Filter time constant (pressure/force), Drive transfer percent, C.5.13 filter time constant (pressure/force) – Delta RMC101 User Manual
Page 842: C.5.14 drive transfer percent
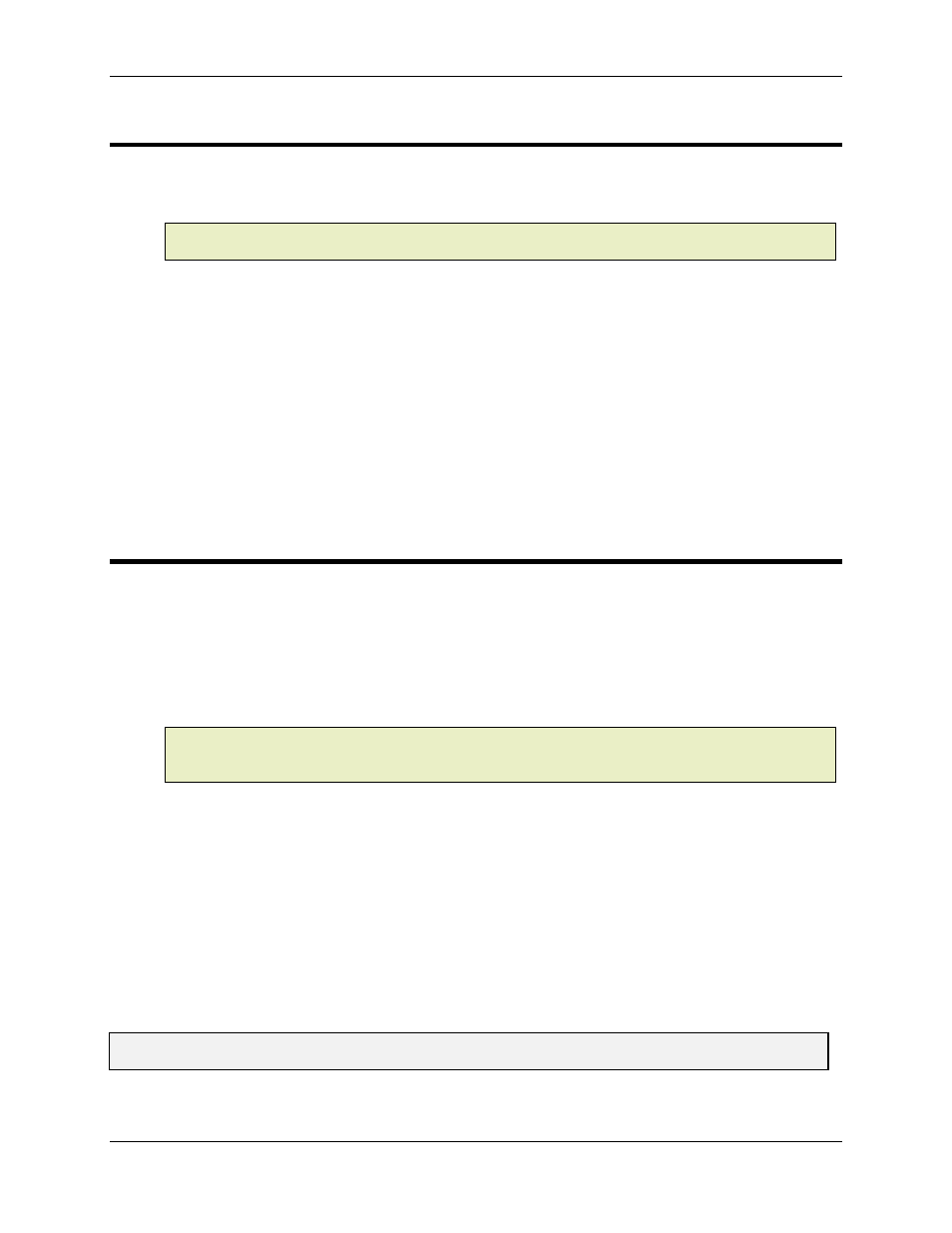
RMC100 and RMCWin User Manual
C-72
C.5.13 Filter Time Constant (Pressure/Force)
Default: 0 (disabled)
Range: 1 to 65,535 milliseconds, or 0 to disable
Note:
This parameter was introduced in RMC CPU firmware dated 20020429 or later. This
parameter is reserved in earlier firmware.
This parameter allows filtering the pressure/force feedback value. By default the filter is disabled.
If this parameter is set to a non-zero value, then the pressure/force feedback is filtered using an
Infinite Impulse Response (IIR) filter with a time constant set to this parameter's value in
milliseconds.
This feature should be left disabled in systems that need to react to quick changes in pressure, as
increasing this filter value will increase the phase delay in the system feedback, making the
system more likely to oscillate. Systems with slower acting pressures can benefit from applying
this filter.
To compute an initial value for your time constant value, recall that for a step jump in the
feedback value, an IIR filter will reach 63% in 1 time constant, and 99% in 5 time constants.
C.5.14 Drive Transfer Percent
Default: 0
Range: -500 to 500
This parameter affects the integral drive at the point when an axis transitions from position control
to pressure control. The drive at that point is multiplied by this parameter and divided by 100, and
this value is placed into the integral drive. The effect is that some controlled portion of the drive is
carried forward from position control into pressure control.
Note:
If this term is non-zero, then it is important that the Integral Gain also be non-zero.
Otherwise, the initial integral drive will never return to zero and the pressure may never reach
the requested pressure.
Why Bother?
There are two reasons for using this parameter to control pressure. First, a negative value can be
entered to apply extra braking power at the time pressure mode is entered. This is desired in
applications where momentum tends to cause the pressure to pass its command value even
though no additional drive is applied. By applying negative drive, the momentum can be taken
away.
Second, some users desire a bumpless transfer. A bumpless transfer is one in which the drive is
kept the same on the transition from position to pressure control and therefore the mass being
moved does not jerk on the transition. To achieve this affect, one would use a value in Drive
Transfer Percent near 100.
TIP:
In many applications the same effect of a bumpless transfer can be obtained with better results by
using appropriate Extend and Retract Feed Forward values.