4 motor phase failure monitoring, Motor phase failure monitoring, 6motor interface – Lenze E94AxPExxxx User Manual
Page 274
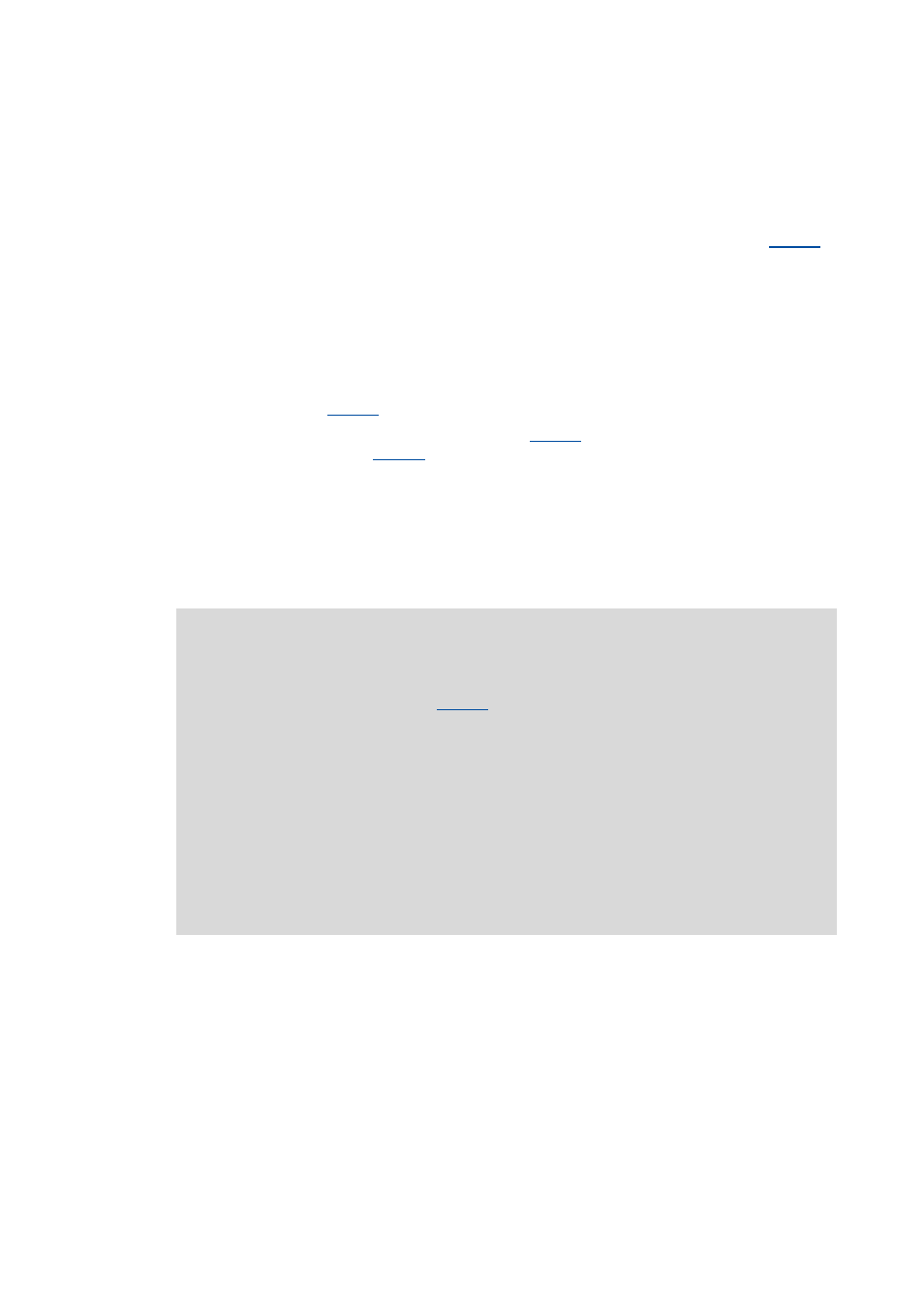
6
Motor interface
6.9
Monitoring
274
Lenze · 9400 Servo PLC· Reference manual · DMS 4.0 EN · 11/2013 · TD05/06
_ _ _ _ _ _ _ _ _ _ _ _ _ _ _ _ _ _ _ _ _ _ _ _ _ _ _ _ _ _ _ _ _ _ _ _ _ _ _ _ _ _ _ _ _ _ _ _ _ _ _ _ _ _ _ _ _ _ _ _ _ _ _ _
6.9.4
Motor phase failure monitoring
6.9.4.1
Monitoring of the individual motor phases during operation
If a current-carrying motor phase (U, V, W) fails during operation, the response set in
is
executed (Lenze setting: "No response") if two conditions are fulfilled:
Condition 1: Monitoring is activated
To safely detect a motor phase failure, a certain motor current must flow for the current sensor
system.
• Monitoring will therefore only be activated if, in the case of servo control the setpoint of the
motor current, and in the case of sensorless vector control or V/f control the actual value motor
current (display in
) has exceeded a certain current value.
• The current value for the activation can be set in
in [%] with regard to the maximum
device current (display in
Condition 2: A certain commutation angle has been covered
In this case monitoring works according to the principle of checking for each motor phase that a
current flows depending on the commutation angle.
• Monitoring responds if a certain commutation angle (approx. 150°) is covered without the
current having exceeded a (non-parameterisable) threshold that depends on the device power.
Note!
• In case of sensorless vector control or V/f control, the safe detection of a motor phase
failure is only carried out if the actual current has exceeded the 3.5-fold value of the
.
• The dependence on the commutation angle also causes a dependence on the motor
type used:
• The commutation angle and the angle at the shaft (number of pole pairs) of a
synchronous machine are proportional. This makes it possible to predict which
shaft angle is maximally covered in case of error.
• An asynchronous machine has an additional slip between the commutation angle
and the angle on the shaft. This results in a load dependency due to which it is
impossible to predict the maximally covered shaft angle in the event of a fault.
In certain applications (e.g. hoists during lowering operation at non-zero speeds) it
may be possible that a rotating field is no longer applied. Instead, a DC current
flows. In this case, condition 2 is no longer met.