19 function library – Lenze 8400 TopLine User Manual
Page 1508
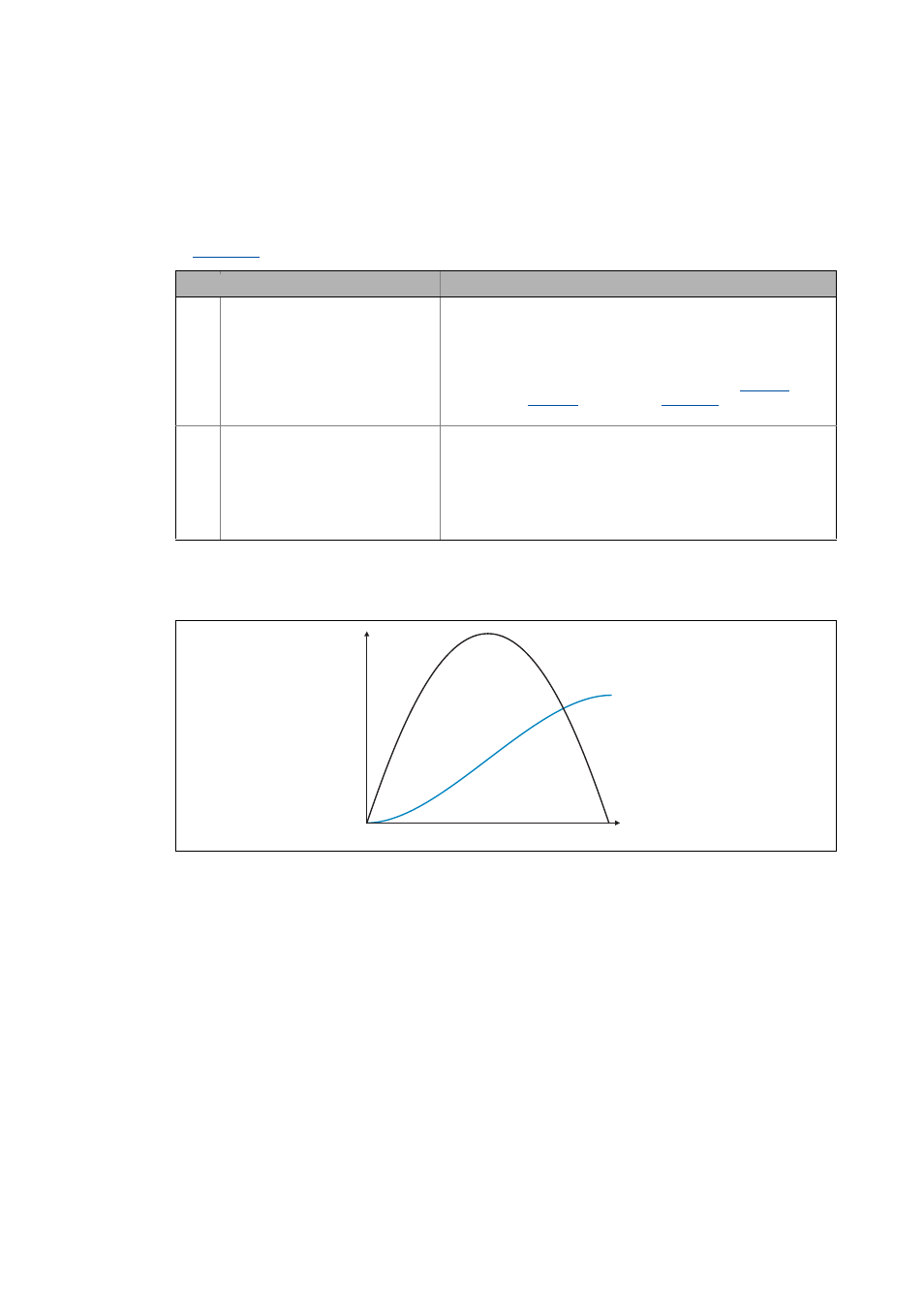
19
Function library
19.1
Function blocks
1508
Lenze · 8400 TopLine · Reference manual · DMS 6.0 EN · 06/2014 · TD05/TD14
_ _ _ _ _ _ _ _ _ _ _ _ _ _ _ _ _ _ _ _ _ _ _ _ _ _ _ _ _ _ _ _ _ _ _ _ _ _ _ _ _ _ _ _ _ _ _ _ _ _ _ _ _ _ _ _ _ _ _ _ _ _ _ _
Compensation process
At the input of the second set or actual touch probe pulse, the difference between master and slave
position is detected which is then provided via the nSpeedSetOut_v speed output and equivalently
as position at .
In
, the following bit coded settings can be made for the compensation procedure:
The following illustration shows a compensating process after the marks have been detected. The
speed is added here as a parabola to the line speed. (The scaling in this diagram does not correspond
to reality)
[19-39] Example: Compensation process
Setting
Info
Bit 1
Angle correction with polynomial
If this bit is set (Lenze setting),the compensating movement is
rounded by polynomial.
• The angle error to be compensated is limited to ±1073741823
increments due to the system. This applies in general when the
L_DFSET_1 carries out the compensation.
• The maximum compensating speed can be set in
. When
if activated in
, the angle error is
measured and output to dnPosDiffOut_p.
Bit 2
External angle correction
From version 13.00.00
If this bit is set, the FB L_DFSET_1 does not compensate any angle
errors.
• Every time the angle errors have been measured, the angular
difference is output to dnPosDiffOut_p.
• In addition, a FALSE/TRUE edge is output to bAck. This signal
serves to trigger an external profile generator which
compensates the angular offset via a speed profile additionally.
nSpeedSetOut_v
dnPosDiffOut_p
t
v