6encoder/feedback system – Lenze 8400 TopLine User Manual
Page 362
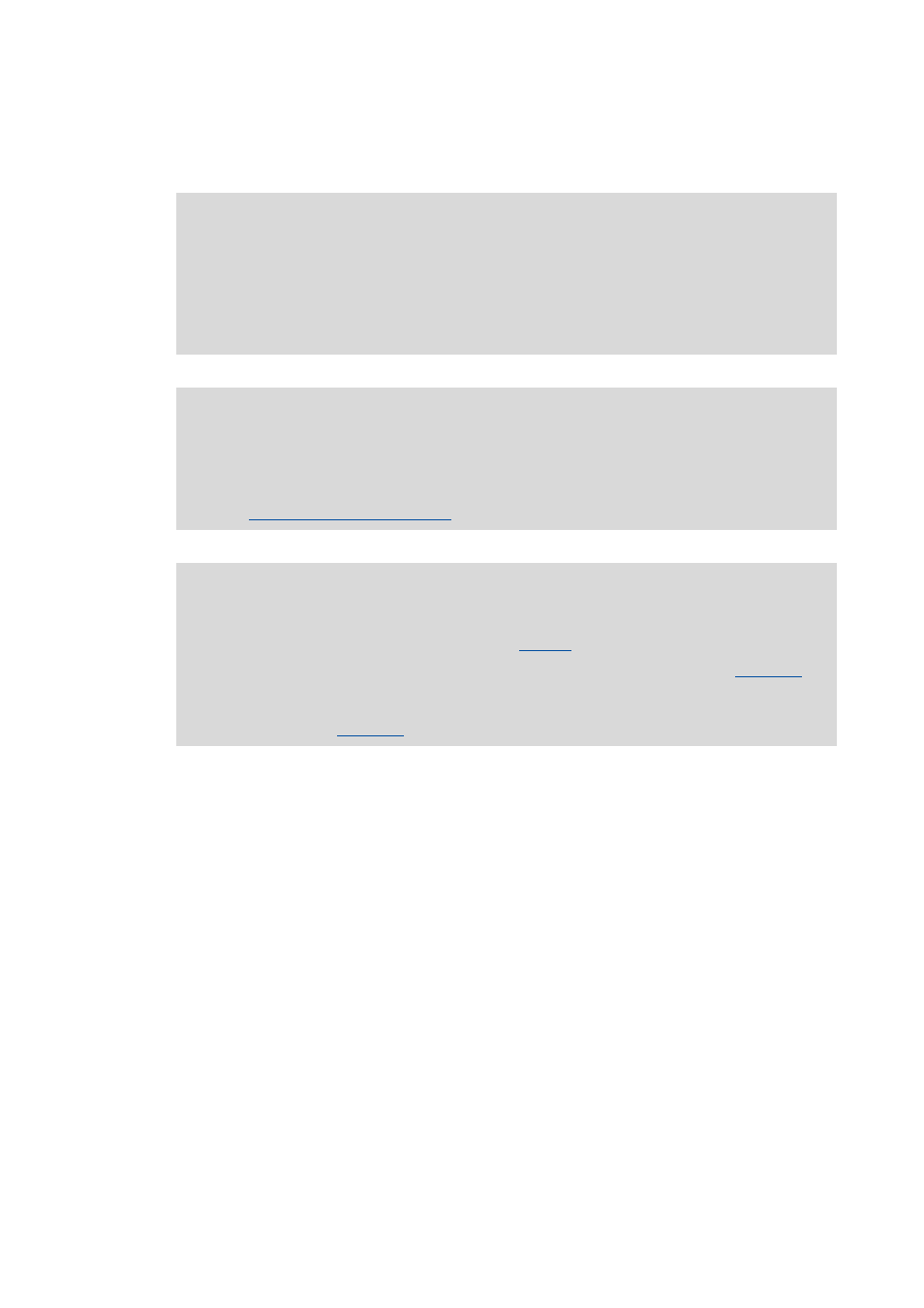
6
Encoder/feedback system
6.5
Pole position identification (PPI)
362
Lenze · 8400 TopLine · Reference manual · DMS 6.0 EN · 06/2014 · TD05/TD14
_ _ _ _ _ _ _ _ _ _ _ _ _ _ _ _ _ _ _ _ _ _ _ _ _ _ _ _ _ _ _ _ _ _ _ _ _ _ _ _ _ _ _ _ _ _ _ _ _ _ _ _ _ _ _ _ _ _ _ _ _ _ _ _
Execute pole position identification 360°
Preconditions for the execution
• A synchronous motor has been selected.
• No other identification is active.
• No error has occurred.
Danger!
The machine must not be braked or blocked during the pole position identification! For this
reason, the pole position identification is not permitted for hanging loads!
During the pole position identification the rotor aligns itself. The motor shaft moves by
max. one electrical revolution which causes the corresponding movement of the connected
mechanical components!
Stop!
Check the correct parameterisation of the max. motor current monitoring before
carrying out the pole position identification to prevent the motor from being
permanently damaged.
Note!
By means of controller inhibit, the procedure started can be cancelled anytime, if
required, without carrying out a change in
If the pole position identification is aborted, the response parameterised in
is
activated (Lenze setting: "Fault").
• If this behaviour is not wanted, deactivate the monitoring by selecting "0: No
response" in