Rockwell Automation GMLC Reference Manual User Manual
Page 560
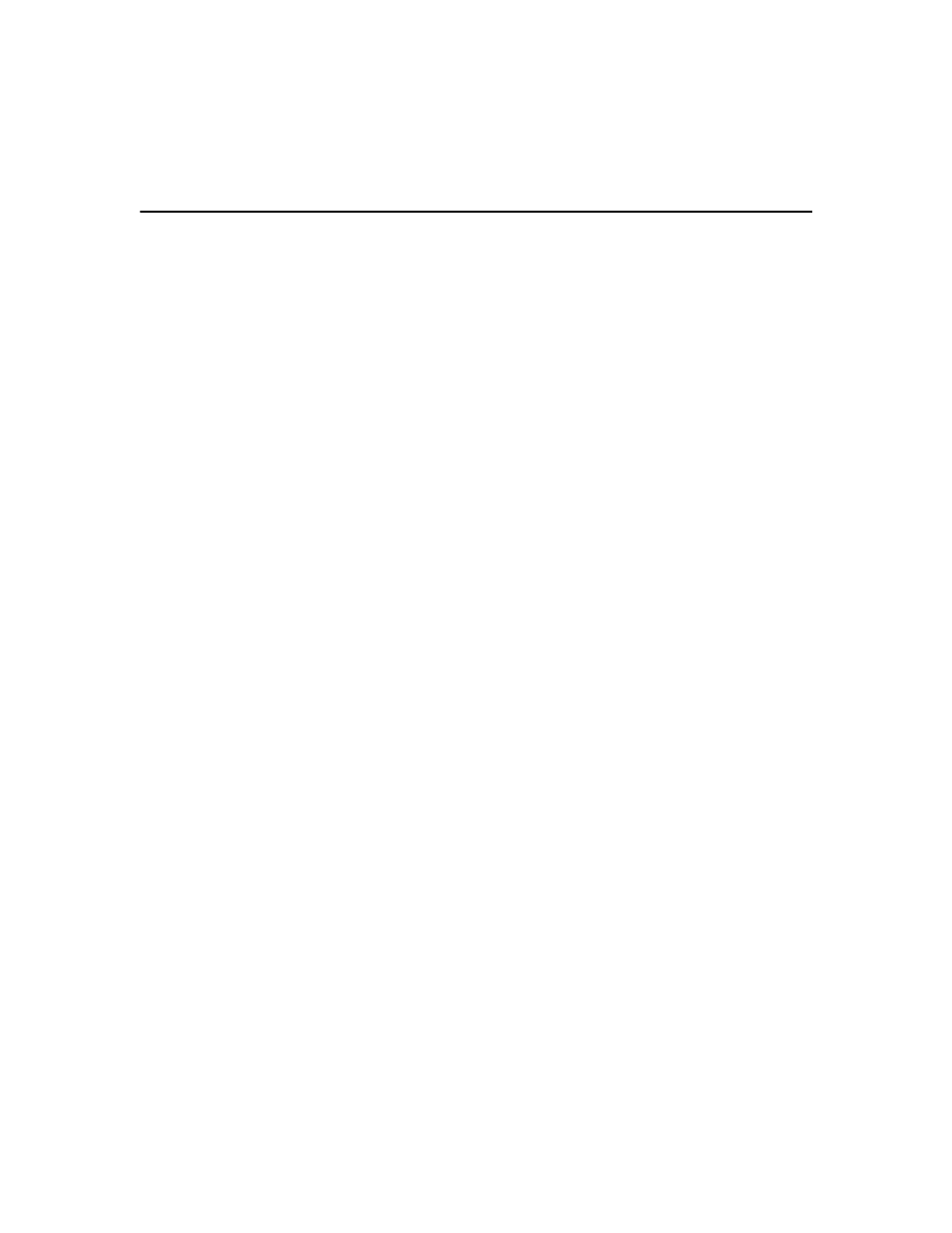
Publication GMLC-5.2 - November 1999
523
•
0 (false) if not
Note: An Encoder is sometimes alternately referred to as a Transducer.
Thus, Encoder Loss Fault is sometimes referred to as Transducer
Loss Fault
In the Tag Explorer, select both Axis System Variables and the desired
physical axis, then select Encoder_loss_fault in the Tag Window.
When evaluated in an expression, the value of the Encoder_loss_fault
variable indicates whether encoder signal loss has been detected on the
encoder input for the axis.
When Encoder_loss_fault = 1, Axis_fault = 1, Axis_status = 7 if no other
faults of higher priority are active on the axis, and Global_fault = 14 if no
other faults of higher priority are active on any axis.
Encoder loss fault is indicated if either of the following occur:
•
Both of the differential signals for any encoder channel (A+ and A-,
B+ and B-, or Z+ and Z-) are at the same level (both low). Under
normal operation, the differential signals are always at opposite
levels. The most common cause of this situation is a broken wire
between the encoder and the motion controller.
•
Loss of encoder power or encoder common to the motion controller
or the encoder.
Each physical axis of the motion controller can be configured to respond
to encoder loss in different ways. If the transducer loss fault action is set
to DISABLE DRIVE, when transducer loss is detected, axis feedback is
immediately disabled, the servo amplifier output is zeroed, and the
appropriate drive enable output is deactivated. If the transducer loss fault
action is set to STATUS ONLY, encoder loss faults must be handled
within the GML Commander diagram. See the Setup section of the
Installation and Setup manual for your motion controller for more
information on configuring the encoder loss fault action.