11 basic drive functions – Lenze 9400 User Manual
Page 574
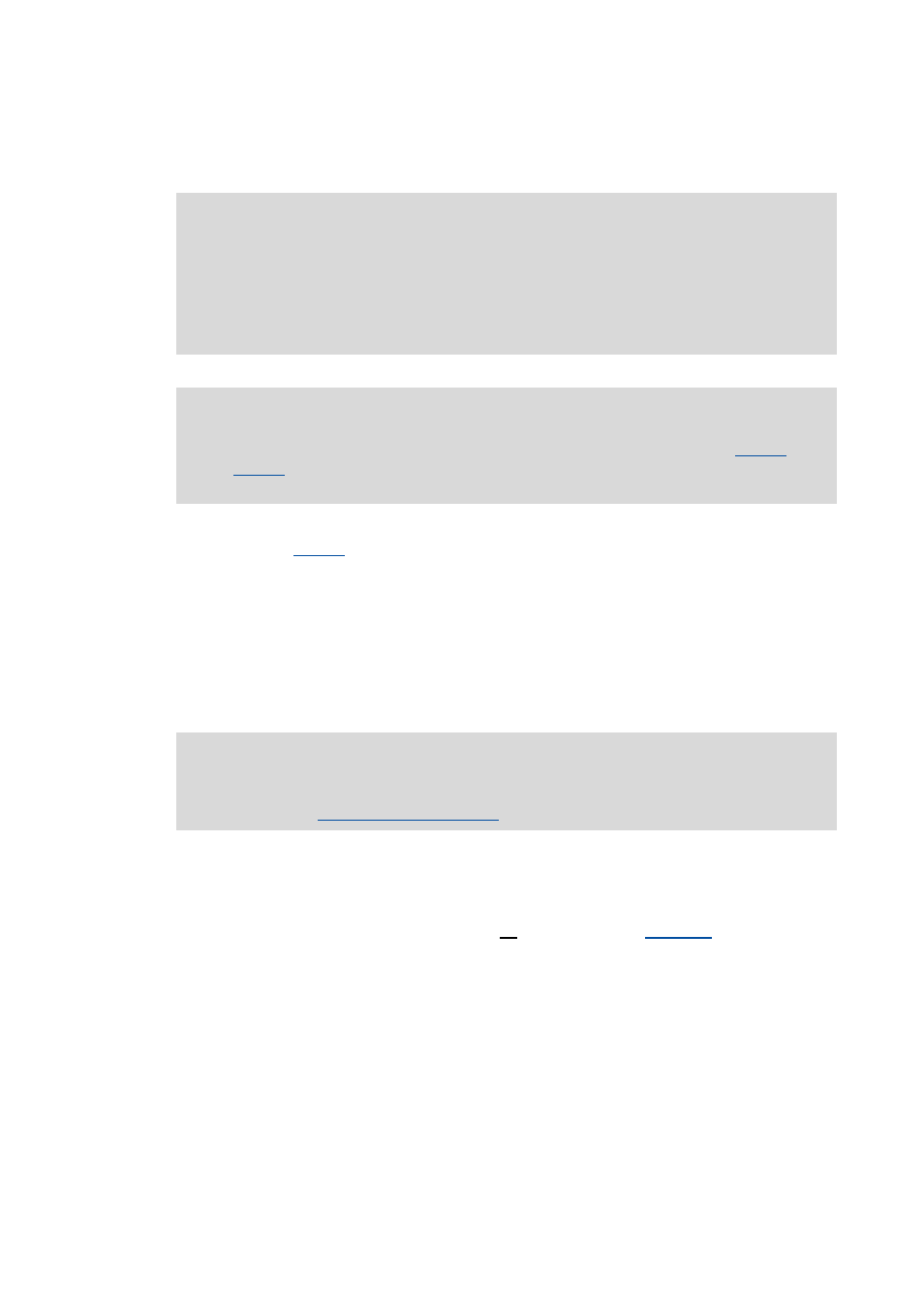
11
Basic drive functions
11.14
Pole position identification
574
Lenze · Servo-Inverter 9400 HighLine · Reference manual · DMS 10.0 EN · 11/2013 · TD05/06
_ _ _ _ _ _ _ _ _ _ _ _ _ _ _ _ _ _ _ _ _ _ _ _ _ _ _ _ _ _ _ _ _ _ _ _ _ _ _ _ _ _ _ _ _ _ _ _ _ _ _ _ _ _ _ _ _ _ _ _ _ _ _ _
Start pole position identification
By setting the PPI_bStart control input to TRUE, the pole position identification is started in the
mode selected in
.
• The procedure starts with controller enable, if
• a synchronous machine is selected,
• no other identification is active,
• no error has occurred, and
• no test mode is activated.
• If one of the above conditions is not met, the procedure is cancelled and the corresponding
device command status is indicated via PPI_dnState.
Deactivation
When the PPI_bEnable enable input is reset to FALSE, an active pole position identification is
stopped.
• If the pole position identification is aborted, no change is made in
• The PPI_bEnabled status output is reset to FALSE and a change-over from the active "Pole
position identification active" function state back to the basic "Controller not ready" state is
carried out.
Danger!
The machine must not be braked or blocked during the pole position identification! For this
reason, the pole position identification is not permitted for hanging loads!
During the pole position identification the rotor aligns itself. The motor shaft moves by
max. one electrical revolution which causes the corresponding movement of the connected
mechanical components!
Stop!
Check the correct parameterisation of the max. motor current monitoring (
) before carrying out the pole position identification to prevent the motor from
being permanently damaged.
Note!
Detailed information on the identification of pole position can be found in the
subchapter "