7encoder evaluation – Lenze E94AxPExxxx User Manual
Page 291
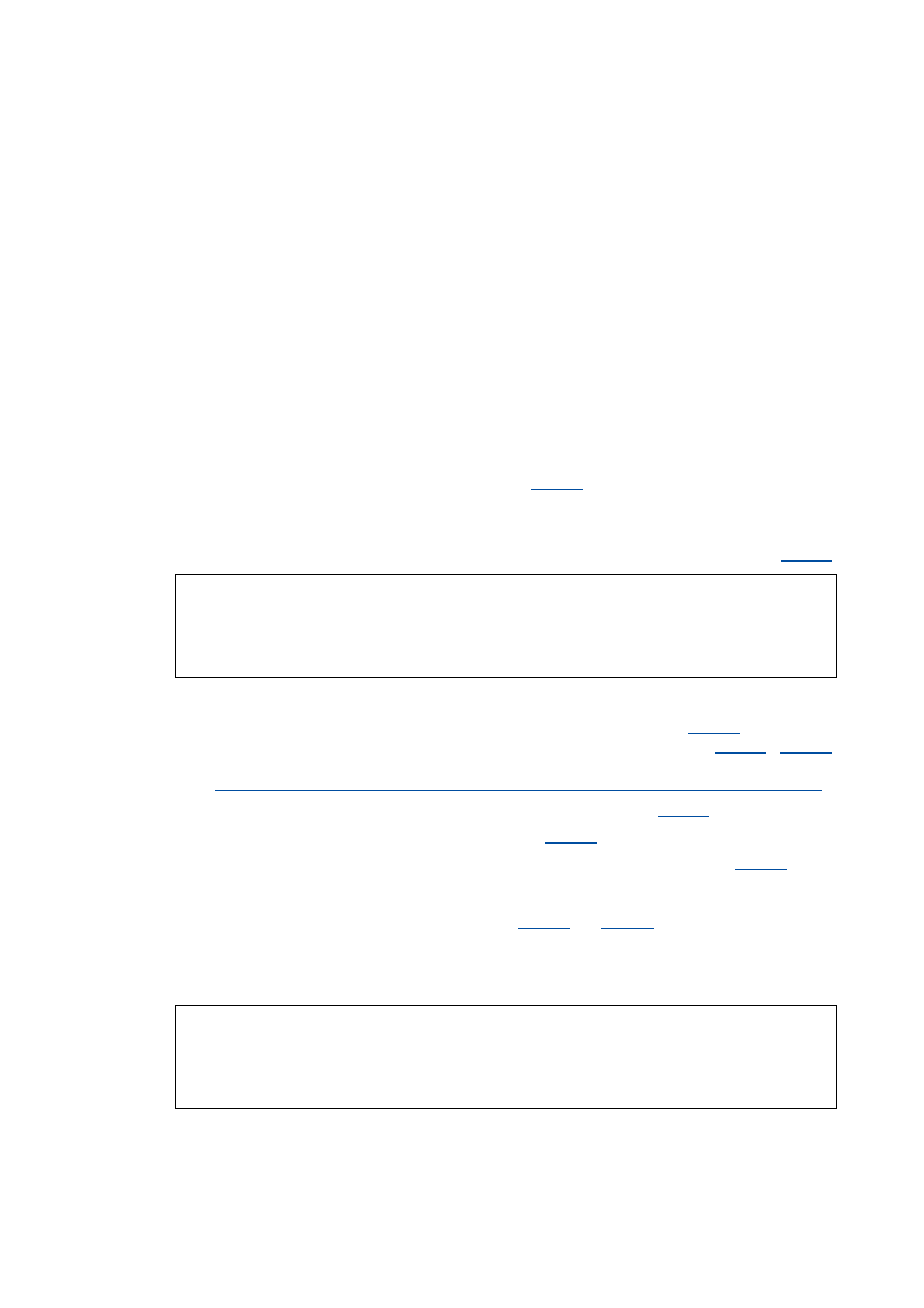
Lenze · 9400 Servo PLC· Reference manual · DMS 4.0 EN · 11/2013 · TD05/06
291
7
Encoder evaluation
7.3
Parameter setting
_ _ _ _ _ _ _ _ _ _ _ _ _ _ _ _ _ _ _ _ _ _ _ _ _ _ _ _ _ _ _ _ _ _ _ _ _ _ _ _ _ _ _ _ _ _ _ _ _ _ _ _ _ _ _ _ _ _ _ _ _ _ _ _
7.3.4
Position feedback with a linear distance measuring device
Linear distance measuring devices (e.g. with Hiperface
®
or EnDat interface) are only used for
additional position feedback in the case of servo-controlled drives. For speed and current control, a
motor encoder is always necessary.
For applications with low requirements regarding dynamic response and speed accuracy, the use of
sensorless V/F control (VFCplus) and position feedback for position control is possible.
7.3.4.1
Conversion from linear to rotative encoder variables
Like the signals of rotative position encoders, the signals of linear distance measuring devices are
read in at encoder input X8. The actual position value of these usually optical encoders is thus
directly available for position control. Additional block interconnection is not necessary.
Evaluation at encoder input X8 is designed for rotary encoders. In order to adapt the linear system,
conversion to (notional) rotative values, which have to be entered in the code, is necessary.
Conversion for the number of encoder increments in
In the case of linear distance measurement devices, the encoder resolution is usually indicated in
the form of graduations in [μm] or as a number of increments per millimetre [inc/mm].
The following rule of thumb can be used to determined the number of encoder increments
[7-4]
Determination of the number of encoder increments of linear distance measuring devices
The integer value (INT = integer part of the calculation) must be entered in
rounding-off error is corrected by means of the position encoder gearbox factor (
in the machine parameters.
See
Determination of the position encoder gearbox factor of linear distance measuring devices
The resulting maximum position which can be shown can be checked in
.
The maximum speed that can be shown is indicated in
If the necessary speeds and positions for the application can no longer be shown,
enlarged. The internal resolution is thus decreased.
Calculation of the position encoder gearbox factor
Please note that, when the number of encoder increments in the numerator of the following
formula is indicated, the value with decimal places must be given whereas, in the numerator, the
integer (INT = integer) is used for purposes of calculation:
[7-5]
Determination of the position encoder gearbox factor of linear distance measuring devices
Number of encoder increments
Feed constant [units/rev]
Encoder graduation [units]
---------------------------------------------------------------------
=
C00420 = INT number of encoder increments
C02524
Encoder graduation
---------------------------------------------------
=
Position encoder - gearbox factor
Encoder Strichzahl (incl. decimal places)
–
Number of encoder increments (integer)
-----------------------------------------------------------------------------------------------------------------
=
C02522
C02523
--------------------
Number of encoder increments (incl. decimal places)
C00420
----------------------------------------------------------------------------------------------------------------------------------------
=