6encoder/feedback system – Lenze 8400 TopLine User Manual
Page 366
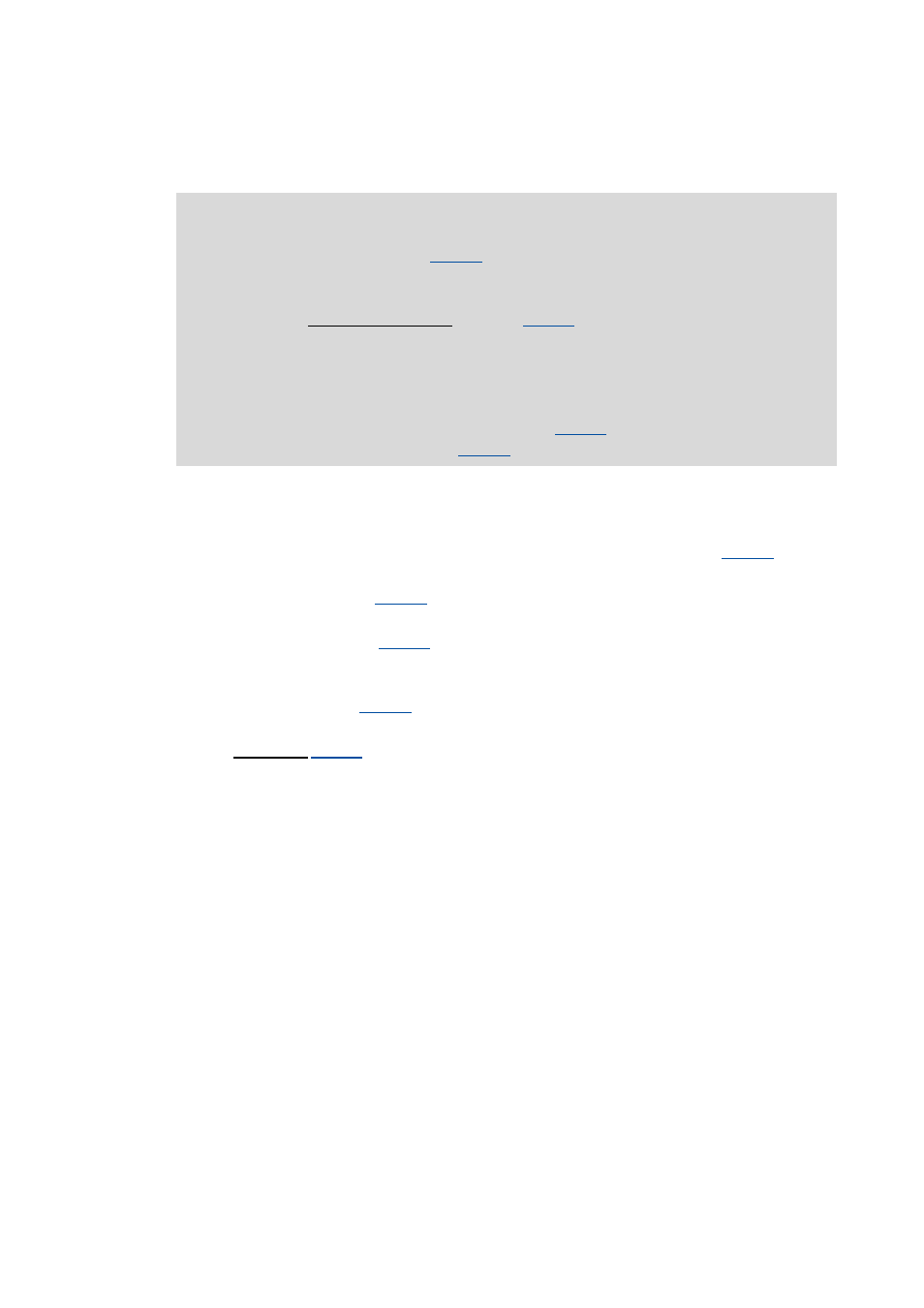
6
Encoder/feedback system
6.5
Pole position identification (PPI)
366
Lenze · 8400 TopLine · Reference manual · DMS 6.0 EN · 06/2014 · TD05/TD14
_ _ _ _ _ _ _ _ _ _ _ _ _ _ _ _ _ _ _ _ _ _ _ _ _ _ _ _ _ _ _ _ _ _ _ _ _ _ _ _ _ _ _ _ _ _ _ _ _ _ _ _ _ _ _ _ _ _ _ _ _ _ _ _
Optimising the pole position identification
How to optimise the pole position identification without motion:
1. For optimisation, enable the controller for various rotor displacement angles.
2. After every controller enable, check the optimisation degree displayed in
The pole position identification is set optimally if an optimisation degree in the range 70 ...
after every controller enable.
3. When the optimisation degree is > 130 %:
Reduce the setting in
step by step an execute controller enable for various rotor
displacement angles until an optimisation degree < 130 % is displayed.
4. When the optimisation degree is < 70 %:
Increase setting in
step by step and execute controller enable for various rotor
displacement angles until an optimisation degree > 70 % is displayed.
serves to increase or reduce the identified electrical rotor displacement
angle. This can prevent e.g. a reversing of the motor due to the accuracy of identification if
applications require it.
Stop!
In case of a too high setting in
, an impermissible motor current may occur during
pole position identification. In this case, the "Fault" error response occurs and the "Id5:
Pole position identification error" error message entered in the logbook.
In case of aconsiderably too high setting in
:
• The following current monitoring functions can be triggered:
• oC7: Motor overcurrent
• oC11: Clamp operation active
• oC1: Power section - short circuit
• The optimisation degree "0 %" is displayed in
• The time "0 ms" is displayed in