Sensorless control for synchronous motors (slpsm), 5motor control (mctrl), Stop – Lenze 8400 User Manual
Page 198
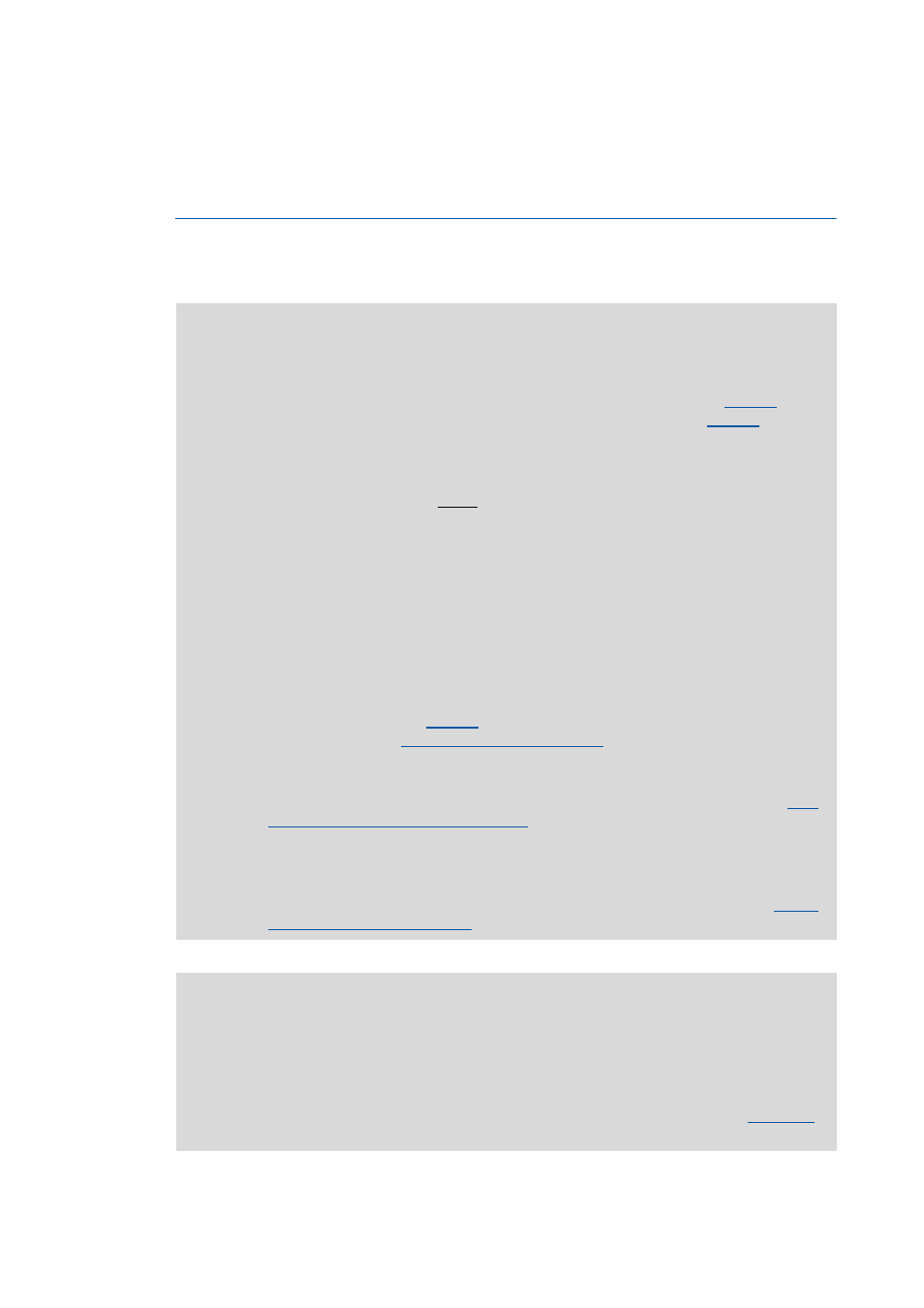
5
Motor control (MCTRL)
5.8
Sensorless control for synchronous motors (SLPSM)
198
Lenze · 8400 protec HighLine · Reference manual · DMS 3.0 EN · 03/2013 · TD05
_ _ _ _ _ _ _ _ _ _ _ _ _ _ _ _ _ _ _ _ _ _ _ _ _ _ _ _ _ _ _ _ _ _ _ _ _ _ _ _ _ _ _ _ _ _ _ _ _ _ _ _ _ _ _ _ _ _ _ _ _ _ _ _
5.8
Sensorless control for synchronous motors (SLPSM)
This function extension is available from version 12.00.00!
The sensorless control for synchronous motors is based on a decoupled and separated control of the
torque-creating and field-creating current share of synchronous motors. In contrast to the servo
control, the actual speed value and the rotor position are reconstructed via a motor model.
Stop!
• The sensorless control for synchronous motors is only possible up to a maximum
output frequency of 650 Hz!
• Depending on the number of motor pole pairs, the reference speed (
) may
only be selected that high that the output frequency displayed in
is lower
than 650 Hz.
• We recommend to select a power-adapted combination of inverter and motor.
• The Lenze setting permits the operation of a power-adapted motor. Optimal
operation is only possible if either:
• the motor is selected via the Lenze motor catalogue
• the motor nameplate data are entered and motor parameter identification is
carried out afterwards
- or -
• the nameplate data and equivalent circuit data of the motor (motor leakage
inductance and motor stator resistance) are entered manually.
• When you enter the motor nameplate data, take into account the phase connection
implemented for the motor (star or delta connection). Only enter the data applying to
the selected connection type.
• In order to protect the motor (e.g. from demagnetisation), we recommend setting the
. This ensures motor protection even with an
unstable operation.
• Controller enable is only possible if the motor is at standstill.
• In the Lenze setting, the rotor displacement angle is identified with every controller
enable and thus a jerk in the machine after controller enable can be avoided.
position identification without motion
• A flying restart circuit for synchronising to rotating motors is in preparation.
• The injection of a constant current may cause an unwanted heating of the motor at
controlled operation.
• We recommend using a temperature feedback via PTC or thermal contact.
Note!
Currently, the sensorless control does not contain a flying restart function that enables
a synchronisation of the controller to a rotating machine.
• Thus, we recommend taking measures for preventing overvoltages at operation in
generator mode (e.g. brake resistor).
• By any means, the delay time for the "DC-bus overvoltage" error trigger in
must be set to 0 s.