Delta RMC101 User Manual
Page 867
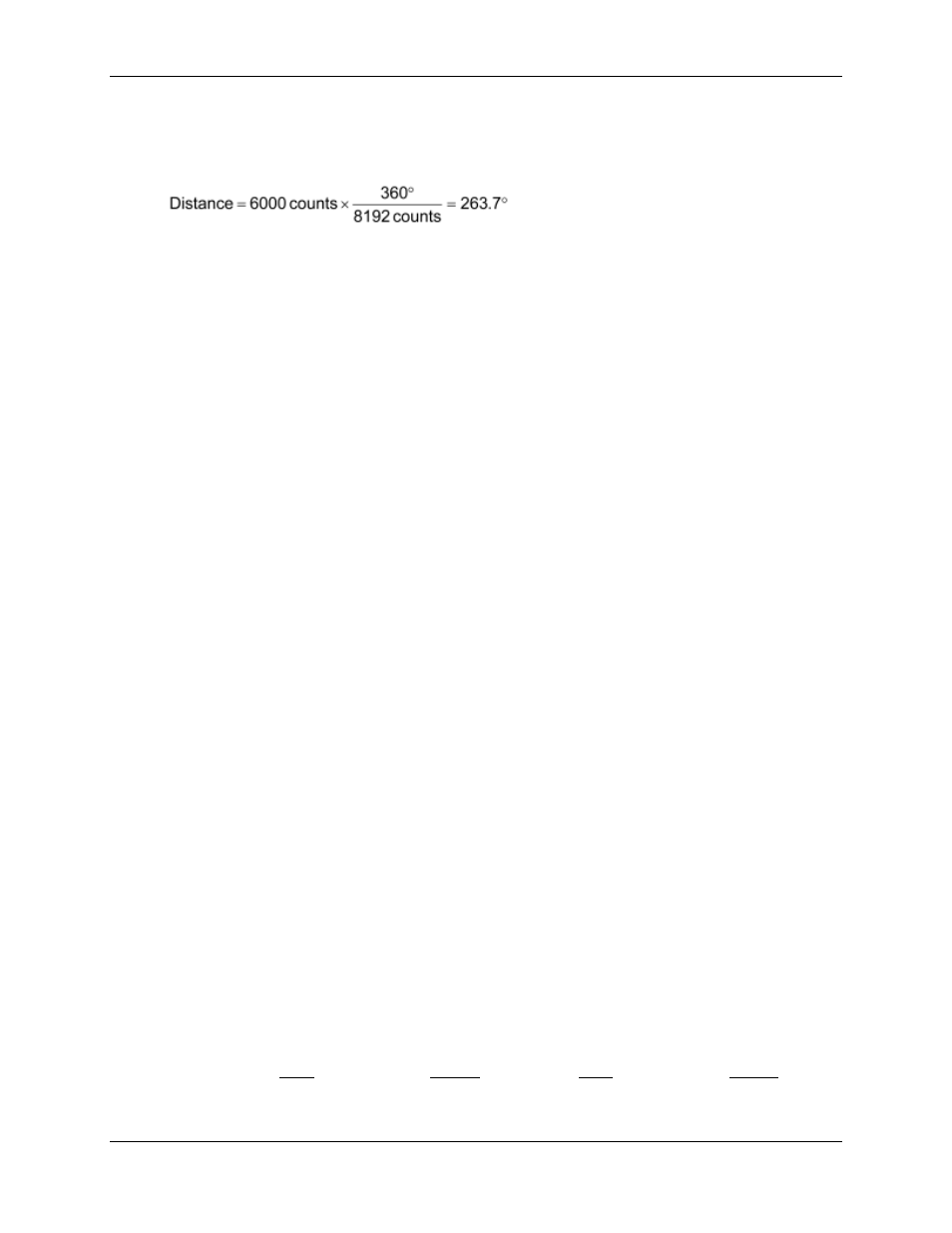
Appendix D: Status Field Reference
D-5
Example 2: A single-turn rotary absolute encoder with SSI feedback has 8192 counts per revolution.
The counts read 6000. The following equation converts the counts to degrees from top-dead-center:
Quadrature
For quadrature devices, the counts increase by one each time an A or B quadrature input toggles
such that the phase of A leads B. The counts decrease by one each time an A or B quadrature input
toggles such that phase of B leads A. The counts are set to zero whenever a position is set by a Zero
Position or Offset Positions command, but are otherwise relative.
Analog
The counts used for analog transducers are defined differently depending on the input range and
quantity type of the channel. The input ranges include 0-10V, ±10V, 0-5V, ±5V, and 4-20mA. Quantity
types include position, velocity, pressure, and force. Pressure, force, and velocity counts are signed
16-bit numbers, which range from 32,768 to 32,767, but position counts are unsigned 16-bit numbers,
which range from 0 to 65,535. Therefore, the charts below treat position counts differently.
There are three error conditions that can be triggered from the counts. These are described below:
• No Transducer
This condition occurs when the value read from the transducer is below a minimum value.
The minimum value depends on the input range and quantity type, and is shown in the
charts below. When this condition is detected, the No Transducer status bit is set, and the
axis will be halted.
• Transducer Overflow
This condition occurs when the analog reading is at its maximum value, which will be 32,767
for all analog axes except analog position inputs, in which case it will be 65,535. When this
condition is detected, the Transducer Overflow status bit will be set. However, the axis may
or may not be halted depending on the configuration of the Auto Stop parameter for this
axis.
• Transducer Noise
This condition occurs only for analog Position Control axes. For these axes, it is triggered
when the transducer feedback jumps by more than 100 position units per millisecond, for at
least six control loops in a row. The reason the value of 100 units/ms was chosen is that a
Position Control can only be commanded in the RMC to move 65,535 units/s, and therefore
64 units/ms. So a feedback speed above 100 units/ms is deemed to be noise. When this
condition is detected, the Transducer Noise status bit is set, and the axis is may or may not
halt depending on the configuration of the Auto Stop parameter.
The tables below list the counts given for the minimum input readings, plus the over- and under-range
readings for each input range.
0 to 10V
Pressure, Force, Velocity
Position
Input
Counts
Input
Counts