2 optimising motor parameters, Optimising motor parameters, 6motor interface – Lenze E94AxPExxxx User Manual
Page 214
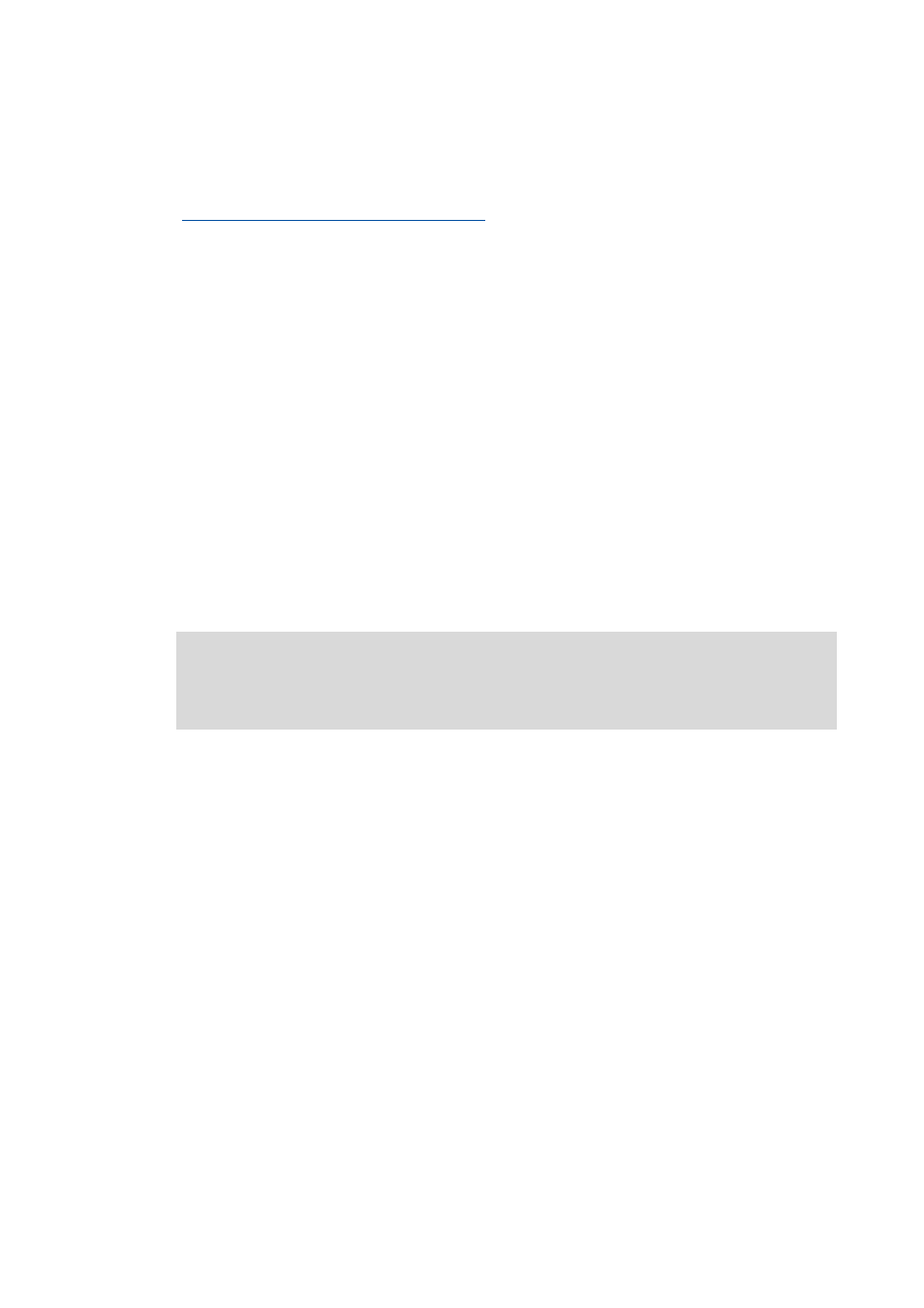
6
Motor interface
6.5
Sensorless vector control (SLVC)
214
Lenze · 9400 Servo PLC· Reference manual · DMS 4.0 EN · 11/2013 · TD05/06
_ _ _ _ _ _ _ _ _ _ _ _ _ _ _ _ _ _ _ _ _ _ _ _ _ _ _ _ _ _ _ _ _ _ _ _ _ _ _ _ _ _ _ _ _ _ _ _ _ _ _ _ _ _ _ _ _ _ _ _ _ _ _ _
6.5.2
Optimising motor parameters
Although the motor parameters have been determined before as described in the chapter
"
Adjusting motor and controller to each other
", an additional optimisation may be required in the
following cases using the adjustment processes described in this chapter:
• When the concentricity factor in the lowest speed range is to be improved.
• When the stability in the lower speed range is to be improved.
• When the rated torque is not reached in the rated point, i. e. at rated speed and rated current.
• When a too high magnetising current is injected in idle state.
General information on the motor parameter adjustment
The motor stator resistance can generally always be adjusted with a passive load since the motor is
stopped when this parameter is set.
An optimisation of the mutual motor inductance, however, is only sensible when the motor rotates
in the medium speed range. In the majority of cases, the no-load operation is sufficient for this
adjustment. In contrast to the rated operation, the no-load operation is also possible for initial
commissioning in many applications.
The motor rotor resistance can only be adjusted exactly if the current motor speed is available. Thus,
for this adjustment only applications are considered where a speed measurement is possible, even
with a manual tachometer. If, under operating conditions (e.g. at rated load), the motor consumes
more than the rated motor current indicated, an adjustment can also be executed by reducing the
mutual motor inductance.
Note!
To execute the adjustment processes described in the following subchapters, the
controller must always be enabled!