3 encoder - angular drift monitoring, Encoder - angular drift monitoring, 6encoder/feedback system – Lenze 8400 TopLine User Manual
Page 371
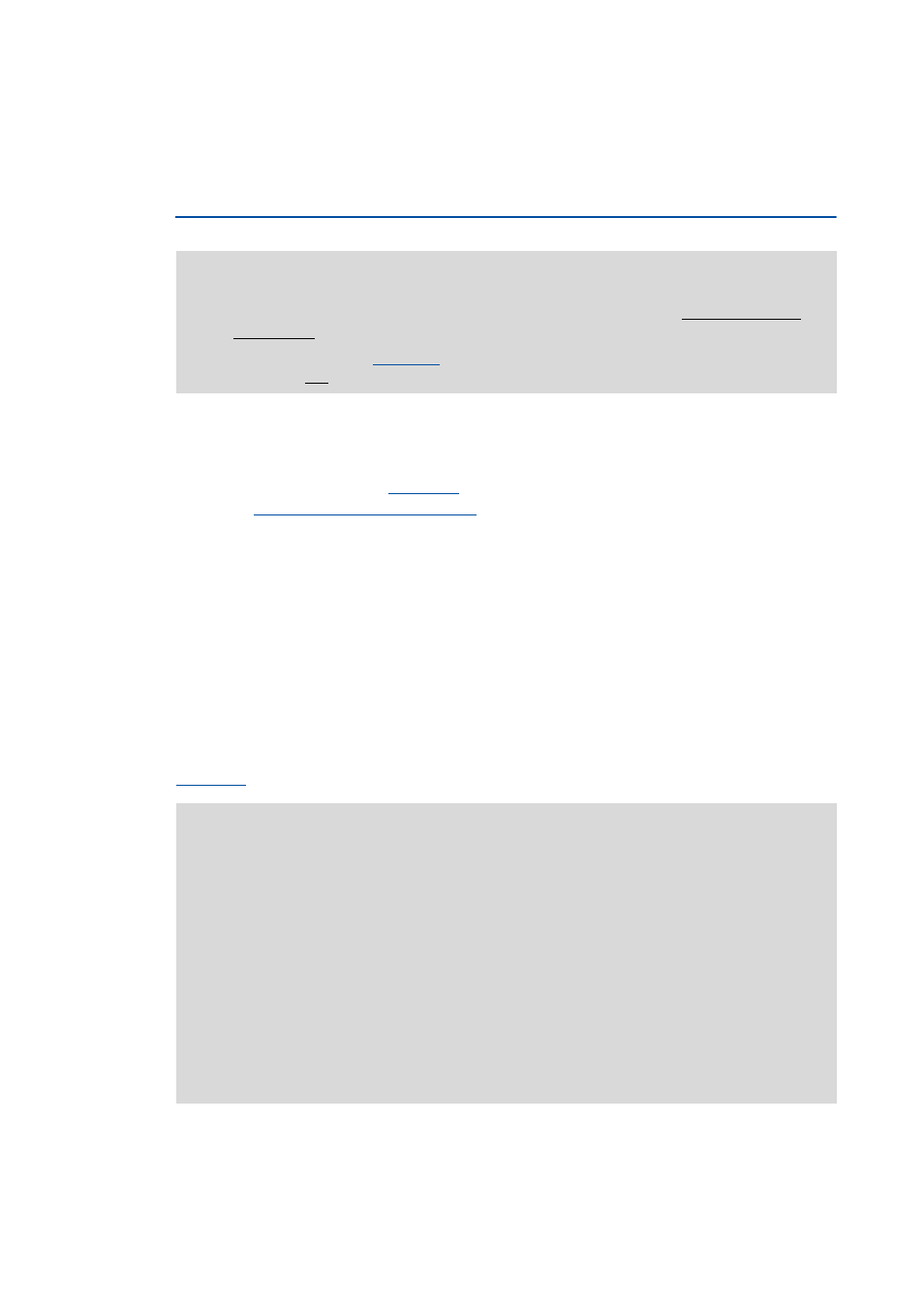
Lenze · 8400 TopLine · Reference manual · DMS 6.0 EN · 06/2014 · TD05/TD14
371
6
Encoder/feedback system
6.7
Monitoring
_ _ _ _ _ _ _ _ _ _ _ _ _ _ _ _ _ _ _ _ _ _ _ _ _ _ _ _ _ _ _ _ _ _ _ _ _ _ _ _ _ _ _ _ _ _ _ _ _ _ _ _ _ _ _ _ _ _ _ _ _ _ _ _
6.7.3
Encoder - angular drift monitoring
This function extension is available from version 12.00.00!
The encoder angular drift monitoring monitors a possible deviation of the real encoder angle from
the angle calculated by counting increments in the encoder evaluation.
• If a deviation higher than 45° (electrical) is recognised when monitoring is activated:
• The error response set in
• The "
Sd8: Encoder angular drift monit.
" error message is entered into the logbook.
• The "Reference known" status of the "Homing" basic drive function is reset (if this status was
set before)
Tip!
A deviation may occur, for instance, by incorrect parameter setting of the encoder
increments, by lines in the form of interferences caused by EMC or loss of lines caused by
EMC.
Functional principle
For an encoder without absolute information, the number of incoming encoder lines between two
zero pulses (one revolution) is monitored. This value must equal the encoder increments set in
.
Note!
The encoder angular drift monitoring is implemented for encoders without absolute
information.
In the Lenze setting (
= "0: No response"), the angular drift monitoring of the
encoder is not activated!
Note!
After mains switching, monitoring is only active after second incoming zero pulse since
the first line difference to be used can only be calculated with the second and first zero
pulse.
When the motor (and thus the encoder) is replaced, it is very likely that a angular drift
error occurs within the first revolution after acknowledging the encoder error since the
monitoring function cannot recognise that the encoder has been replaced.
Due to the type of monitoring, accuracy (distance of Z pulse to the detected position) can
only be detected while the machine is running. As a permanently pending error would
prevent the error cause to be removed, a detected error will be automatically reset by the
controller after a short time. In order that the motor does not continue to rotate in this
case, an engaging error response (e.g. "Fault" or "TroubleQSP") has to be set. If an error is
detected again, it is entered again into the logbook.