5motor control (mctrl) – Lenze 8400 TopLine User Manual
Page 246
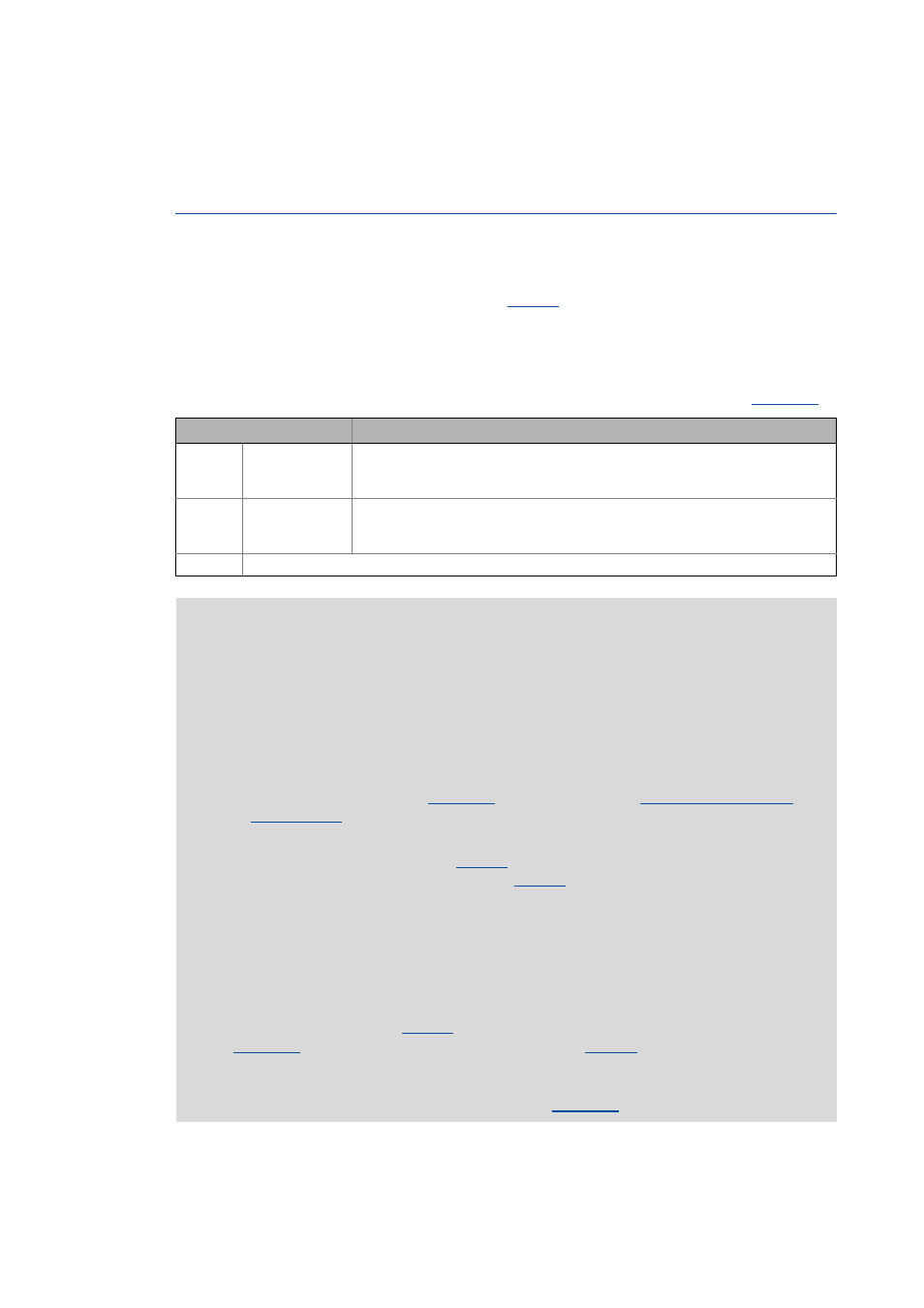
5
Motor control (MCTRL)
5.9
Servo control (SC)
246
Lenze · 8400 TopLine · Reference manual · DMS 6.0 EN · 06/2014 · TD05/TD14
_ _ _ _ _ _ _ _ _ _ _ _ _ _ _ _ _ _ _ _ _ _ _ _ _ _ _ _ _ _ _ _ _ _ _ _ _ _ _ _ _ _ _ _ _ _ _ _ _ _ _ _ _ _ _ _ _ _ _ _ _ _ _ _
5.9.4.6
Slip calculation from motor equivalent circuit diagram data
This function extension is available from version 02.00.00!
In order to achieve a better speed stability and torque accuracy, the slip calculation can be either
derived from the motor nameplate data (e.g. rated motor speed) or the motor equivalent circuit
diagram data (stator resistance, rotor resistance etc.).
In case of servo control for asynchronous motors (
= "2"), the slip calculation is always made
•
up to and including version 01.xx.xx
from the motor nameplate data.
•
from version 02.00.00 onwards
in the Lenze setting from the motor equivalent circuit diagram
data in order to obtain a higher torque accuracy.
The data to be used for servo control (for asynchronous motors) is selected via bit 1 in
:
Setting
Info
Bit 0 SLVC
In case of sensorless vector control:
• "0" ≡ Slip calculation from motor nameplate data (Lenze setting)
• "1" ≡ Slip calculation from motor equivalent circuit diagram data
Bit 1 SC_ASM
In case of servo control for asynchronous motors:
• "0" ≡ Slip calculation from motor nameplate data
• "1" ≡ Slip calculation from motor equivalent circuit diagram data (Lenze setting)
Bit 2 ... 7 Reserved
Note!
In order that the slip can be calculated from the motor equivalent circuit diagram data,
the equivalent circuit data (stator resistance, rotor resistance etc.) must be known as
exactly as possible.
• Selecting a motor in the »Engineer« motor catalogue loads the exact motor
equivalent circuit diagram data.
• When the motor nameplate data is entered manually and the motor equivalent
circuit diagram data is then detected via the motor parameter identification, the
"extended identification" (
= 2) must be used.
In case of servo control for asynchronous motors, the slip calculation can also be made
from the motor nameplate data (
/Bit 1 = "0"). In this case, the slip is too high by
a factor of 1.35 as the rated motor speed (
) is assumed for a cold machine. This
has the following consequences:
• The higher slip provides a better behaviour for the field weakening range.
• In the motor setting range, a considerably too high torque is detected (torque
accuracy is worse).
• The achieved maximum torque in the motor setting range is smaller.
From version 15.00.00
, the excessive slip with the activated "slip calculation from motor
nameplate data" option (
/bit 1 = "0") can be corrected by setting bit 7 to "1" in
. With this setting, the rated motor speed (
) for a warm machine is
assumed.
• By selecting the motor in the »Engineer« motor catalogue or executing the motor
parameter identification, bit 7 is set to "1" in