Go command, A.1.18 go command – Delta RMC101 User Manual
Page 671
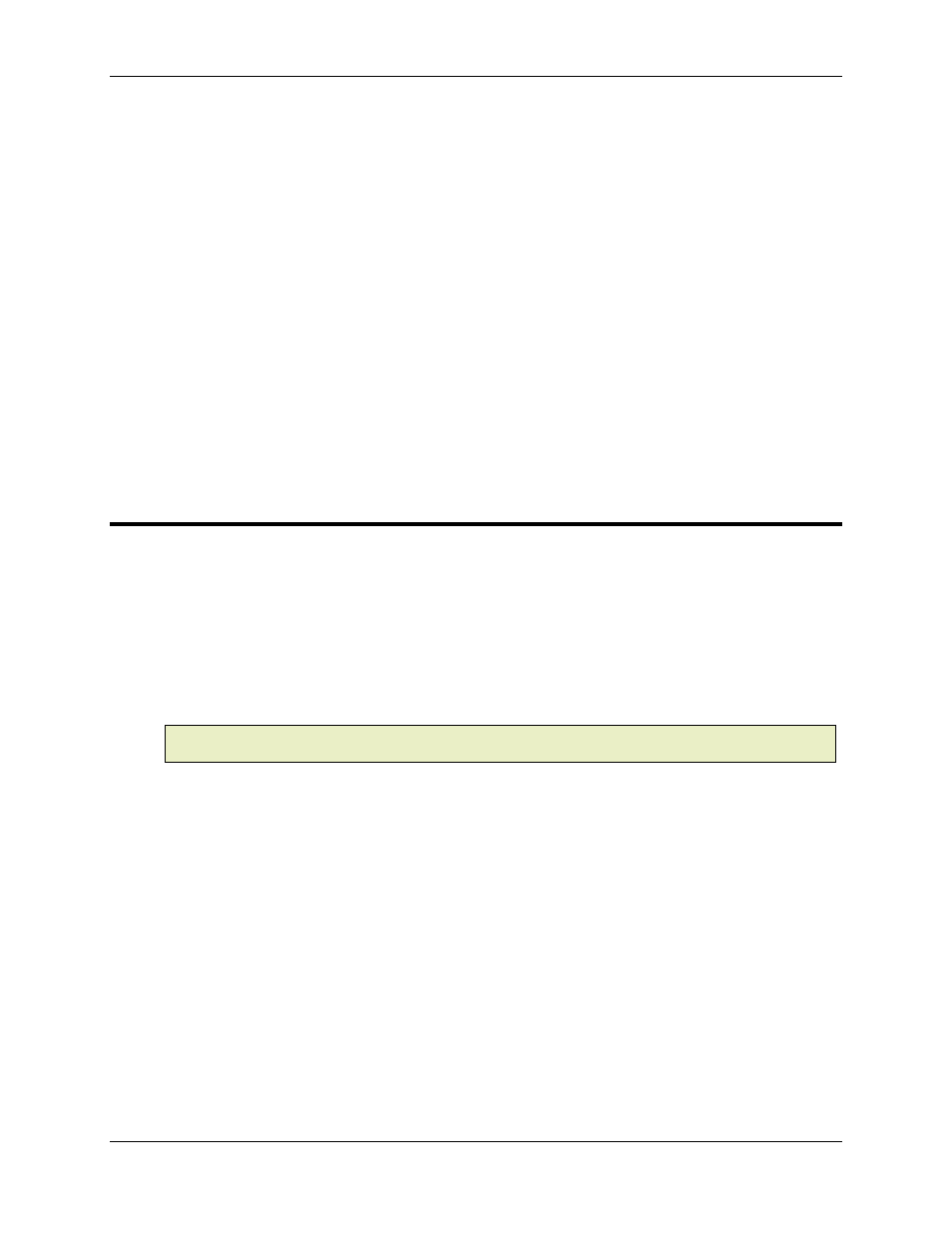
Appendix A: Command Reference
A-19
includes superimposed mode. The above description of this command is appended in the
following ways:
• The Geared Mode bit is used, despite the note about firmware versions.
• The Superimposed Mode bit is used as follows:
o
If set, the move may be superimposed on top of a Geared move, a Speed Control move, a
Sine Move, or another Spline. If cleared, the spline will be the only move. Notice, that if the
axis is stopped, the Superimposed bit may still be used without harm.
o
If set, the Status word’s State A and B bits will not be affected. However, the In Position bit
will be affected. If cleared, the State A and B bits will be cleared during the spline.
o
If set, the entire spline is performed as relative to the current position. Therefore, the entire
spline is adjusted to start at zero position, and then the curve is added to any other motion
being performed on the axis. If cleared, the spline is assumed to be absolute and the axis
must be at the first spline position before beginning the spline. This can be ensured by first
issuing a Go (G) command to the first spline location.
A.1.18 Go Command
Character: G or g
Decimal: 71 or 103
Hexadecimal: 0x47 or 0x67
Command Value: Requested Position, in position units
The Go command will initiate a position move, a speed control move, or a new gear ratio. The
user must make sure that all parameter words are valid when the Go command is issued.
Normally, once the Mode, Acceleration, Deceleration, and Speed are set, only the Command
Value needs to be changed.
Note:
The ’r;G’ command can be given while the axis is in motion. If you do this, the RMC will
ramp to the new speed at the rate specified by the Acceleration and Deceleration parameters.
Bits in the Mode word select the type of move:
Position Control (Rotational bit cleared):
This command moves the axis to the position specified in the Command Value field.
Speed Control with Position Loop (Rotational bit set):
This command requests the axis to ramp up or down to the new requested speed in the Speed
field. The Command Value field indicates the direction the axis should move: 0 represents the
direction of increasing counts (extend or clockwise), -1 represents the direction of decreasing
counts (retract or counter-clockwise). See Speed Control for details on this mode.
The direction can be changed while the axis is moving; the axis will ramp down to a stop and then
immediately ramp up to the new speed in the new direction.