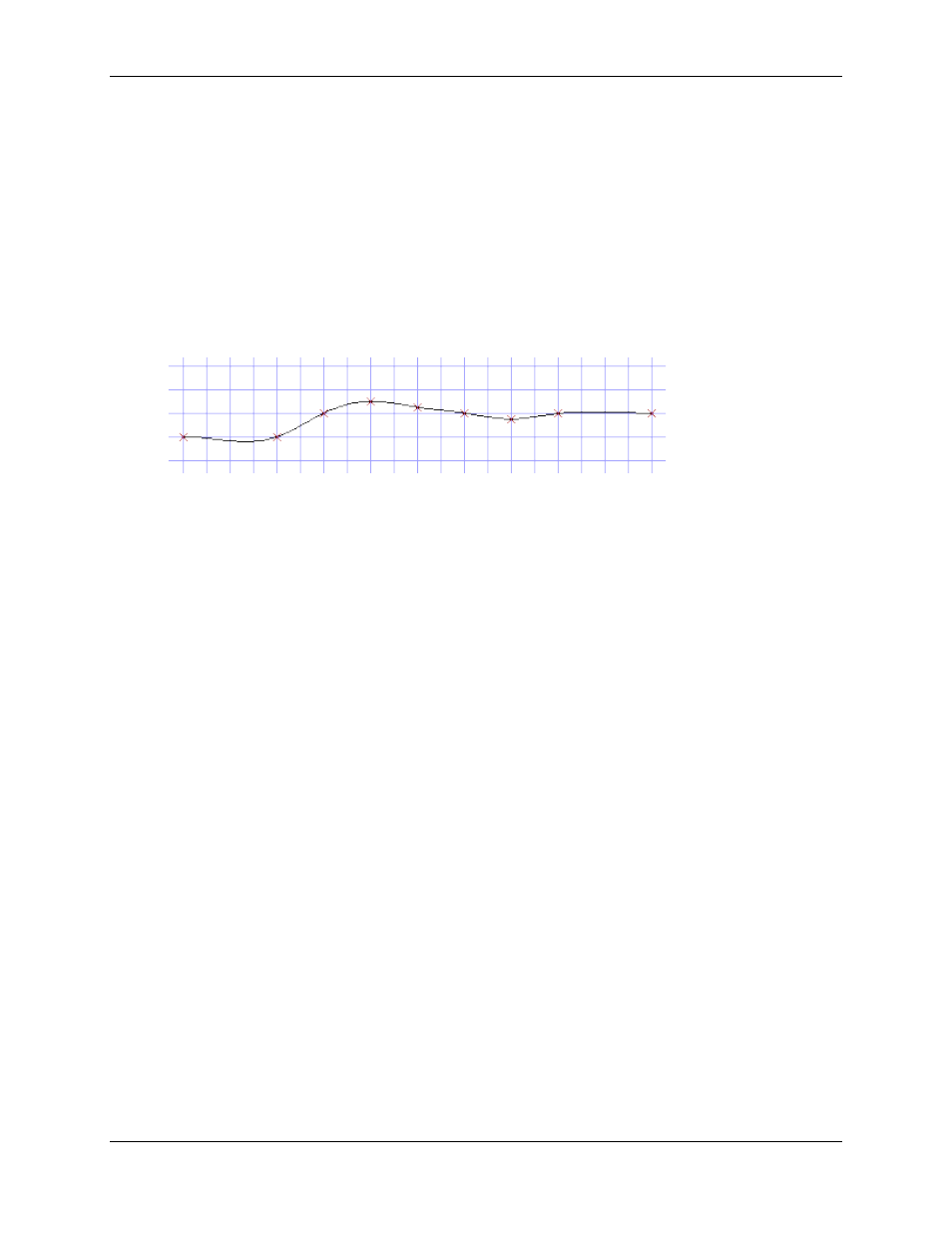
Spline Overview 4.8
Controller Features
4-25
X
61000
Send 7th scanned value.
x
61000
Send trailing point.
T
0
Signal end of the segment.
In this example, notice that the case of the Add Spline Point (X) command is toggled each time it is
used. In order for the motion controller to process a command, it must detect that the command or
command value has changed. Therefore, by toggling the case of the 'X' command, each point will be
processed even if two points have the same value (as is the case with the last two points).
The following graph demonstrates what the loaded spline will look like, with the vertical gridlines
being 100 counts apart and the horizontal gridlines being 1000 position units (1 inch) apart.
Next, suppose an electric eye in front of the saws detects when a cant is about to be cut. A cant
will trigger this electric eye a fixed number of counts before it reaches the blades. In our example,
this eye is 1000 counts in front of the saws. Because of the leading point added to the spline, our
spline begins 400 counts before the cant itself, so we must delay 600 counts from the time the
electric eye detects the beginning of the cant to the time that we begin following the spline.
The programmable controller can take care of this time delay, however it is also possible to
process this input using the Input to Event and Event Step tables in the RMC. To do this, the
output from the electric eye can be run into the motion controller's CPU input 0. CPU output 0 will
then be run back to the programmable controller to indicate when the cut is completed. The entry
in the Input to Event table for this input will hold the Event Step 1. The Event Step table would
look something like this.
Step 1
Step 2
Step 3
Step 4
Command
Value
0x0001
0x0001
0
0x0001
Command
]
0
f
[
Link Type
InputRise
DelayTicks
BitsON
DelayMS
Link
Value
0
600
00001
20
Link Next
2
3
4
1
In the first step, we reset the output to the programmable controller and wait for the input from the
electric eye to trigger. After this occurs, we move to step 2 and delay for 600 counts. After the
delay, event step 3 will be executed, which issues an 'f' command that makes the motion
controller begin following the spline. After the In Position bit of the STATUS word is set, then step
4 is executed. At this point the CPU output 0 is set high and held high for 20 milliseconds to let
the programmable controller know that the cant has been cut. The sequence is then repeated.