2 pole position identification without motion, Pole position identification without motion, Can be avoided – Lenze 8400 TopLine User Manual
Page 364: 6encoder/feedback system
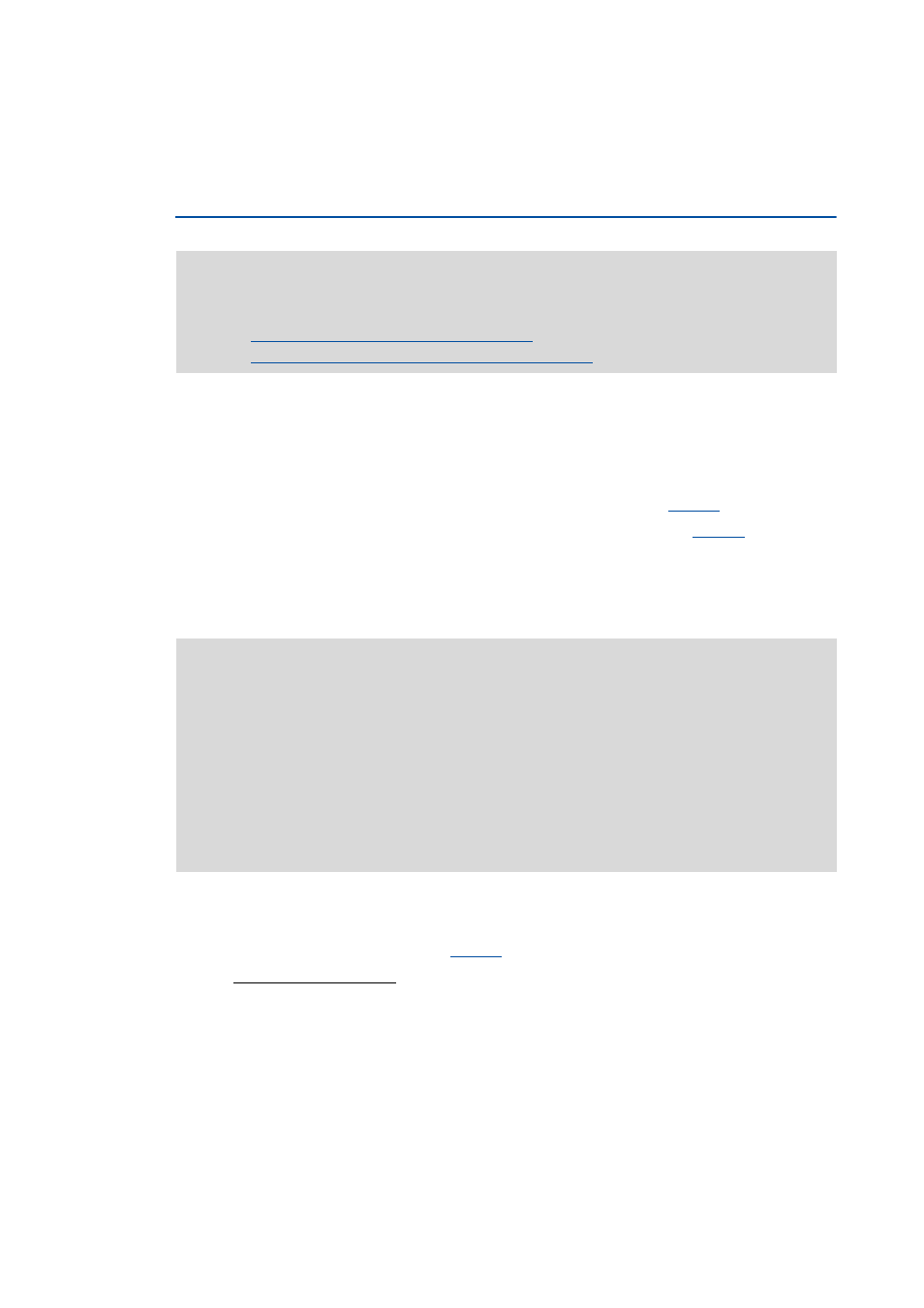
6
Encoder/feedback system
6.5
Pole position identification (PPI)
364
Lenze · 8400 TopLine · Reference manual · DMS 6.0 EN · 06/2014 · TD05/TD14
_ _ _ _ _ _ _ _ _ _ _ _ _ _ _ _ _ _ _ _ _ _ _ _ _ _ _ _ _ _ _ _ _ _ _ _ _ _ _ _ _ _ _ _ _ _ _ _ _ _ _ _ _ _ _ _ _ _ _ _ _ _ _ _
6.5.2
Pole position identification without motion
This function extension is available from version 02.00.00!
From version 02.00.00, a pole position identification without motion is also possible in case of servo
control and sensorless control.
• For sensorless control of synchronous motors (SLPSM), this function is already activated in the
Lenze setting, i.e. with every controller enable the rotor displacement angle is identified and
thus jerks in the machine after controller enable can be avoided.
• In order to achieve the same behaviour as before, set bit 0 to "0" in
.
• For servo control (SC), this function can be activated for various events in
bits 1 ... 3:
• Bit 1: Pole position identification after mains connection
• Bit 2: Pole position identification after controller enable
• Bit 3: Pole position identification after error acknowledgement
Tip!
In case of servo control (SC), it is generally sufficient to activate this function only once after
mains connection of the device (
: Bit 1 = "1").
Typical application case: A speed sensor with an unknown pole position is used (e.g.
encoder). The pole position identification 360°, however, cannot be used since, e.g. the
motor is locked, the application does not permit it or the identification takes too long.
Note!
Function only possible with:
Servo control (SC) for synchronous motors
•
Sensorless control for synchronous motors (SLPSM)
Note!
• The "Pole position identification without motion" cannot completely replace the "pole
position identification 360°"!
• The electrical rotor displacement angle can only be electrically identified with an
error of up to 10°. This inaccuracy can cause a worse torque accuracy and a worse
energy efficiency.
• The identification takes motor-dependent 1 ... 15 ms. The setpoint enabling of the
device is reduced by this time.
• In the Lenze setting, the function is preset so that in most of the cases no further
settings have to be made.