7encoder evaluation – Lenze E94AxPExxxx User Manual
Page 290
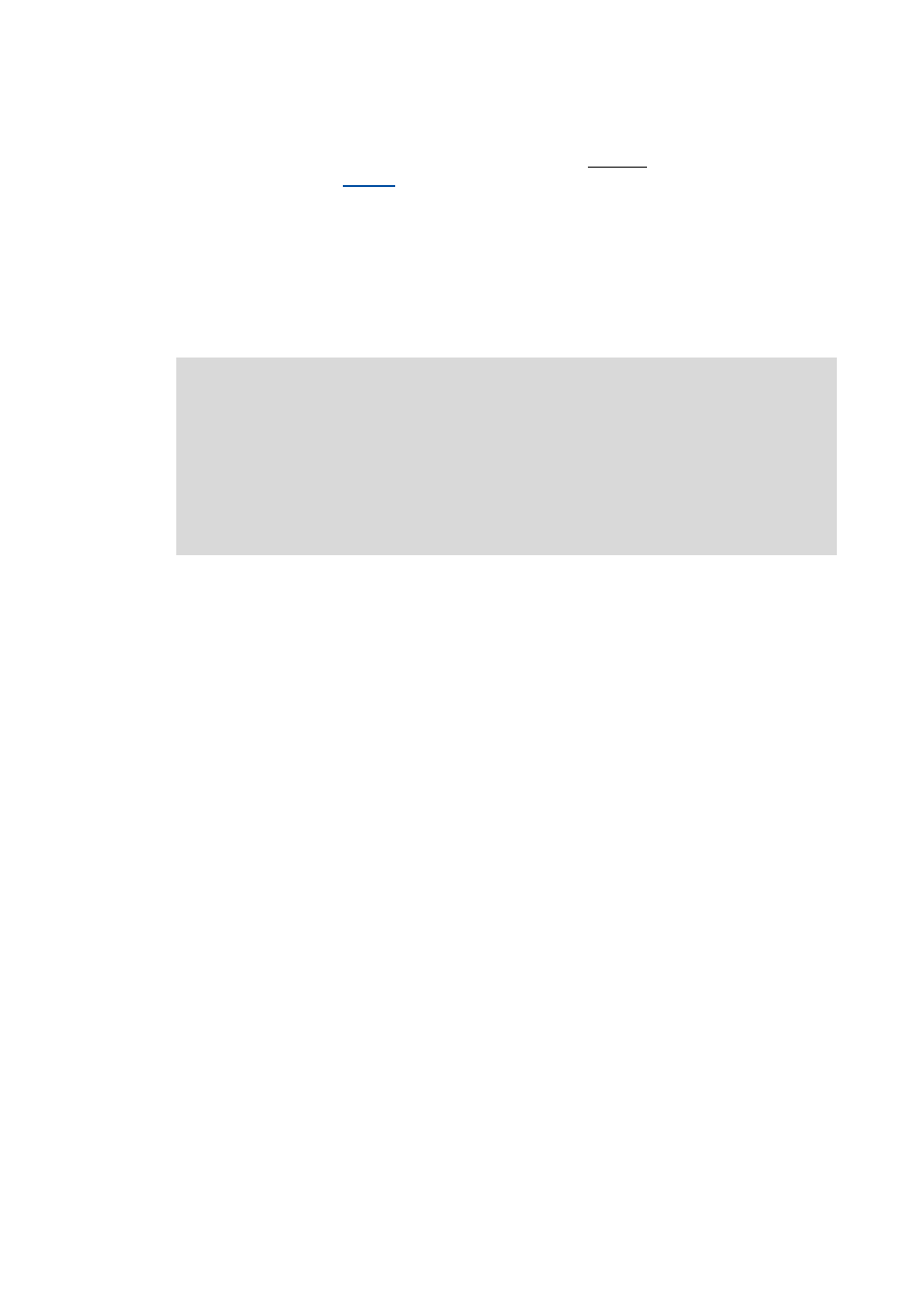
7
Encoder evaluation
7.3
Parameter setting
290
Lenze · 9400 Servo PLC· Reference manual · DMS 4.0 EN · 11/2013 · TD05/06
_ _ _ _ _ _ _ _ _ _ _ _ _ _ _ _ _ _ _ _ _ _ _ _ _ _ _ _ _ _ _ _ _ _ _ _ _ _ _ _ _ _ _ _ _ _ _ _ _ _ _ _ _ _ _ _ _ _ _ _ _ _ _ _
If a position encoder is used as well as the motor encoder, it is essential that position control is used
instead of angle control (
Rotative encoders as well as linear distance measuring devices can be used as position encoders.
The feedback from position encoders (SSI-, EnDat-, TTL-, Sin/Cos-, Hiperface encoder) is transferred
via encoder input X8, with the exception of fieldbus encoders.
If a fieldbus encoder is used, the fieldbus interface is used for position feedback.
The actual position value is passed on to the position controller via the system block available for
encoder evaluation LS_Feedback. For this purpose, the actual position value must be connected to
the input FDB_dnActPosIn_p.
Note!
The use of an SSI encoder is a special case:
• Position feedback takes place via encoder input X8 as is the case with most position
encoders.
• Processing of the actual position value is carried out in the same way as in the case of
a fieldbus encoder. The actual position is passed on to the position controller via the
system block available for encoder evaluation LS_Feedback. For this purpose, the
actual position value must be connected to the input FDB_dnActPosIn_p.