7encoder evaluation – Lenze E94AxPExxxx User Manual
Page 299
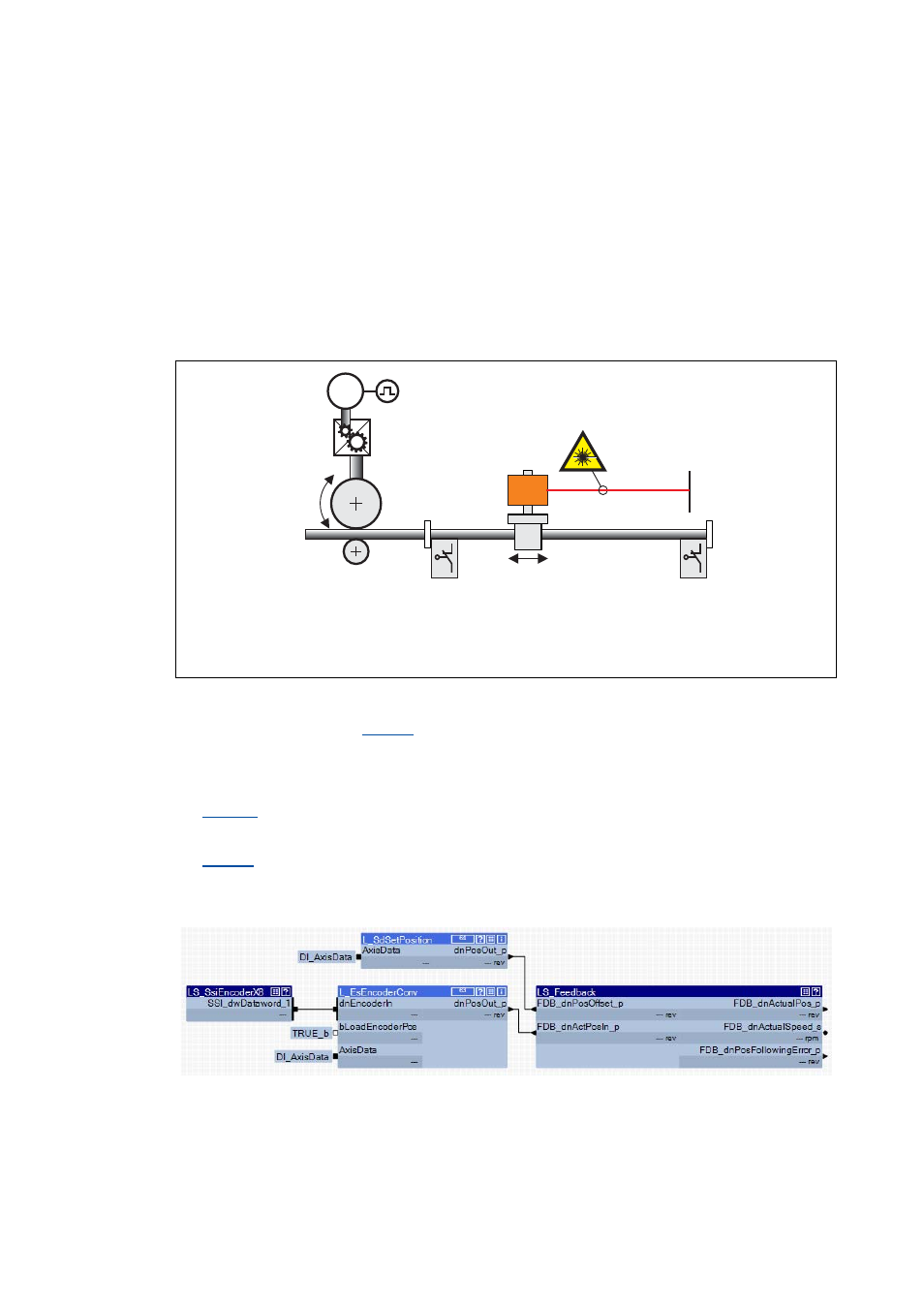
Lenze · 9400 Servo PLC· Reference manual · DMS 4.0 EN · 11/2013 · TD05/06
299
7
Encoder evaluation
7.3
Parameter setting
_ _ _ _ _ _ _ _ _ _ _ _ _ _ _ _ _ _ _ _ _ _ _ _ _ _ _ _ _ _ _ _ _ _ _ _ _ _ _ _ _ _ _ _ _ _ _ _ _ _ _ _ _ _ _ _ _ _ _ _ _ _ _ _
Example: Position encoder feedback with an SSI linear distance measuring device
The current position of a positioning unit is detected with a laser distance measuring device (e.g.
»DME5000«) with an SSI interface. A graduation of 0.1 mm has been parameterised in the linear
distance measuring device.
The positioning unit is moved by 848.23 mm in an axial direction for each revolution of the slip-free
drive roll. The current motor speed is detected by a resolver.
A position offset of 100 mm must be taken into account due to installation of the distance
measuring device and the reflector.
The lower 24 bits of the SSI data word contain information coded in Gray.
[7-11] Schematic diagram of feedback with laser distance measuring device DME5000
The Multiturn resolution (
C05274
) that is set must allow the entire traversing range of the
application to be represented and must also ensure that the display limit in the 9400 device is not
exceeded.
• Minimum Multiturn resolution.
C05274
= Maximum traversing range / feed constant = 59
• Maximum Multiturn resolution
C05274
= 2
31
-1 / resolution of Singleturn = 253181
Required FB interconnection
Motor encoder
Laser distance measuring device
Feed rate of the screw
Laser beam/reflective surface
Circumference of the drive roll = 848,23 mm
M
DME
5000
?