5motor control (mctrl), Stop – Lenze 8400 User Manual
Page 273
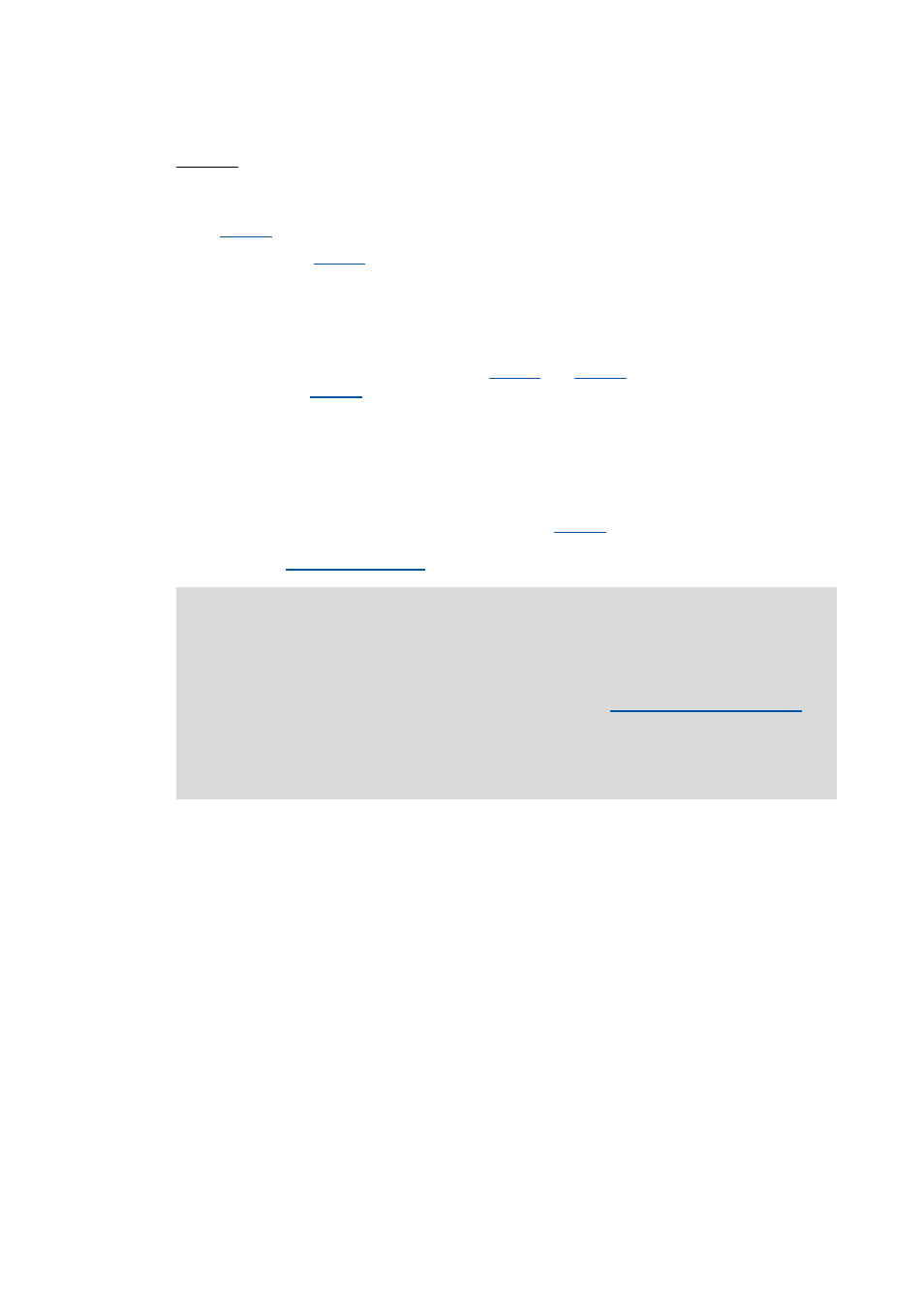
Lenze · 8400 protec HighLine · Reference manual · DMS 3.0 EN · 03/2013 · TD05
273
5
Motor control (MCTRL)
5.13
Braking operation/brake energy management
_ _ _ _ _ _ _ _ _ _ _ _ _ _ _ _ _ _ _ _ _ _ _ _ _ _ _ _ _ _ _ _ _ _ _ _ _ _ _ _ _ _ _ _ _ _ _ _ _ _ _ _ _ _ _ _ _ _ _ _ _ _ _ _
Example:
• A 400 V device has a maximum mains voltage of 420 V AC.
• Maximum stationary DC-bus voltage: 420 V AC * 1.414 = 594 V DC
•
has been set with the selection "0" for 400 V AC mains.
• This means that
can be set to a maximum of 131 V DC (725 V DC - 594 V DC).
5.13.2
Selecting the response to an increase of the DC-bus voltage
If the brake chopper threshold resulting from
is exceeded in the DC bus, the
takes place (use of the brake resistor and/or stop of the ramp function
generator and/or inverter-motor brake).
• Optimum following of the actual speed value until the speed setpoint is reached (e.g. the motor
is stopped rapidly) is always achieved with the help of a brake resistor
• Stopping the ramp function generator enables smoother deceleration with lower torque
oscillation..
• The inverter motor brake is available for selection in
. This function enables rapid
braking without a brake resistor. Torque oscillations can occur due to the traversing
dynamics.
Stop!
• The two braking procedures "Stopping of the ramp function generator" and "Inverter
motor brake" can only be used for speed-controlled applications without the
influence of a position controller!
• When the "inverter motor brake" function is used, the
is
not adapted. If it is braked too frequently, there is a risk of the motor being thermally
overloaded or the motor overload monitoring does not work properly!
• The "inverter motor brake" function must not be used with vertical conveyors (hoists)
or with active loads!