No initialized pressure axis is assigned, 44 no initialized pressure axis is assigned – Delta RMC101 User Manual
Page 641
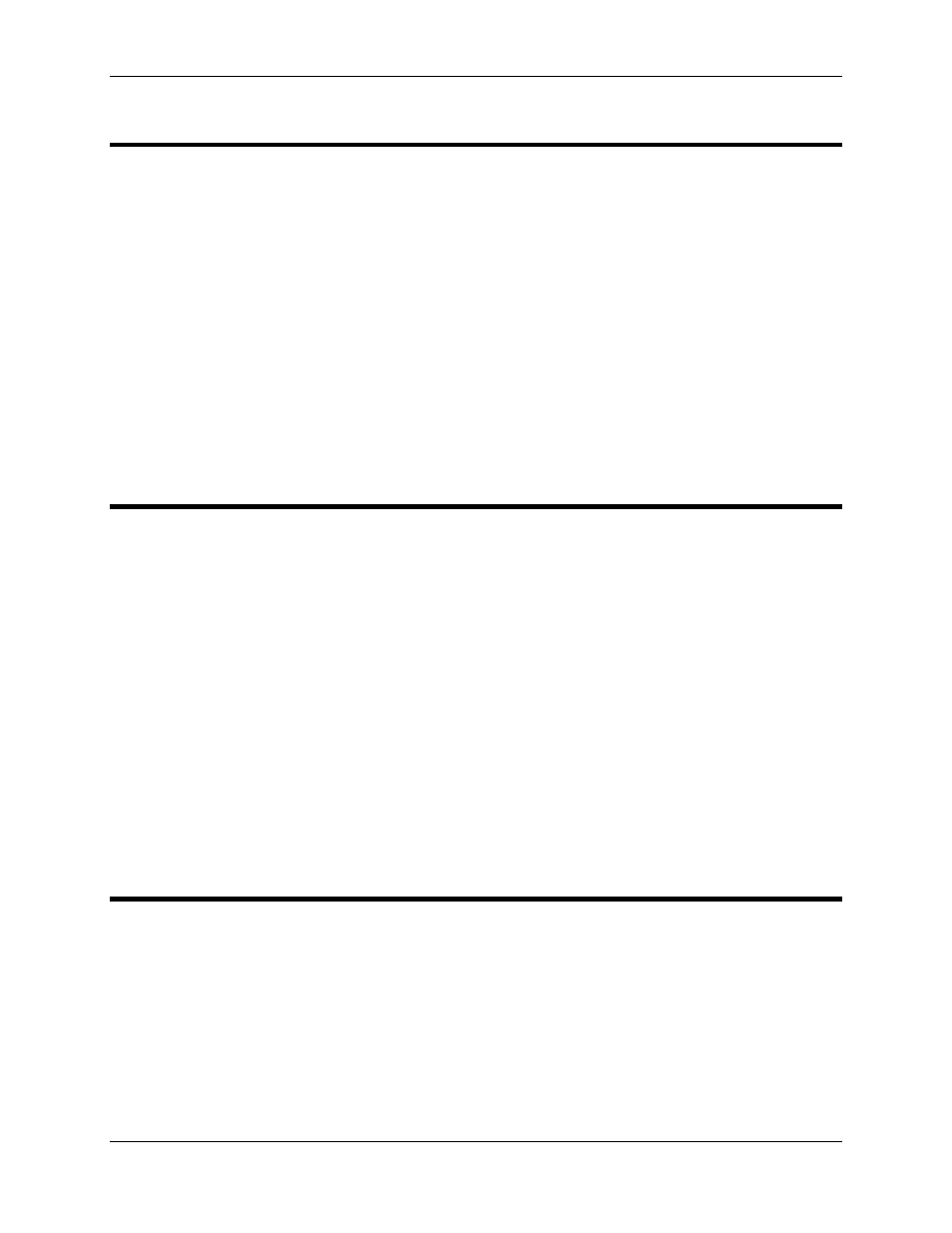
Parameter Errors 7.4
Support and Troubleshooting
7-17
7.4.44 No initialized pressure axis is assigned
This parameter error occurs when a move is started with the Monitor Pressure bit set in the
MODE word, but either no pressure axis assigned to the position axis, or the pressure axis
assigned has not been initialized. Consider the following three possibilities:
• Did you intend to set the Monitor Pressure bit in the MODE word? If not, then you should open
the MODE word popup editor in RMCWin and clear the Monitor Pressure check box.
• Have you assigned a pressure axis to the pressure axis? To verify this, check the CONFIG word
to see if a pressure axis has been assigned. Make sure that you’ve issued a Set Parameters
command to send the current parameters to the motion controller.
• Have you initialized the assigned pressure axis? You must send a Set Parameters command to
the pressure axis as well as the position axis.
For more details on controlling pressure, refer to Controlling Pressure or Force.
7.4.45 Non-existent pressure axis selected in "Config" word
This parameter error indicates that the CONFIGURATION word has been set incorrectly.
Specifically, bits 8, 9 and 10 have been set incorrectly. These bits are used to reference the
pressure axis that should be assigned to the position axis. This could occur because of any of the
following reasons:
• There are no analog input modules installed in the RMC that have pressure control enabled.
These are included in the RMC101-series products from Delta Computer Systems, Inc.
• There are multiple axes trying to use the same analog axis. Each pressure axis can only be
assigned to a single position axis.
• The pressure axis number selected is larger than the number of pressure axes available. For
example, in an RMC101-M1-A1 with the four pressure channels configured as two differential
force axes, only pressure axes 0 and 1 can be selected, and attempts to access pressure axis 2
and 3 (using CONFIGURATION values of 0x0A00 and 0x0B00) will generate this error.
7.4.46 Numeric overflow while sending a spline to the Spline
Download Area
The last sequence of points sent to the Spline Download Area resulted in a numeric overflow.
This will only happen if your points are positioned such that speeds and accelerations for the
spline curve would have been too high. Try increasing the time (or master counts) between
points, or reducing the distance (in position units) between points.
The spline you were attempting to download will not succeed. You should restart sending the
spline at the first point.