Delta RMC101 User Manual
Page 205
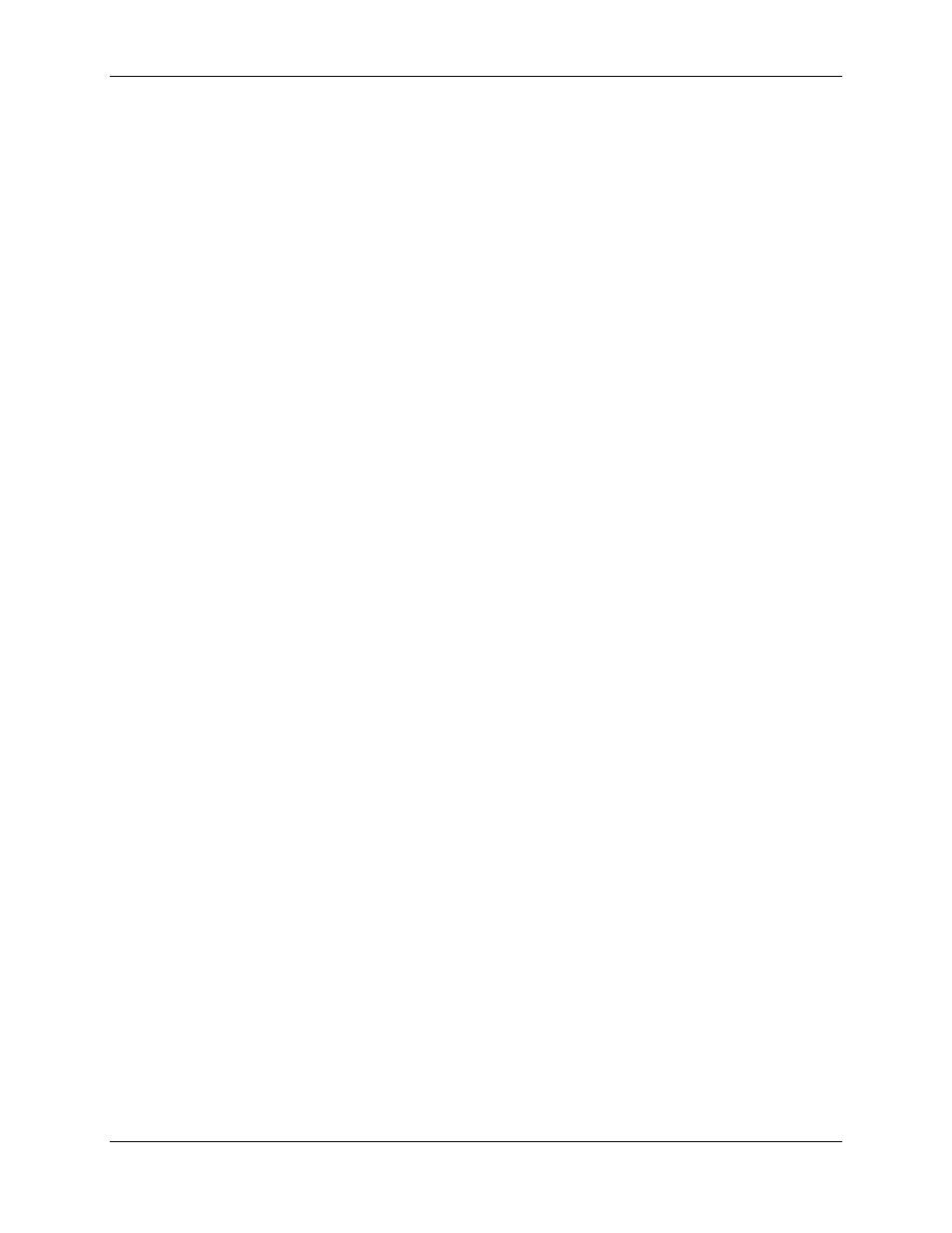
Spline Overview 4.8
Controller Features
4-19
The user defines several spline points for a single curve. In the example shown above, the X's mark
the points set by the user. The horizontal direction in this graph is time and the vertical direction is the
axis position.
Spline Interval:
The user controls the number of master units between the spline points. Master units can be any of
three quantities:
• Master Axis Position Units. If the curve is followed with a master axis selected, then each
master unit will correspond to one position unit on the master axis. See the Follow Spline (f)
and Follow Spline Relative commands for details on following a spline with a master axis.
This is the most common way of following a spline.
• Time. If the curve is followed without a master axis selected, and no Digital I/O module
counter is enabled (see Using Counters), then each master unit will correspond to 1/1024th
of a second.
• Counter Ticks. If the curve is followed without a master axis selected, and a Digital I/O
module counter is enabled (see Using Counters), then each master unit correlates to one
counter tick. This method is largely historical. It is usually better to use the Master Axis
Position Units as master units, but this method was introduced before the RMC's Quadrature
module was available.
The interval between spline points cannot be greater than 65,535 master units or less than 10 units.
Spline Segment:
The RMC can hold several spline curves in its memory at a time; each is called a segment. There is
no exact limit for how many points can be in a segment, but there is a limit for the total number of
points among all segments in the motion controller. This limit is 1023 points per axis on a 2-axis
RMC, 511 points per axis on a 3- to 4-axis RMC, and 255 points per axis on RMCs with five or more
axes.
Standard vs. Enhanced Splines
The RMC supports two types of curves: Standard and Enhanced. Each is described below.
Standard Curves
Standard curves were introduced with RMC CPU firmware dated 19971204. This gave the RMC the
capability of following curves defined by cubic splines. The user defines the position and time of each
point in the curve. The velocities of the endpoints are fixed at zero (0). The velocities of all other
points and accelerations of all points are computed by the RMC to find the smoothest curve through
all points.
There are several deficiencies with Standard curves:
• Because the accelerations are computed at the endpoints, it is likely that they will be non-zero
and therefore result in an acceleration discontinuity and relatively high jerk at each endpoint.
• It is difficult to accurately approximate a linear segment.
• It is difficult to set and maintain a given velocity at a given point.
• The velocities at the endpoints could not be changed from zero (0).