3 process data transfer, 12 profibus/profinet option – Lenze 8400 User Manual
Page 701
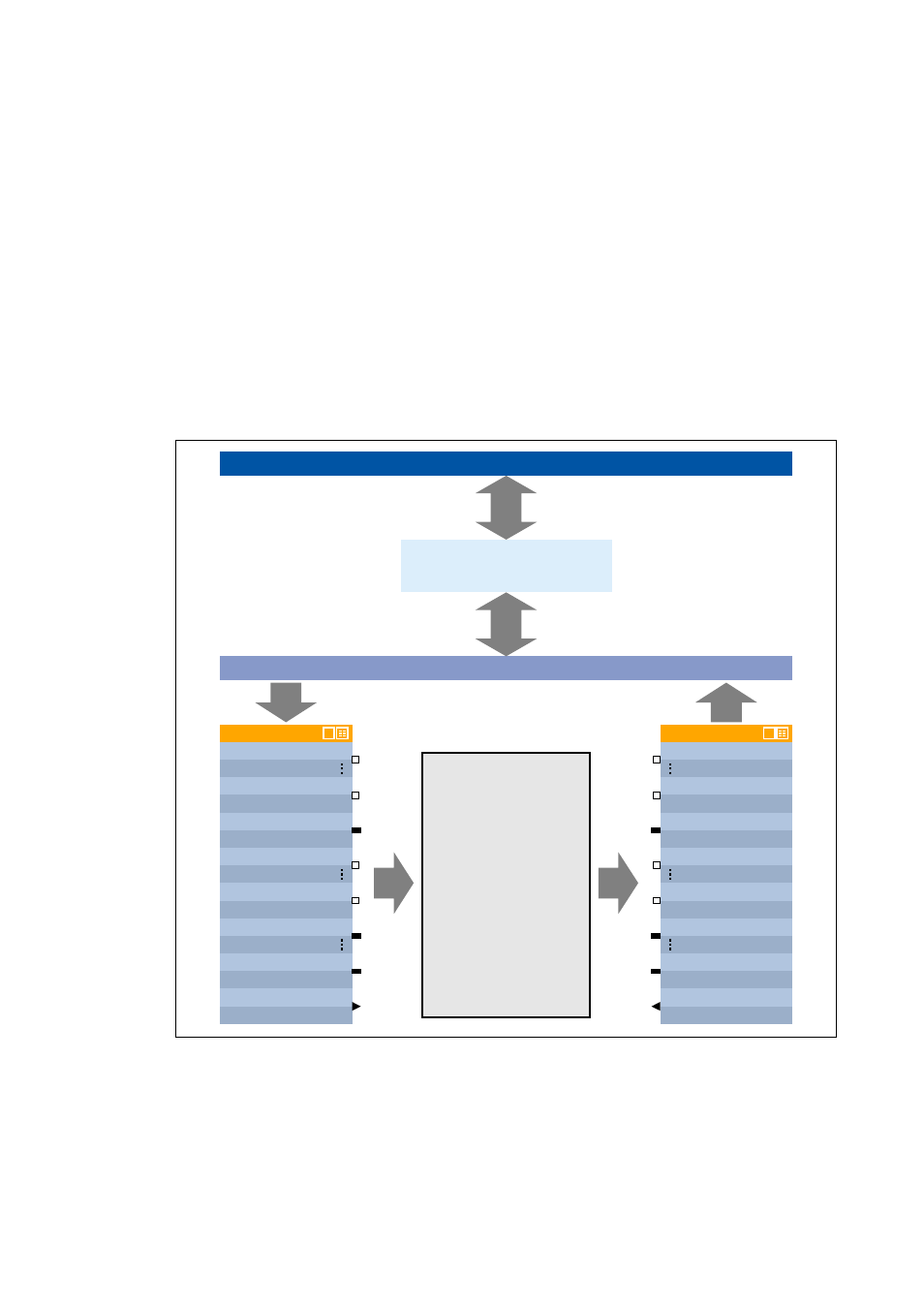
Lenze · 8400 protec HighLine · Reference manual · DMS 3.0 EN · 03/2013 · TD05
701
12
PROFIBUS/PROFINET option
12.3
Process data transfer
_ _ _ _ _ _ _ _ _ _ _ _ _ _ _ _ _ _ _ _ _ _ _ _ _ _ _ _ _ _ _ _ _ _ _ _ _ _ _ _ _ _ _ _ _ _ _ _ _ _ _ _ _ _ _ _ _ _ _ _ _ _ _ _
12.3
Process data transfer
The process data serve to control the controller. Thus the transfer of the process data is time-critical.
• The process cycle is 1ms, irrespective of the respective communication option and the type of
controller.
• Process data transfer takes place cyclically between the master system and the drive controllers.
• This concerns the continuous exchange of current input and output data.
• In the case of the 8400 protec HighLine controller, 16 words per direction are exchanged.
• The master computer can directly access the process data.
Access to the process data takes place via the port blocks LP_MciIn and LP_MciOut (see FB
interconnection of the »Engineer«).
These port blocks are also called process data channels.
• The process data are not saved in the controller.
[12-1] External and internal data transfer between bus system, drive controller and function block interconnection
/3B0FL,Q
"
E&WUOB%
E&WUOB%
Z&WUO
E,QB%
E,QB%
Z,Q
Z,Q
GQ,QBS
/3B0FL2XW
E6WDWHB%
E6WDWHB%
Z6WDWH
E2XWB%
E2XWB%
Z2XW
Z2XW
GQ2XWBS
"
)LHOGEXV
$SSOLFDWLRQ
)%LQWHUFRQQHFWLRQ
&RPPXQLFDWLRQRSWLRQ
0&,LQWHUIDFH