Control, C 93), 9400 highline | parameter setting & configuration – Lenze E94AxHE Servo Drives 9400 HighLine (Firmware 01-37) User Manual
Page 93
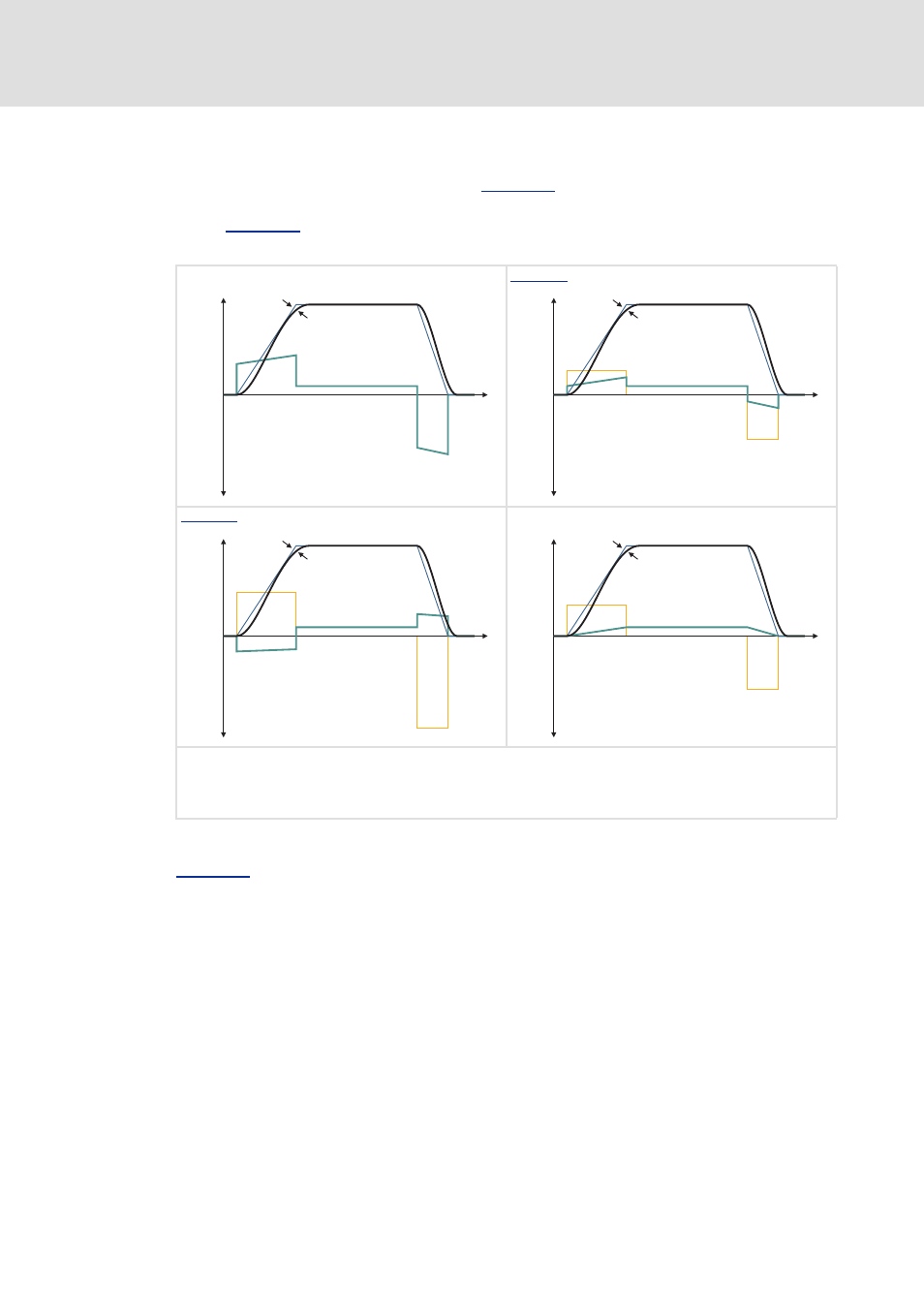
L
Firmware 1.37 - 09/2006
93
9400 HighLine | Parameter setting & configuration
Motor interface
Extended commissioning | Optimise the response to setpoint changes by means of the torque
5.2.4
Optimise the response to setpoint changes by means of the torque feedforward control
Setting the load moment of inertia under
does not always provide the optimum
torque feedforward control. Depending on the application, an adaptation of the setting
under
may be necessary to optimise the response to position/speed control
setpoint changes.
[5-8]
Typical signal characteristics for different settings of the load moment of inertia
can be used to compensate for effects in addition to the moment of inertia
which are detected by the speed controller in the closed speed control loop (e.g. friction
torque).
Below you will find a description of a procedure for optimising the feedforward control
behaviour starting from the system's moment of inertia.
Without feedforward control:
set too low:
set too high:
Optimum feedforward control:
n
Speed setpoint (Speed.dnSpeedSetpoint signal)
o
Actual speed value (Speed.dnActualMotorSpeed signal)
p
Speed controller output (Torque.dnOutputSpeedCtrl signal)
q
Torque feedforward control (Torque.dnTotalTorqueAdd signal)
n, M
t
t
n, M
t
n, M
t
n, M