5motor interface – Lenze 9400 User Manual
Page 155
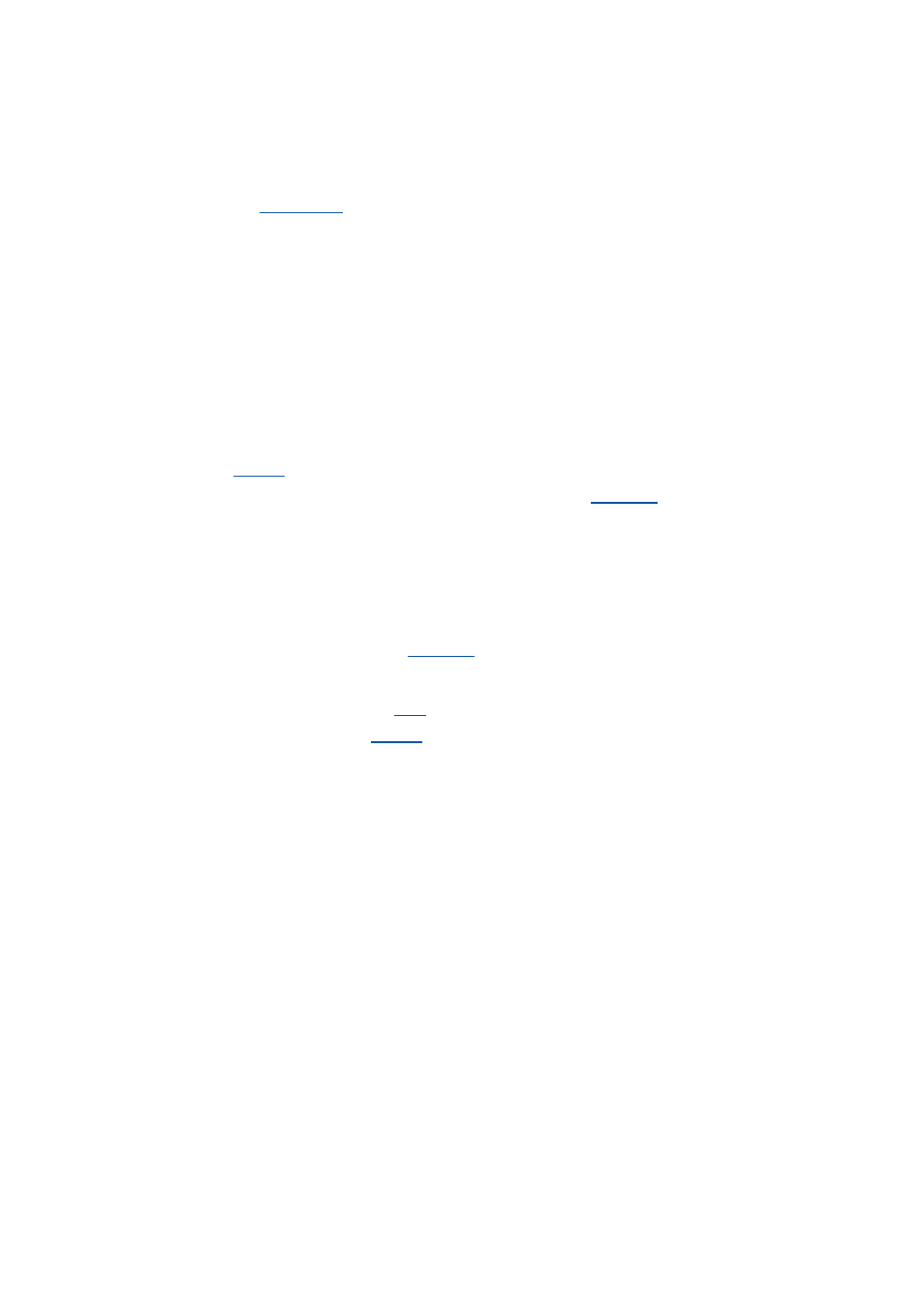
Lenze · Servo-Inverter 9400 HighLine · Reference manual · DMS 10.0 EN · 11/2013 · TD05/06
155
5
Motor interface
5.4
Servo control (SC)
_ _ _ _ _ _ _ _ _ _ _ _ _ _ _ _ _ _ _ _ _ _ _ _ _ _ _ _ _ _ _ _ _ _ _ _ _ _ _ _ _ _ _ _ _ _ _ _ _ _ _ _ _ _ _ _ _ _ _ _ _ _ _ _
How to optimise the torque feedforward control:
1. Run a typical speed profile and record the inputs and outputs of the speed controller with
the
• Motor control variables to be recorded:
Speed.dnSpeedSetpoint (speed setpoint)
Speed.dnActualMotorSpeed (actual speed value)
Torque.dnOutputSpeedCtrl (speed controller output)
Torque.dnTotalTorqueAdd (torque feedforward control)
• Application variable to be recorded (if available):
L_LdMonitFollowError1.dnFollowErrorIn_p (following error)
It is essential for optimising the response to setpoint changes to monitor the speed
controller output (Torque.dnOutputSpeedCtrl) and the torque feedforward control
(Torque.dnTotalTorqueAdd). The effect of the feedforward control can also be observed in
the following error.
2. Select the signal source required for the torque setpoint (feedforward control path) under
.
3. Estimate the load moment of inertia and set it under
end (i.e. considering the gearbox factors).
4. Repeat the oscilloscope recording (see step 1).
Now the oscillogram should show that part of the required torque is generated by the
feedforward control (Torque.dnTotalTorqueAdd) and the speed controller output signal
(Torque.dnOutputSpeedCtrl) should be correspondingly smaller. The resulting following
error decreases.
5. Change the setting under
and repeat the oscilloscope recording until the
intended response to setpoint changes is reached.
• The optimisation could aim at the speed controller being completely relieved (see signal
characteristics in Fig.
).
6. Save parameter set (
= "11: Save start parameters").