6 network communication, 1 network communication with can on board, Network communication – Lenze E94AxPExxxx User Manual
Page 59: Network communication with can on board, 4plc functionality
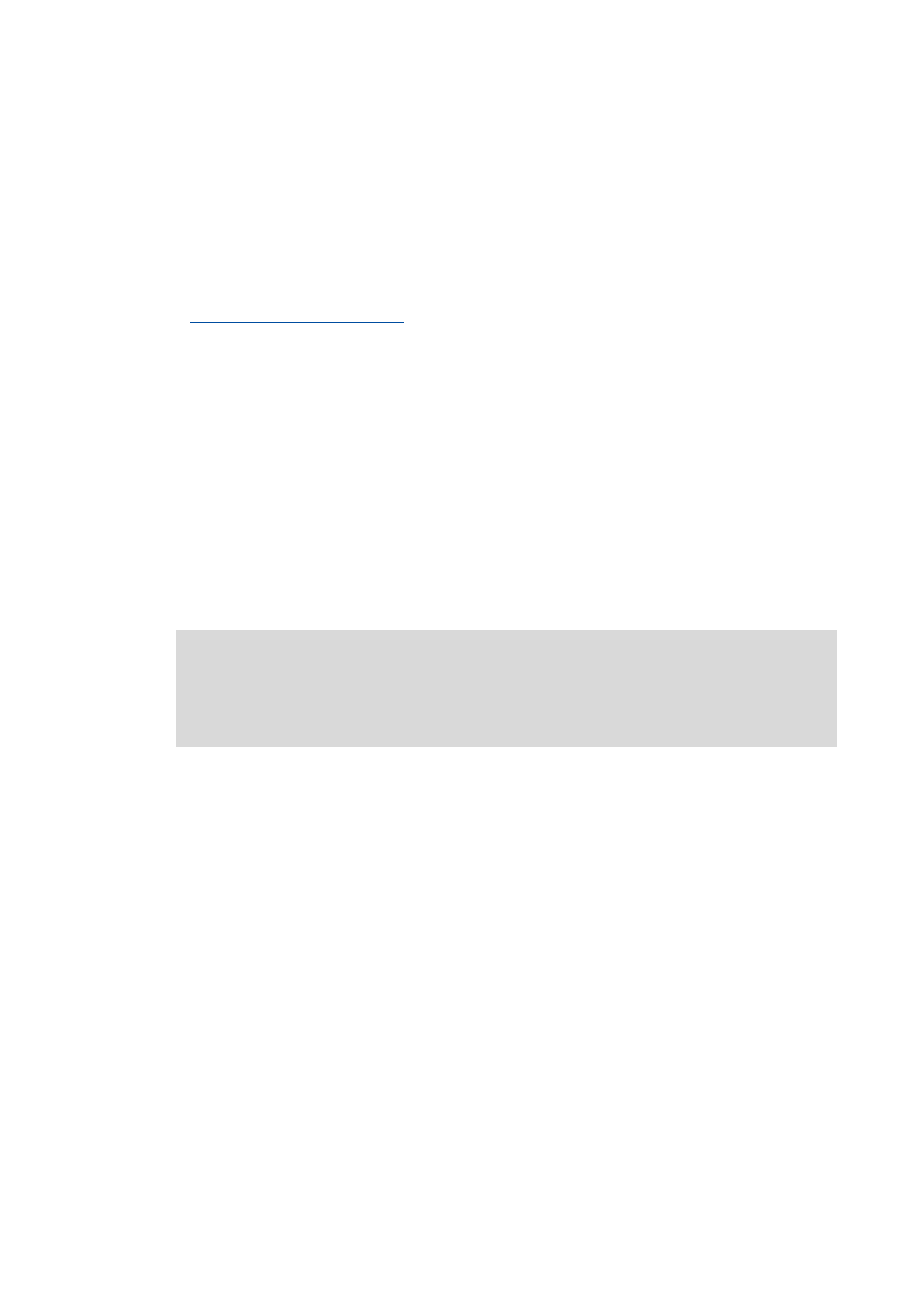
Lenze · 9400 Servo PLC· Reference manual · DMS 4.0 EN · 11/2013 · TD05/06
59
4
PLC functionality
4.6
Network communication
_ _ _ _ _ _ _ _ _ _ _ _ _ _ _ _ _ _ _ _ _ _ _ _ _ _ _ _ _ _ _ _ _ _ _ _ _ _ _ _ _ _ _ _ _ _ _ _ _ _ _ _ _ _ _ _ _ _ _ _ _ _ _ _
4.6
Network communication
Communication between the single components of an entire system requires fieldbus system for
process automation. For the common fieldbus systems, Lenze offers a great number of
communication modules in addition to the CAN system bus.
This section contains information on PDO mapping for the CAN (on board) implemented in the
controller and on PDO mapping for the fieldbus systems to be adapted additionally.
See also:
Communicating with the controller
4.6.1
Network communication with CAN on board
The »9400 ServoPLC« features the following parameterisable process data channels (PDO
channels):
• Max. 4 transmission objects (transmit PDO, TPDO) with 1 ... 8 bytes
• Max. 4 transmission objects (receive PDO, RPDO) with 1 ... 8 bytes
PDO mapping in »Engineer«
The data exchange between the »CAN on board« interface and the PLC program is carried out via
ports. In the Ports tab, 30 input ports and 30 output ports are created.
PDO mapping means the connection of the parameterisable process data channels with the ports
of the controller.
Tip!
The general online help of »Engineer« describes PDO mapping in the section entitled Insert
and configure network / Process data objects.
Note!
In contrast to the »9400 HighLine«, in the case of the »9400 ServoPLC« the user cannot
create his own ports. Instead of that, a set of fixed ports is provided under the Ports tab,
via which a port interconnection can be carried out.