So observe the, Notes for using an ssi laser position encoder, 6encoder/feedback system – Lenze 8400 TopLine User Manual
Page 341
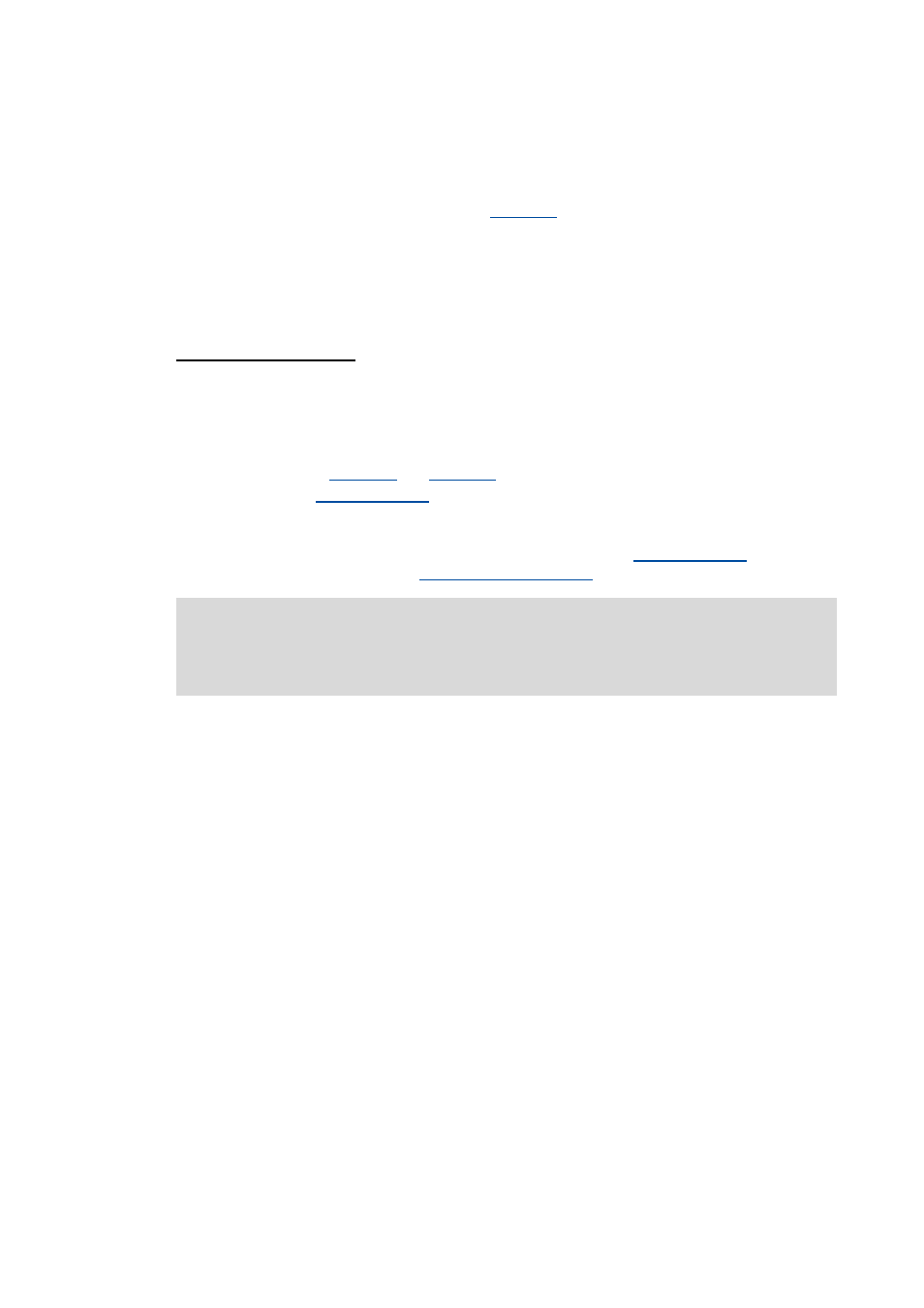
Lenze · 8400 TopLine · Reference manual · DMS 6.0 EN · 06/2014 · TD05/TD14
341
6
Encoder/feedback system
6.3
Multi-Encoder (X8)
_ _ _ _ _ _ _ _ _ _ _ _ _ _ _ _ _ _ _ _ _ _ _ _ _ _ _ _ _ _ _ _ _ _ _ _ _ _ _ _ _ _ _ _ _ _ _ _ _ _ _ _ _ _ _ _ _ _ _ _ _ _ _ _
6.3.3.2
Important notes for using an SSI laser position encoder
If you are using an SSI laser position encoder at X8 and, deviating from the Lenze setting, you have
activated the position control for quick stop (
- bit 0 and/or bit 1 set), please note the
following:
If the laser beam is interrupted, due to the "TroubleQuickStop" following error standard response,
the drive may move unexpectedly.
• A drive that had already reached the position-controlled standstill can execute a movement.
• A drive that is ramping down can continue running.
Possible countermeasures:
• Do not use the controller with the above-described parameter setting.
• By implementing suitable other measures, ensure that, in terms of safety aspects, the response
described is acceptable for the specific application case.
• Monitor the valid position:
• Use parameters
to define a value range for valid positions.
• Configure the
.bFail output so that controller inhibit is set when the output
at the drive is active. Take other requirements relating to the application into consideration
(e.g. application of brake).
• Resulting drive behaviour: If the value range set is exited, the
.bFail output
activates controller inhibit.
Note!
The response of the drive to interruptions of the laser beam is always part of the error
scenarios to be checked during commissioning.