5motor interface – Lenze 9400 User Manual
Page 220
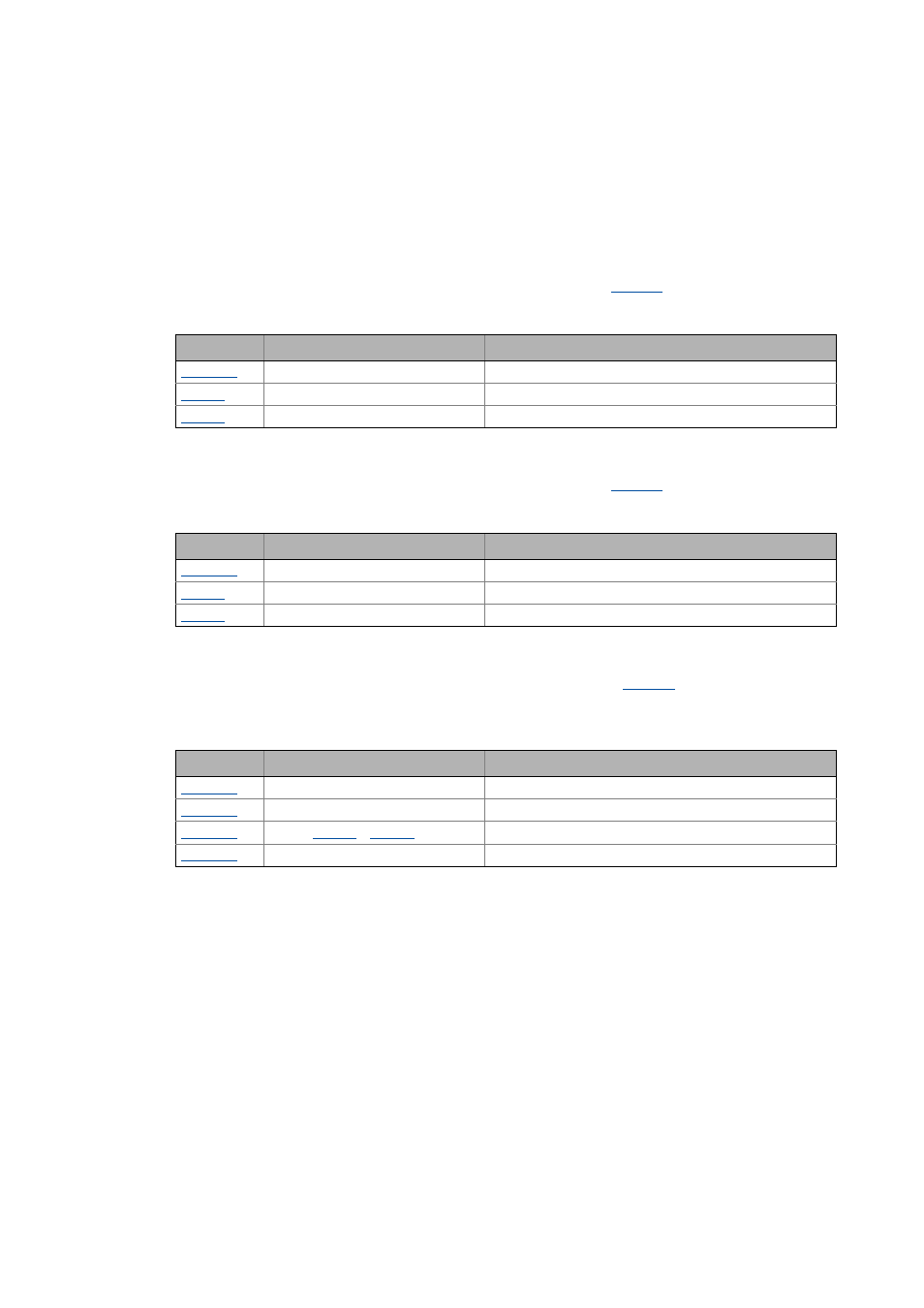
5
Motor interface
5.9
Monitoring
220
Lenze · Servo-Inverter 9400 HighLine · Reference manual · DMS 10.0 EN · 11/2013 · TD05/06
_ _ _ _ _ _ _ _ _ _ _ _ _ _ _ _ _ _ _ _ _ _ _ _ _ _ _ _ _ _ _ _ _ _ _ _ _ _ _ _ _ _ _ _ _ _ _ _ _ _ _ _ _ _ _ _ _ _ _ _ _ _ _ _
5.9.2.3
UL 508-compliant I²xt motor temperature monitoring
The following test steps 1 ... 4 are part of the UL 508C-compliant device acceptance.
They have to be executed successfully during the I²xt motor monitoring.
Test step 1
• Motor overload: 6 x I
rated,mot
(I
rated,mot
: Rated motor current (
))
• Trigger time: Max. 20 s after the overload has occurred
Test step 2
• Motor overload: 2 x I
rated,mot
(I
rated,mot
: Rated motor current (
))
• Trigger time: Max. 480 s after the overload has occurred
Test step 3
• Motor overload: 1,1 x I
rated,mot
(I
rated,mot
: Rated motor current (
• In case of a motor field frequency of 10 Hz, the I²xt motor monitoring has to be tripped faster
than with a motor field frequency of 20 Hz.
Code
Setting
Info
11.8 min
Thermal time constant - laminated core/housing
0 %
Percentage of the winding in the final temperature
100 %
Switch-off threshold of motor overload protection (I²xt)
Code
Setting
Info
27.8 min
Thermal time constant - laminated core/housing
0 %
Percentage of the winding in the final temperature
100 %
Switch-off threshold of motor overload protection (I²xt)
Code
Setting
Info
0 %
Speed = 0 (standstill)
< 100 %
Permissible motor torque at standstill
20 Hz /
Speed n
2
from which on the torque must be reduced
100 %
Permissible motor torque at speed n
2
(torque reduction)