Delta RMC101 User Manual
Page 284
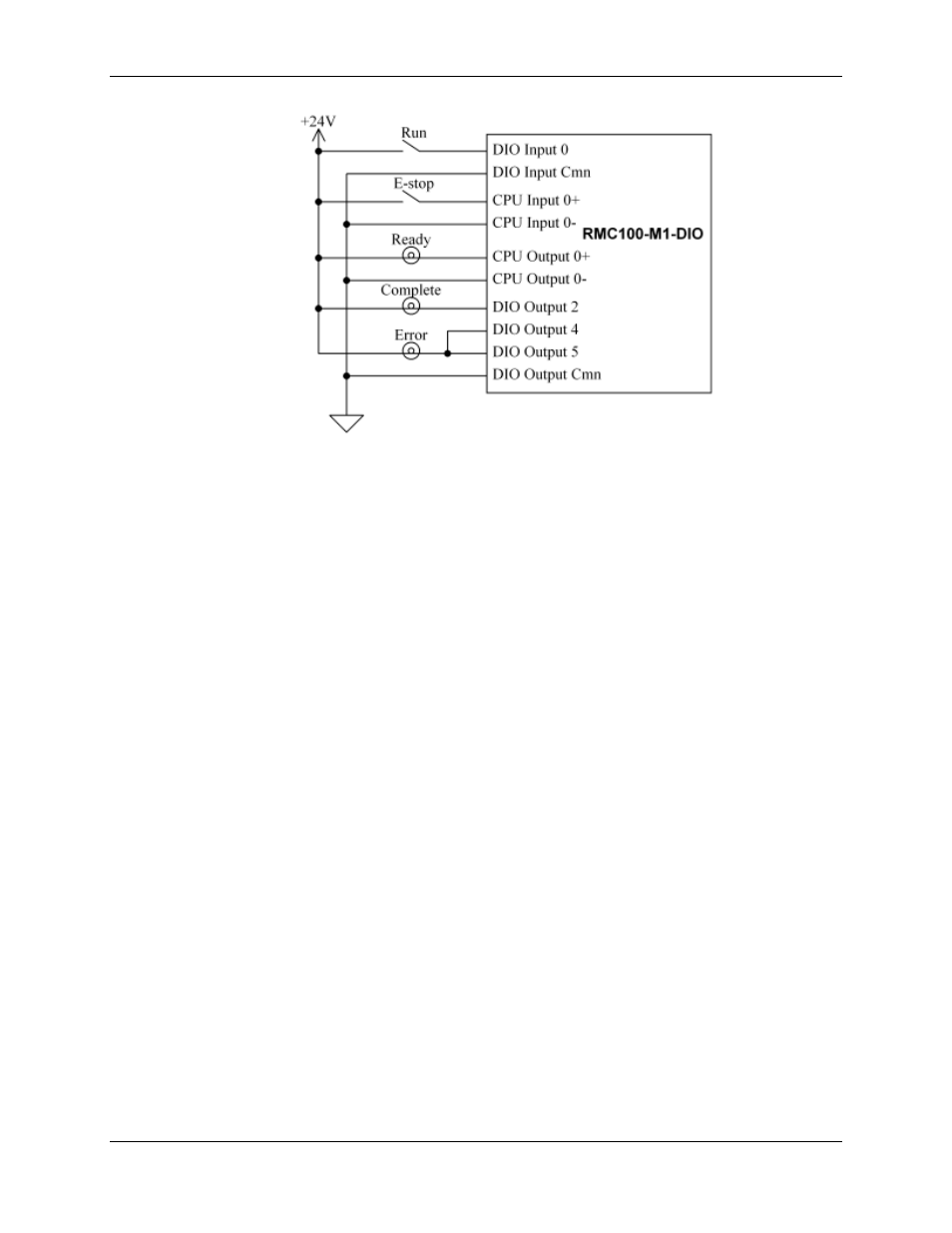
RMC100 and RMCWin User Manual
5-34
Simply by wiring the system, many of the controls are already handled:
o
The E-stop button enables or halts the axes as wired into the Run/Stop (CPU input 0)
input of the RMC.
o
The Ready light works as specified because the Ready (CPU output 0) output on the
RMC is on when the system is not halted by the Run/Stop.
o
The Error light works as specified because it combines the Stop on Error status outputs
(DI/O outputs 4 and 5) of the two axes. Therefore, when either axis has an error, the light
will illuminate.
2. Program the Event Step Table
We now need to write an event sequence that will generate the desired sequence on the two axes
and turn on DI/O output 2 to illuminate the Complete light at the end. A complete listing of available
commands can be obtained from RMCWin’s online help. The following event sequence will be
used to control both axes:
Each step is described below, beginning with the first step that will be executed:
1. A Reset Outputs (]) command is issued. Its hexadecimal Command Value indicates
which bits to reset. Therefore, bit 2 (hexadecimal 00004) represents DI/O output 2. The
DelayMS (D) link type and its 0 link value indicate to delay 0 milliseconds and then go to
step 2.
2. Both axes are commanded to Go (G) to 250 position units. The AxesInPos (A) link type
waits until axes 0 and 1 are both in position, and then goes to step 3.
3. Both axes are commanded to Go (G) to 10,000 position units. The AxesInPos (A) link
type waits until axes 0 and 1 are both in position, and then goes to step 4.
4. A Set Outputs ([) command is issued, which turns on DI/O output 2. The event sequence
then ends by going back to event step 0.
5. This step ends the event step sequence because it has no link type.