Delta RMC101 User Manual
Page 895
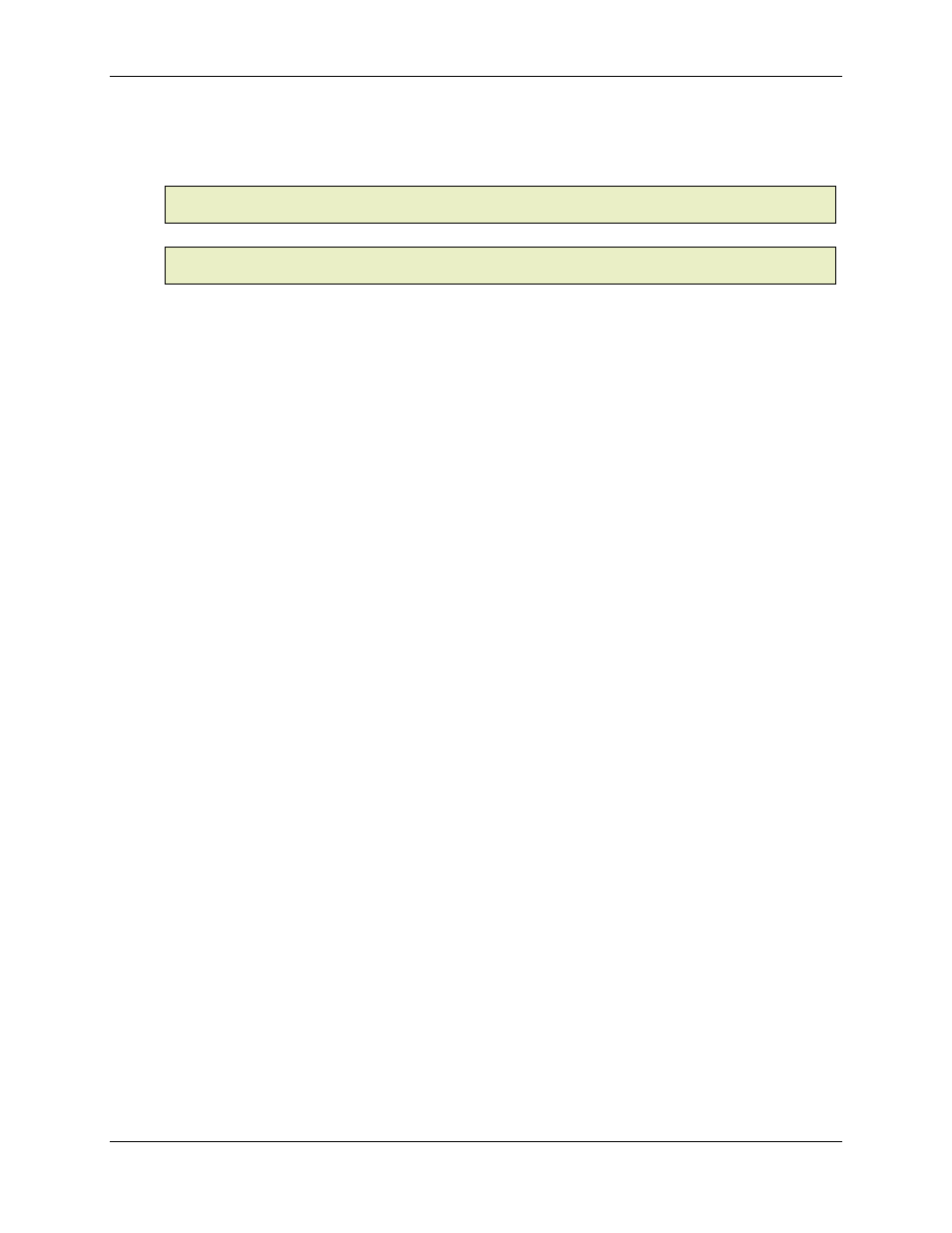
Appendix E: Event Step Link Reference
E-5
from the master. When this value is changed, the link type copies it into the Extended Link Value,
so a new value must be written to the Link Value each time.
Note:
The Extended Link Value is also used by the Skew Detection (<) link type. Care must be
taken to ensure that these link types are not used on the same axis.
Note:
Because the Extended Link Value powers up with 0, starting with a Comm Trigger (C) link
value of 0 will cause the event sequence to wait the first time it encounters this link type.
Example:
Step 10
Step
11
Step
12
Mode
0x0000
0x0001
0x0001
Accel
0
10
10
Decel
0
10
10
Speed
0
1000
1000
Command
Value
0
4000
5000
Command
G
G
Commanded
Axes
Default
Default
Default
Link Type
CommTrig
BitsON
BitsON
Link Value
0
1
1
Link Next
11
12
10
This example is an axis making two moves. Suppose the PLC wants to control these moves by
downloading the step sequence to the RMC. Here is how this can be done:
• The RMC starts this sequence running on axis 0. That axis will first encounter the CommTrig (C)
link type and wait until the Extended Link Value or Link Value change, since both are zero.
• The PLC waits until the axis is not running either step 11 or 12.
• The PLC downloads values to these two steps. These values can include, but are not limited to,
accelerations, speeds, and positions.
• The PLC issues a Set Extended Link Value command with a command value of 1 to axis 0.
Alternatively, the PLC could change the Link Value in the event step table itself, but it would
need to write a different value each time.
• The CommTrig (C) link type sees that the Extended Link Value differs from the Link Value of 0,
so it copies the Link Value of 0 into the Extended Link Value and jumps to step 11.