3 mutual motor inductance, 5motor interface – Lenze 9400 User Manual
Page 169
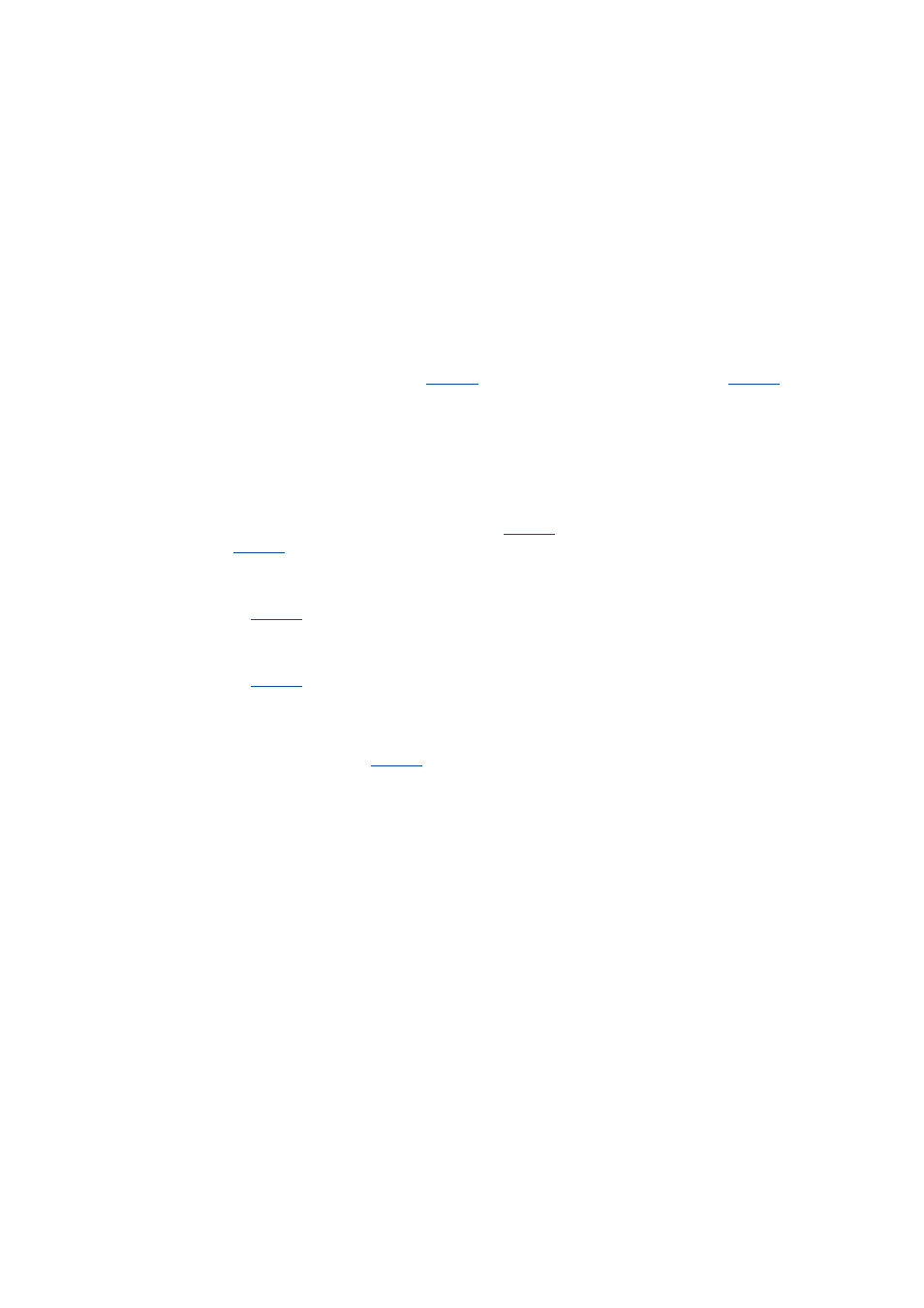
Lenze · Servo-Inverter 9400 HighLine · Reference manual · DMS 10.0 EN · 11/2013 · TD05/06
169
5
Motor interface
5.5
Sensorless vector control (SLVC)
_ _ _ _ _ _ _ _ _ _ _ _ _ _ _ _ _ _ _ _ _ _ _ _ _ _ _ _ _ _ _ _ _ _ _ _ _ _ _ _ _ _ _ _ _ _ _ _ _ _ _ _ _ _ _ _ _ _ _ _ _ _ _ _
5.5.2.3
Mutual motor inductance
Adjustment at rated operation
This adjustment is executed at rated speed and a defined load (e.g. measuring brake) which serves
to define the rated torque. A condition for the adjustment is to know the real load torque. The motor
current is compared to the rated current. At rated load, these two values should be almost identical.
If an adjustment at rated operation is not possible, alternatively execute the adjustment at no-load
operation (see the following section "Adjustment at no-load operation").
How to adjust the mutual motor inductance at rated operation:
1. Set the maximum current in
to 110 % of the rated motor current (
).
2. Select setpoint speed 0 rpm
3. Enable controller.
4. Slowly increase setpoint speed to rated speed (no field weakening) and then keep it at rated
speed constantly.
5. Apply rated load to the motor.
6. Compare the motor current displayed in
with the rated motor current displayed in
.
7. If motor current > rated motor current:
• Reduce the mutual motor inductance stepwise and indirectly via the Lh adjustment in
until the following applies: motor current ≈ rated motor current.
If motor current < rated motor current:
• Increase the mutual motor inductance stepwise and indirectly via the Lh adjustment in
until the following applies: motor current ≈ rated motor current.
8. Unload the motor again and slowly reduce the setpoint speed to 0 rpm again.
9. Inhibit controller.
10. Save parameter set (
= "11: Save start parameters").