5 pole position identification (ppi), Pole position identification (ppi), Pole position identification – Lenze 8400 TopLine User Manual
Page 358: Pole position identification (ppi) ( 358), Pole position identification (pli), Carry out, 6encoder/feedback system
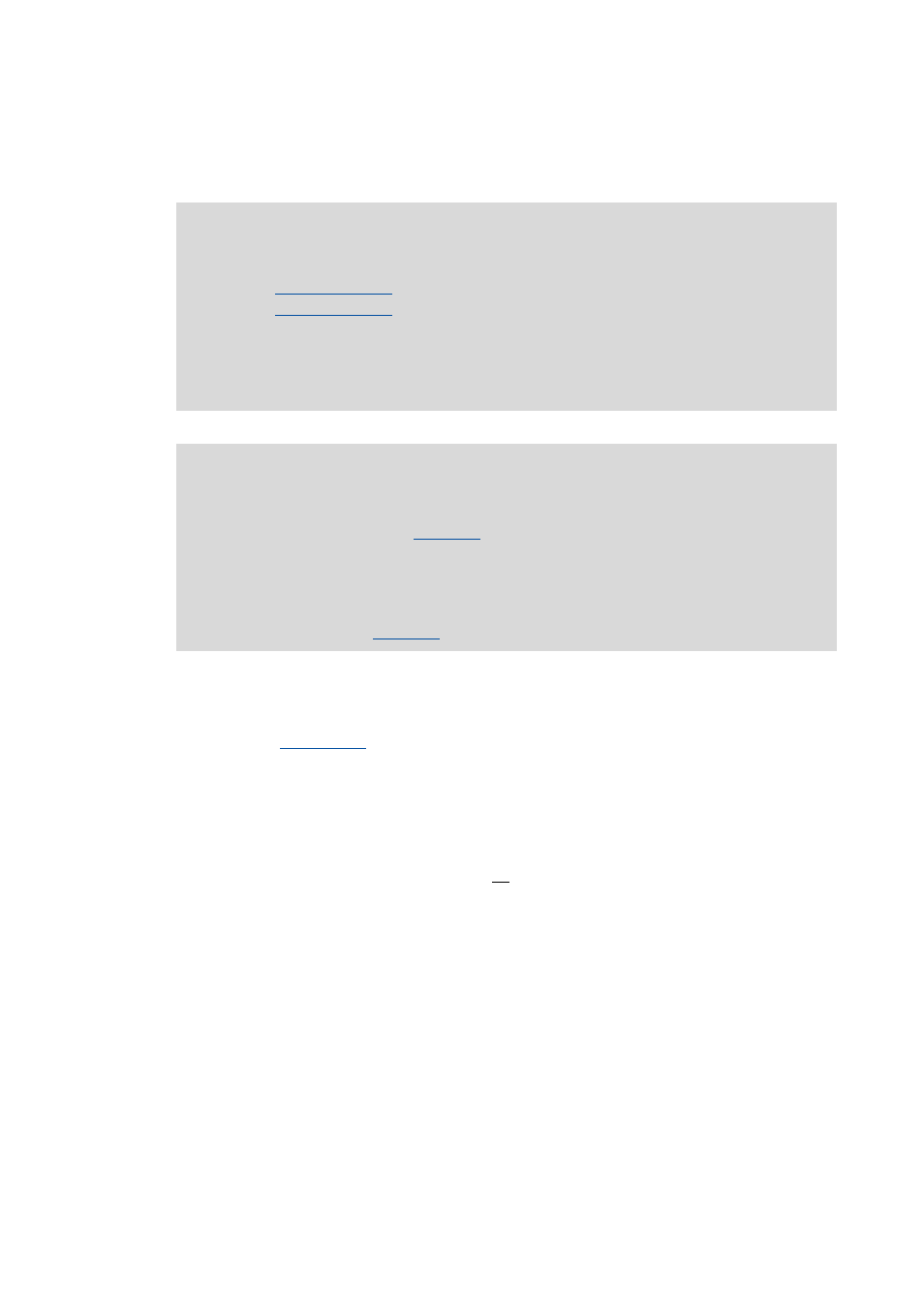
6
Encoder/feedback system
6.5
Pole position identification (PPI)
358
Lenze · 8400 TopLine · Reference manual · DMS 6.0 EN · 06/2014 · TD05/TD14
_ _ _ _ _ _ _ _ _ _ _ _ _ _ _ _ _ _ _ _ _ _ _ _ _ _ _ _ _ _ _ _ _ _ _ _ _ _ _ _ _ _ _ _ _ _ _ _ _ _ _ _ _ _ _ _ _ _ _ _ _ _ _ _
6.5
Pole position identification (PPI)
For the control of permanent-magnet synchronous machines, the pole position – the angle between
the motor phase U and the field axis of the rotor – must be known.
• For Lenze motors with absolute value encoder or resolver, the pole position is already set
.
• When incremental encoders (TTL or sin/cos encoders) are used, a pole position identification
(PPI) is always required after mains switching, even with Lenze motors.
• The controller can also evaluate multi-pole-pair resolvers.
• When the number of motor pole pairs is an integer multiple of the number of pole pairs of
the resolver, a pole position identification must only be executed once.
• When the number of motor pole pairs is no integer multiple of the number of pole pairs of
the resolver, a pole position identification must be executed after every mains switching.
Note!
Only required:
with synchronous motor of a third-party manufacturer.
with synchronous motor and use of incremental encoders (TTL
or sin/cos encoders as well as multi-pole pair resolvers).
• After changes of the motor feedback system, e.g. encoder exchange.
For the sensorless control of synchronous motors (SLPSM), a pole position identification
is not required.
Note!
Acceptance of the resolver pole position from a Servo Drive 9400
The resolver pole position (
) cannot be simply accepted from a Servo Drive
9400 if the pole position (C58/1) considerably differs from -90 ° in the Servo Drive 9400.
• We always recommend a pole position identification (PLI).
• As an alternative, the following conversion has to be carried out for a transfer of the
resolver pole position from a Servo Drive 9400 to the 8400 TopLine:
Pole position
8400
) = - (pole position
9400_C58/1
+ 180 °)