Axis fault – Rockwell Automation GMLC Reference Manual User Manual
Page 737
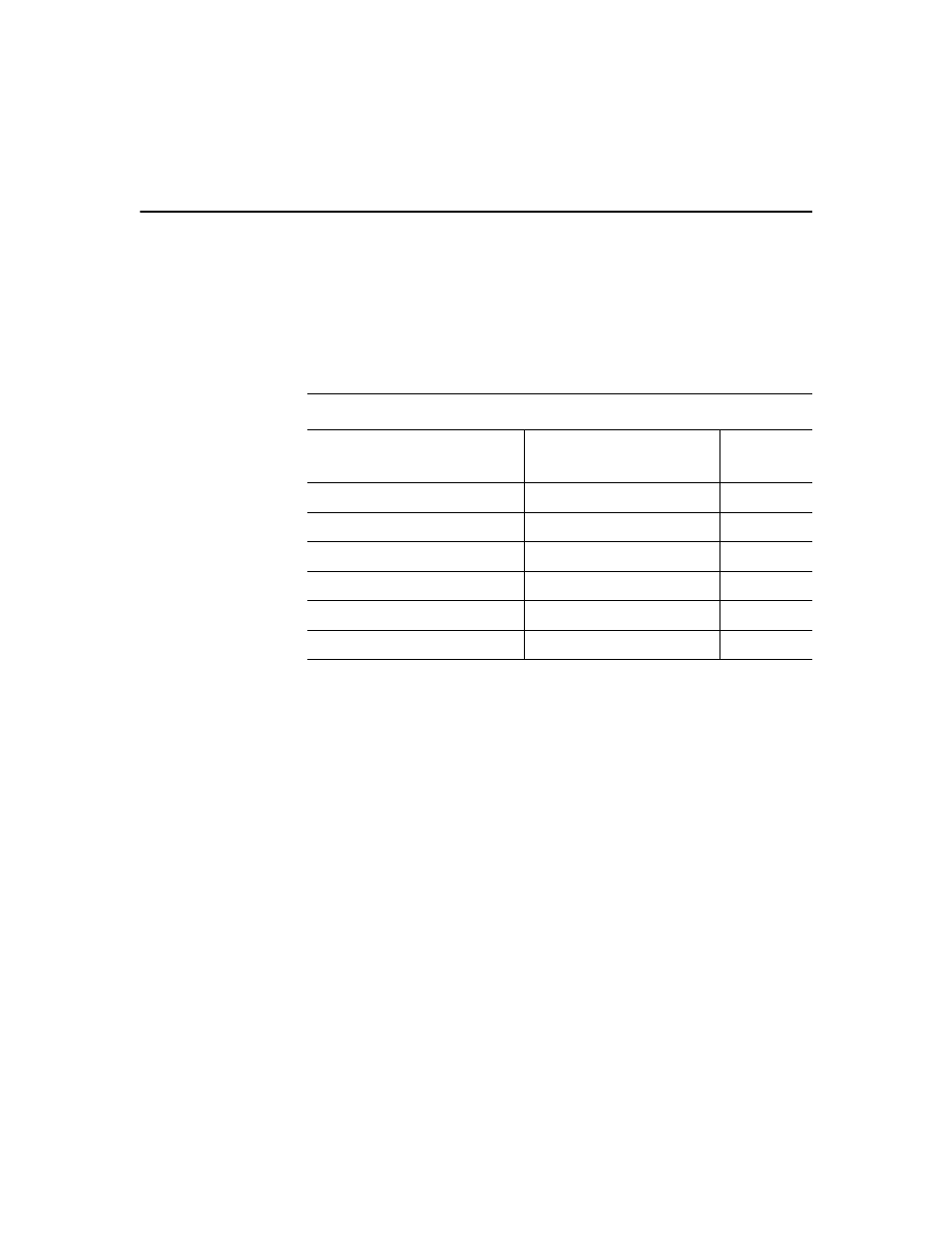
Publication GMLC-5.2 - November 1999
700
Using the RIO Adapter Option
Axis Fault
The axis fault output for each axis (SLC or PLC inputs 4 – 7) is set
whenever an axis fault occurs
(Axis_fault
> 0). The next table shows
the axis faults that trigger an axis fault output, and the corresponding
message that appears in the Terminal Window (or Runtime Display, if
enabled).
If no axis faults have occurred (Axis_fault = 0), the fault output for the
axis is cleared and the message “No Fault” appears in the Terminal
Window (or Runtime Display, if enabled.)
Specifically, the axis fault output for an axis is set whenever the
corresponding Axis_fault variable in GML Commander has a value
greater than 0, and cleared whenever it has a value of 0. See the Status
Variables chapter of this manual for more information on Axis_fault.
To determine which fault is active when one of the axis fault bits is set,
the PLC should issue a block transfer read of the appropriate axis fault
status variable in the motion controller. See Using Block Transfers in this
chapter for more information.
Axis Faults
Description
On Watch & Axis System
Variable Display
Runtime
Display
Drive Fault
Drive_fault
DRV FLT
Position Error Tolerance Exceeded
Position_error_fault
ERR FLT
Hardware Overtravel Fault
Hardware_overtravel_fault
HRD LIM
Software Travel Limits Exceeded
Software_overtravel_fault
SFT LIM
Encoder Noise Fault
Encoder_noise_fault
ENC FLT
Encoder Loss Fault
Encoder_loss_fault
ENC FLT