2 monitoring for counter overflow, 5function blocks – Lenze E94A User Manual
Page 378
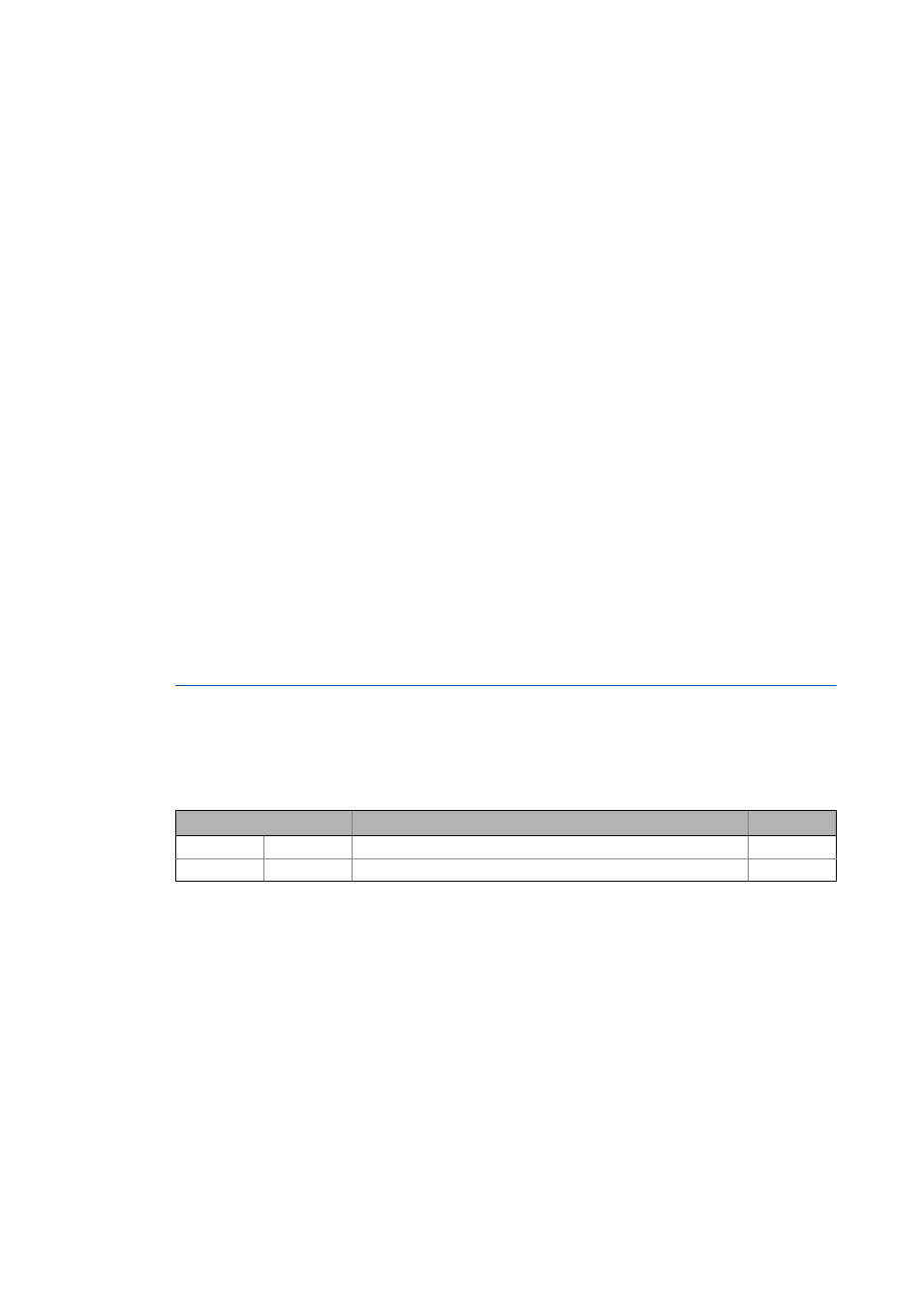
5
Function blocks
5.99
L_LdVirtualMasterP - virtual master for synchronism
378
Lenze · 9400 function library · Reference manual · DMS 6.7 EN · 08/2014 · TD05
_ _ _ _ _ _ _ _ _ _ _ _ _ _ _ _ _ _ _ _ _ _ _ _ _ _ _ _ _ _ _ _ _ _ _ _ _ _ _ _ _ _ _ _ _ _ _ _ _ _ _ _ _ _ _ _ _ _ _ _ _ _ _ _
Profile generator/stopping at stop position:
• The process can be executed via several machine cycles (example: printing machines). The
setting of the operating time is decisive.
Load starting position:
• The starting position set in C05012 is accepted by setting bLoadStartPos to TRUE.
• For this, the enable input bEnable must be set to TRUE.
Stop master shaft
• The master shaft is braked to standstill within the operating time set in C05015/3 setting
bStopInstant to TRUE.
• For this, the enable input bEnable must be set to TRUE.
• This function has the highest priority.
Change over to second master speed
• By setting bEnable2ndSpeedSet to TRUE, the master speed 1 (C05013/1) is changed to master
speed 2 (C05013/2).
• Ramp functions are active.
5.99.2
Monitoring for counter overflow
This function extension will be available from library V2.02!
If the machine parameters transferred to the FB via the AxisData input are changed afterwards (e.g.
the gearbox factors), this may cause a counter overflow when the speed and position values defined
via parameters are converted from the real unit to the internal unit.
The FB causes a corresponding error message in case of an internal counter overflow due to a
changed measuring system:
Error number
Error message in the logbook
Response
61669515
0x3AD008B
L_LdVirtualMasterP:int.speed overflow (LS_DriveInterface)
Error
61669387
0x3AD000B
L_LdVirtualMasterP:int.speed overflow (L_SdSetAxisData)
Error