5motor control (mctrl) – Lenze 8400 TopLine User Manual
Page 266
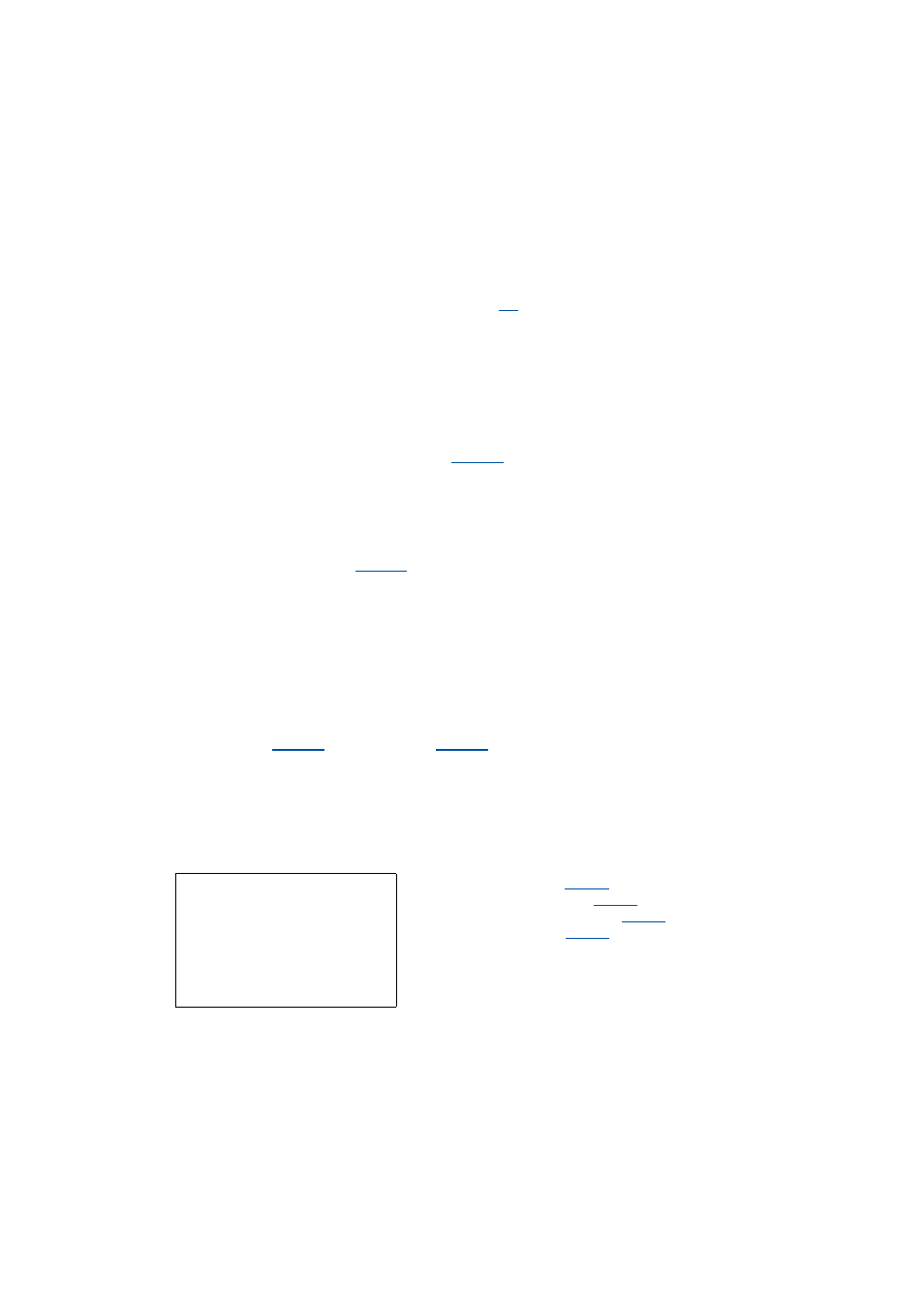
5
Motor control (MCTRL)
5.10
Parameterisable additional functions
266
Lenze · 8400 TopLine · Reference manual · DMS 6.0 EN · 06/2014 · TD05/TD14
_ _ _ _ _ _ _ _ _ _ _ _ _ _ _ _ _ _ _ _ _ _ _ _ _ _ _ _ _ _ _ _ _ _ _ _ _ _ _ _ _ _ _ _ _ _ _ _ _ _ _ _ _ _ _ _ _ _ _ _ _ _ _ _
We recommend setting a flying restart current of 10 % ... 25 % of the rated motor current.
• During a flying restart process, a current is injected into the motor to identify the speed.
• Reducing the current causes a reduction of the motor torque during the flying restart
process. A short-time starting action or reversing of the motor is prevented with low
flying restart currents.
• An increase of the current improves the robustness of the flying restart function.
• At too high mass inertias and high speeds at the same time, the flying restart circuit may
cause an overvoltage in the DC bus ("
") if no brake resistor is connected. In this case,
reduce the flying restart current.
Tip!
Use of motors with higher rated frequencies
For trouble-free operation, we recommend to manually enter a starting frequency of 20 %
of the rated motor frequency in
as well as to accelerate the flying restart process
(see above) and to use a lower flying restart current (10 % of the rated motor current) if
motors with higher rated frequencies are used.
Optimisation of the flying restart time
The duration of the flying restart process can be influenced via the setting of the
integration time (
). A reduction of the integration time causes the flying restart
function to accelerate and thus a reduced flying restart time.
• We recommend not to change the Lenze setting of the integration time.
• When special motor are used (e.g. multi-pole motors or ASM servo motors), a reduced
integration time may improve the flying restart behaviour.
Optimising the current controller if the behaviour is unstable
During the execution of flying restart function, peak currents/torques are avoided by
controlling the current amplitude.
Gain (
) of the current controller can be adapted to improve
the jerk-free/torque-free connection of the inverter to the supply of the rotating motor.
• We recommend not to change the Lenze setting of the current controller.
• If the behaviour of the current controller is unstable, gain and reset time can be
calculated as per the following formulae:
[5-22] Formulae for the calculation of the gain and reset time of the current controller
V
p
= Current controller gain (
T
i
= Current controller reset time (
)
L
ss
= Motor stator leakage inductance (
)
R
s
= Motor stator resistance (
)
T
E
= Equivalent time constant (= 500 μs)
V
p
L
ss
H
[ ]
T
E
s
[ ]
----------------
=
T
i
L
ss
H
[ ]
R
s
Ω
[ ]
----------------
=