3 pole position identification, Pole position identification, 6motor interface – Lenze E94AxPExxxx User Manual
Page 176
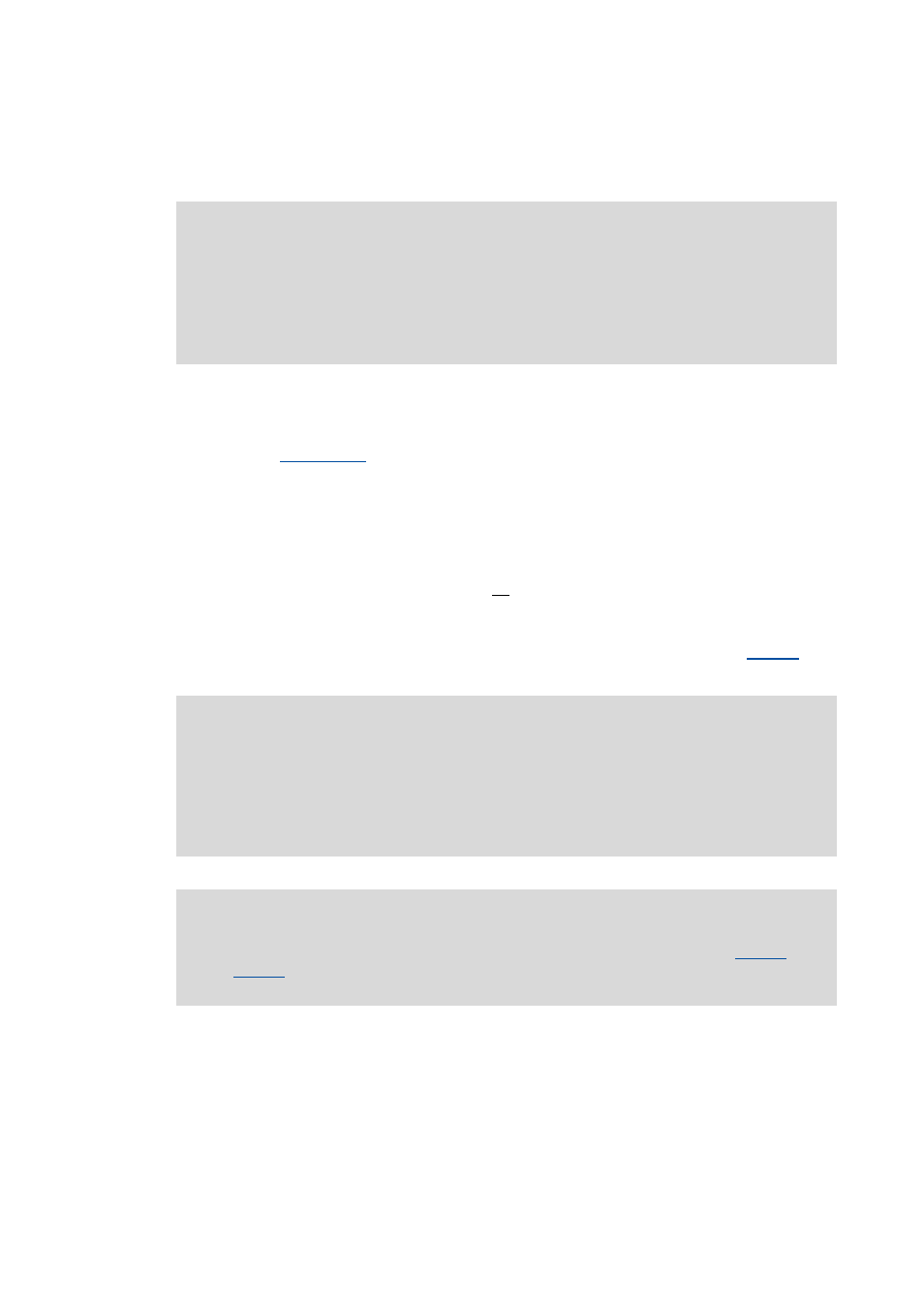
6
Motor interface
6.3
Adjusting motor and controller to each other
176
Lenze · 9400 Servo PLC· Reference manual · DMS 4.0 EN · 11/2013 · TD05/06
_ _ _ _ _ _ _ _ _ _ _ _ _ _ _ _ _ _ _ _ _ _ _ _ _ _ _ _ _ _ _ _ _ _ _ _ _ _ _ _ _ _ _ _ _ _ _ _ _ _ _ _ _ _ _ _ _ _ _ _ _ _ _ _
6.3.3
Pole position identification
For the control of permanent-magnet synchronous machines, the pole position – the angle between
the motor phase U and the field axis of the rotor – must be known.
• For Lenze motors with absolute value encoder or resolver, the pole position is already set
.
• When incremental encoders (TTL or sin/cos encoders) are used, a pole position identification
(PPI) is always required after mains switching, even with Lenze motors.
• The controller can also evaluate multi-pole-pair resolvers.
• When the number of motor pole pairs is an integer multiple of the number of pole pairs of
the resolver, a pole position identification must only be executed once.
• When the number of motor pole pairs is no integer multiple of the number of pole pairs of
the resolver, a pole position identification must be executed after every mains switching.
• The device commands "Identify pole position (360°)" and "Identify pole position (min. motion)"
serve to determine the pole position for the motor encoder currently activated in
(see
the following instructions).
Note!
Only required:
• For servo control with synchronous motor of a third-party manufacturer.
• For servo control with synchronous motor and use of incremental encoders (TTL or
sin/cos encoders as well as multi-pole pair resolvers).
• After changes of the motor feedback system, e.g. encoder exchange.
Danger!
The machine must not be braked or blocked during the pole position identification! For this
reason, the pole position identification is not permitted for hanging loads!
During the pole position identification the rotor aligns itself. The motor shaft moves by
max. one electrical revolution which causes the corresponding movement of the connected
mechanical components!
Stop!
Check the correct parameterisation of the max. motor current monitoring (
) before carrying out the pole position identification to prevent the motor from
being permanently damaged.