Optimising the switching, Performance of the inverter, 5motor interface – Lenze 9400 User Manual
Page 135
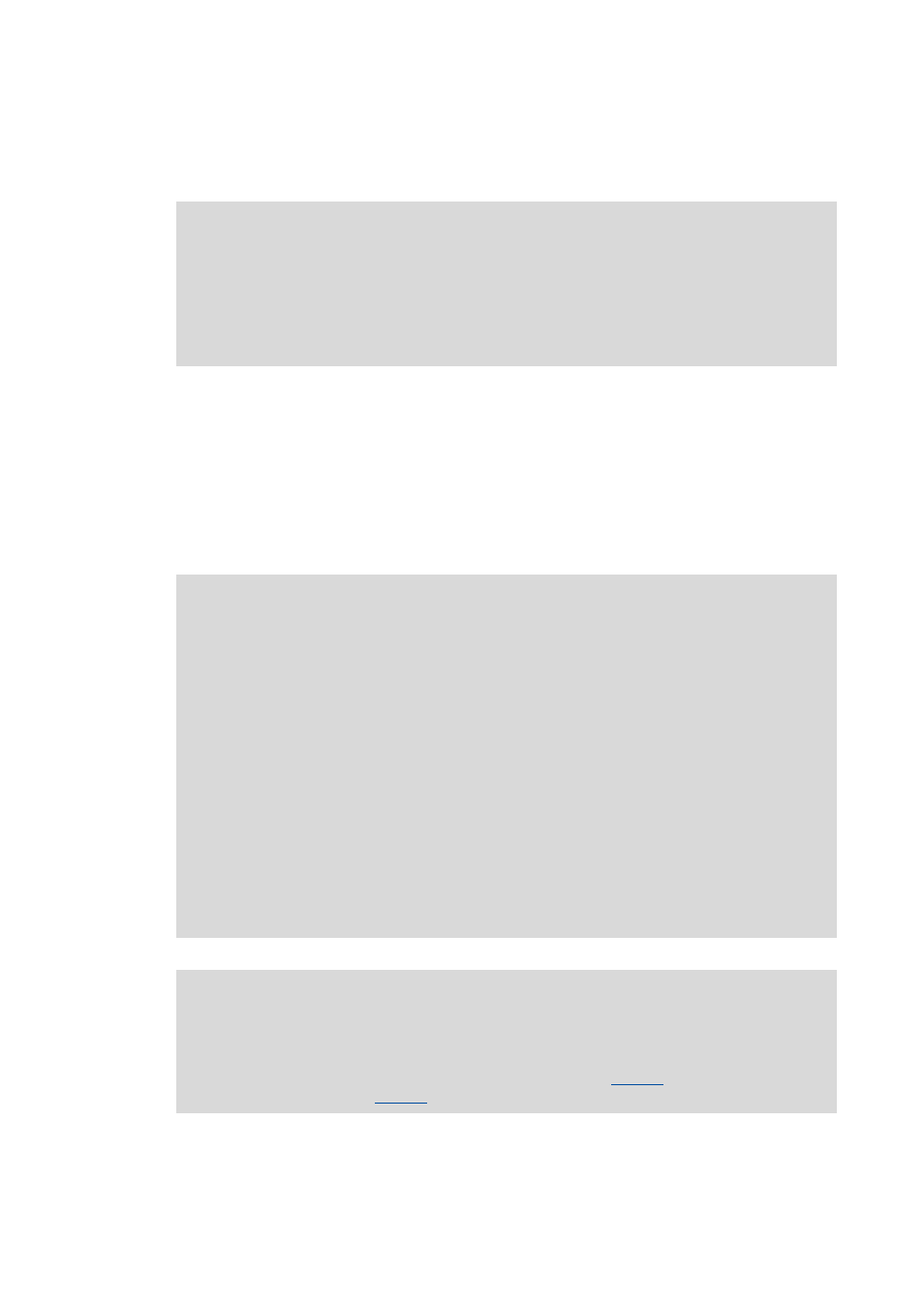
Lenze · Servo-Inverter 9400 HighLine · Reference manual · DMS 10.0 EN · 11/2013 · TD05/06
135
5
Motor interface
5.3
Adjusting motor and controller to each other
_ _ _ _ _ _ _ _ _ _ _ _ _ _ _ _ _ _ _ _ _ _ _ _ _ _ _ _ _ _ _ _ _ _ _ _ _ _ _ _ _ _ _ _ _ _ _ _ _ _ _ _ _ _ _ _ _ _ _ _ _ _ _ _
5.3.4
Optimising the switching performance of the inverter
An inverter generates a pulse-width-modulated, three-phase voltage system. Due to the design of
the inverter, current-dependent and switching frequency-dependent losses inside of the inverter
falsify the voltage that is output. As the voltage that is output is not measured, the losses have to
be compensated by a suitable feedforward control. This compensation is based on an inverter error
characteristic.
Among other things, the inverter error characteristic depends on the length of the motor cable and
at least has to be individually determined once for the connected motor by means of the device
command "Calculate inv. characteristic". For an automatic determination of the motor parameters,
this ensures that the current has a sinusoidal form.
Note!
Only required for servo control if the motor parameters are to be defined by a motor
from a third-party manufacturer!
Always required for sensorless vector control and open loop V/f control!
• An optimum drive performance can only be achieved with the sensorless operating
modes if the voltage errors in the inverter are compensated as exactly as possible.
Danger!
This procedure may only be carried out during commissioning, not during operation!
• During the procedure the motor is energised so that:
• it cannot be excluded that the connected mechanical components may move!
• the windings heat up.
If you repeat the procedure, ensure that the motor is not thermally overloaded
(particularly if no temperature feedback is used).
For software versions lower than V4.0 the following applies:
• If the automatic brake operation is used, ensure that no basic function is requested or
that the application is stopped before this procedure is called. Otherwise the applied
holding brake could be released!
• For positioning applications you have to observe that the absolute position and the
home position will get lost when this procedure is called. The loss of the home
position is not signalled to the application. The following sequence has to be observed
for positioning applications: 1.) Execute identification 2.) Save parameter set
3.) Restart controller 4.) Execute homing procedure.
Note!
For devices of the types 6 + 7 the Ixt monitoring may be activated during the inverter
error characteristic is determined.
Remedy: Only start identification at a device utilisation (
) of 0 % and/or reduce
rated motor current (
) and reset it to the original value after the identification.