Delta RMC101 User Manual
Page 600
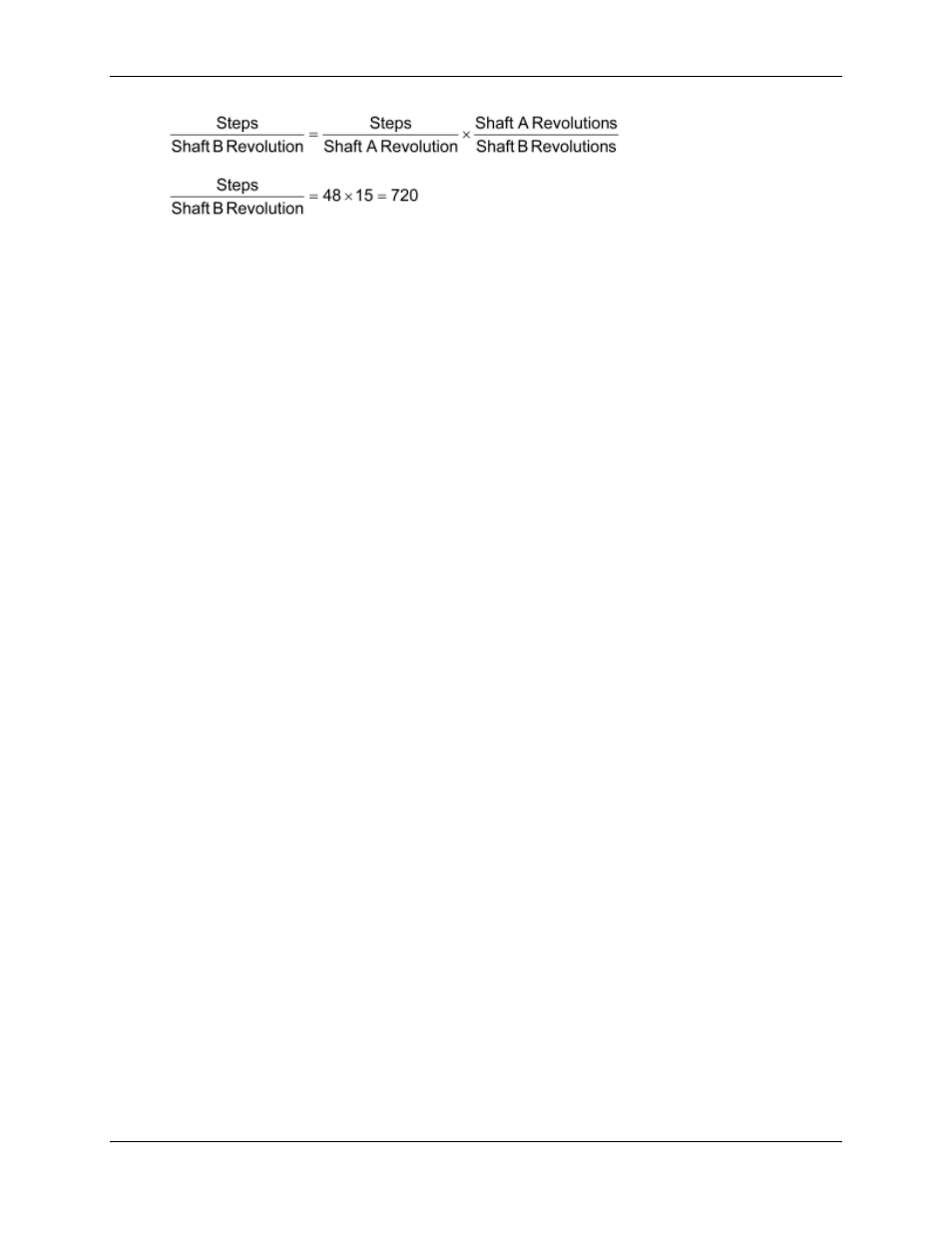
RMC100 and RMCWin User Manual
6-56
Therefore, our parameters should be as follows:
Parameter
Value
Steps/Rev
720
Position Units/Rev
360
Quad Counts/Rev
1024
Therefore, each quadrature count will affect the actual position by 360/1024 of a position unit.
Each target position unit causes 720/360 of a step or 2 steps. Therefore, half of a position unit
causes one step.
Suppose that when these parameters are entered, it is found that the stepper moves in the
correct direction, but the actual positions go backwards. This means that the count to position unit
scale needs to be reversed. As described above, reversing the sign of the Quad Counts/Rev
parameter changes the direction of this scale. Therefore, we would use the following parameters:
Parameter
Value
Steps/Rev
720
Position Units/Rev
360
Quad Counts/Rev
-1024
Example 4:
Suppose we have a stepper motor with 1.8° per step or 200 steps per revolution, and its drive is
configured to have 25 microsteps per step. Therefore, the RMC will need to give 5000 steps to
turn the motor one revolution. A 1000-line encoder is on the same shaft, which generates 4000
quadrature counts per revolution.
The motor moves a belt, and the user wants positions in inches that the belt moves. Therefore,
we need to be able to determine the distance the belt moves per motor revolution. This depends
on the circumference of the drive wheel. If we assume the radius of this wheel is 2.5 inches, then
the circumference is 2 x p x 2.5 inches or 15.70796 inches.
Given this, a first attempt might be to enter the nearest integer in the POS UNITS/REV field, so
our parameters would be:
Parameter
Value
Steps/Rev
5000
Position Units/Rev
16
Quad Counts/Rev
4000
There are two problems with this solution. First, the user sees the position only in inches; no
fractions of an inch will be displayed. Second, the distance reported will be off by 1.825% or
0.292” per revolution, which is unacceptable in most applications, especially those involving
multiple motor turns.