6encoder/feedback system – Lenze 8400 TopLine User Manual
Page 361
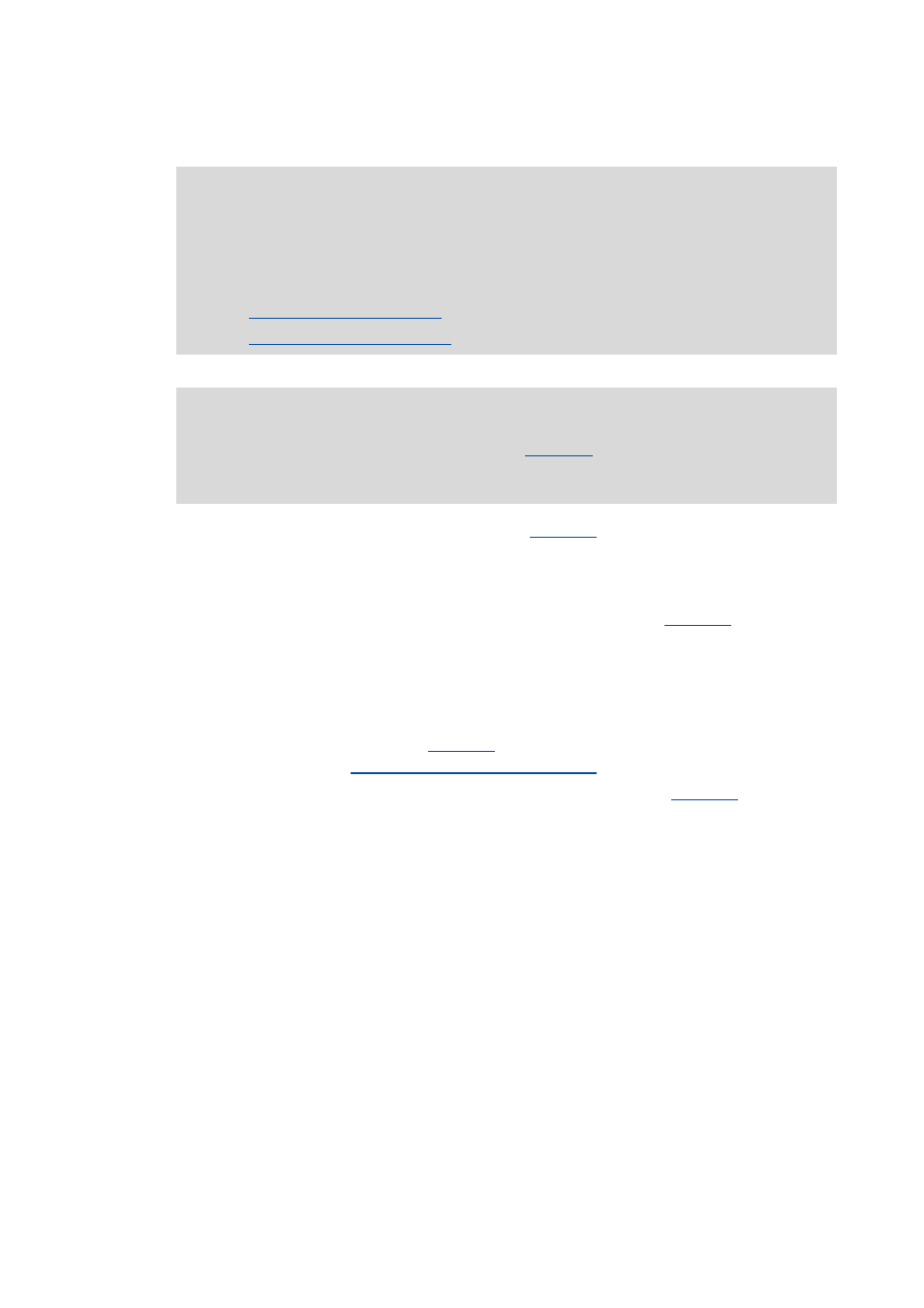
Lenze · 8400 TopLine · Reference manual · DMS 6.0 EN · 06/2014 · TD05/TD14
361
6
Encoder/feedback system
6.5
Pole position identification (PPI)
_ _ _ _ _ _ _ _ _ _ _ _ _ _ _ _ _ _ _ _ _ _ _ _ _ _ _ _ _ _ _ _ _ _ _ _ _ _ _ _ _ _ _ _ _ _ _ _ _ _ _ _ _ _ _ _ _ _ _ _ _ _ _ _
• The ramp time can be adjusted proportionally in
• For large machines and high mass inertia values, the ramp time usually has to be increased.
• For small machines, a reduction of the ramp time can speed up the pole position
identification process.
• In some situations it may be helpful to reverse the travel direction in
for the pole
position identification (e.g. for linear motor at the end stop).
• The "pole position identification 360°" procedure comprises a plausibility check. If the rotor
position determined via the encoder system does not correspond to the controlled output
position:
• the pole position identification procedure is aborted.
• the response parameterised in
(Lenze setting: "Fault") is activated.
• the error message "
Id5: Pole position identification error
" is entered into the logbook.
• The preset fault tolerance for the plausibility check can be changed in
Stop!
If there is no temperature monitoring in the motor and/or the I2xt motor monitoring
and the maximum current monitoring are not parameterised correctly, the motor may
be permanently damaged when the current amplitude is set too high (e.g. to the
maximum value)!
Note!
If the current amplitude is set to > 100 % in
, the device utilisation (Ixt)
monitoring and/or one of the motor monitoring functions may respond and cause the
abort of the pole position identification.