2 notes on commissioning using the keypad, Notes on commissioning using the keypad, 3commissioning – Lenze 9400 User Manual
Page 24
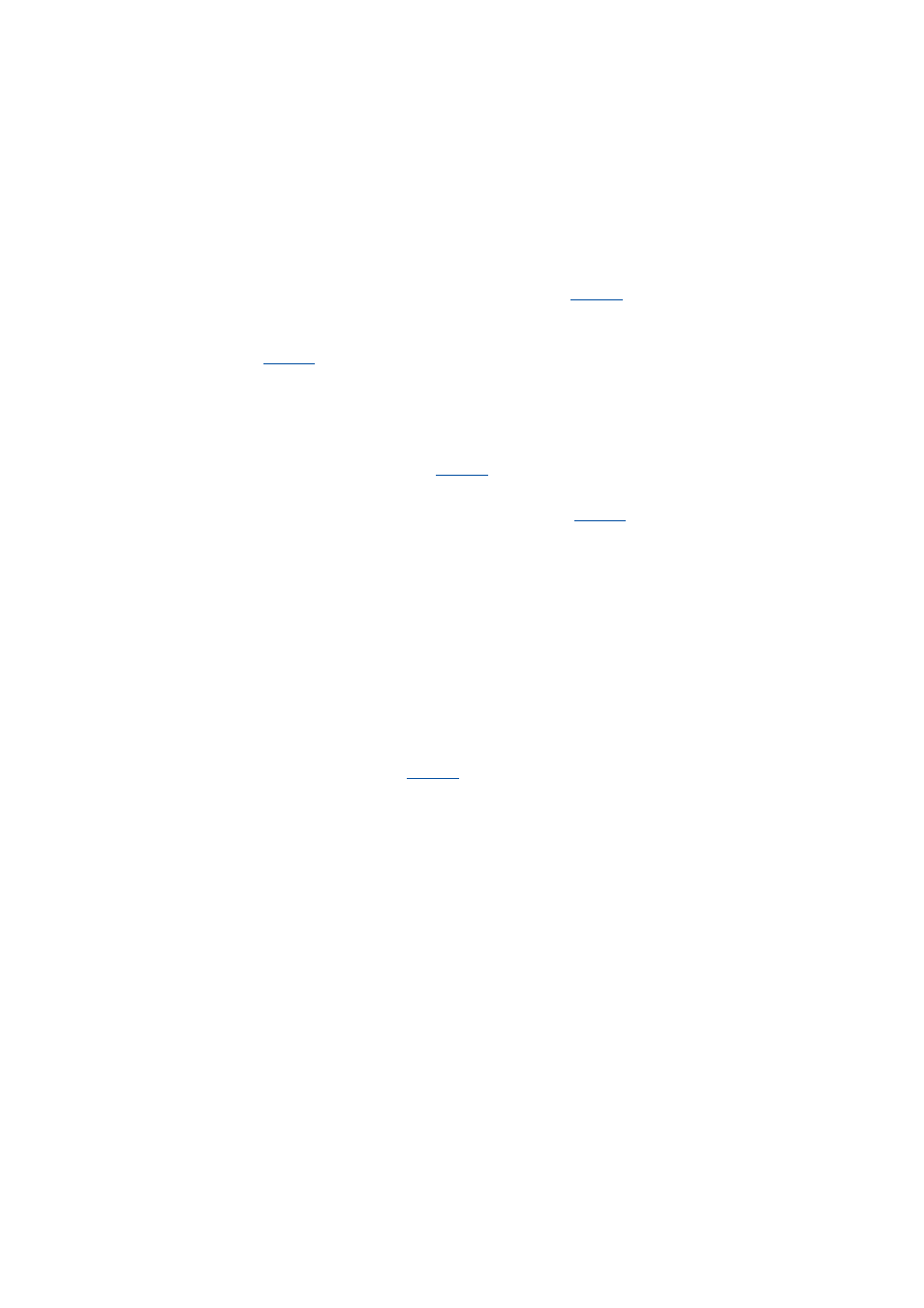
3
Commissioning
3.2
Notes on commissioning using the keypad
24
Lenze · Servo-Inverter 9400 HighLine · Reference manual · DMS 10.0 EN · 11/2013 · TD05/06
_ _ _ _ _ _ _ _ _ _ _ _ _ _ _ _ _ _ _ _ _ _ _ _ _ _ _ _ _ _ _ _ _ _ _ _ _ _ _ _ _ _ _ _ _ _ _ _ _ _ _ _ _ _ _ _ _ _ _ _ _ _ _ _
3.2
Notes on commissioning using the keypad
For a motor with an electronic nameplate (ENP)
• A display of the plant parameters offered by ENP via keypad is not provided. The plant
parameters must be edited and optimised individually.
• To avoid that the motor starts unintentionally without adjusting the plant parameters, the
maximum current in the Lenze setting is set to "0 A" in
• After setting the plant parameters, they have to be saved on the memory module of the
controller with mains failure protection, just as the motor data that have been read out from
the ENP (
= "11: Save start parameters").
For a motor without an electronic nameplate (ENP)
• The motor data and plant parameters must be edited and set individually.
• To avoid that the motor starts unintentionally without adjusting the plant parameters, the
maximum current is set to "0 A" in
by the factory.
• After setting the motor data and plant parameters, they have to be saved on the memory
module of the controller with mains failure protection (
= "11: Save start parameters").
Commissioning of the application
• The application must already be stored on the memory module of the controller. Otherwise
commissioning by only using the keypad is not possible.
• All application parameters which deviate from the factory adjustment have to be edited
individually. For this the project planner has to provide a corresponding list to the commissioner
(including the motor and plant data).
• In the case of a standard set-up, a pole position identification may have to be carried out for
synchronous motors of a third party manufacturer or Lenze synchronous motors with a
Stegmann absolute value encoder.
• After setting the parameters, they have to be saved on the memory module of the controller
with mains failure protection (
= "11: Save start parameters").
Tip!
Detailed information on the individual technology applications can be found in the
corresponding Software Manual for the technology application and the »Engineer« online
help in the chapter "L-force Servo Drives 9400 Technology applications".