Reset fault – Rockwell Automation GMLC Reference Manual User Manual
Page 221
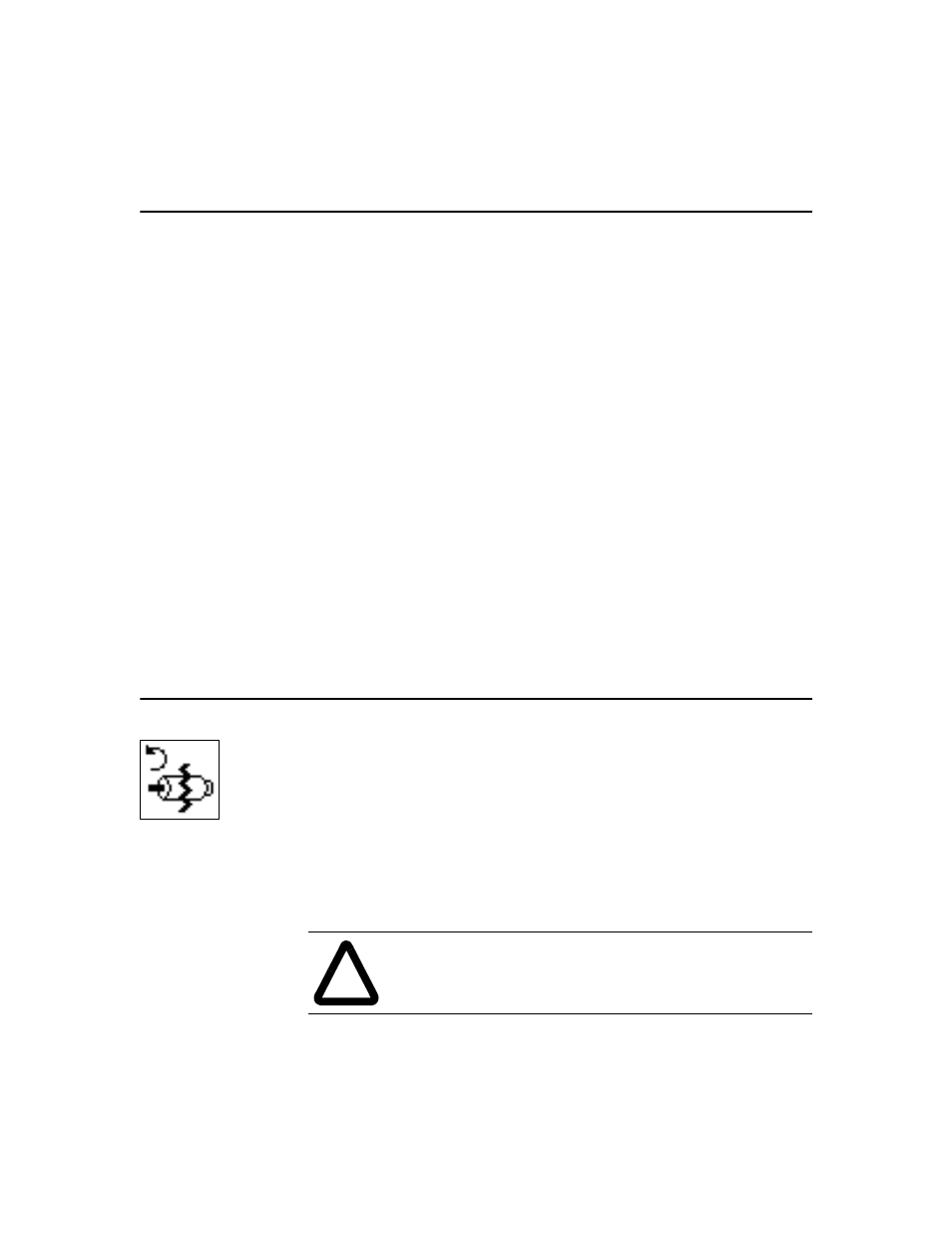
Publication GMLC-5.2 - November 1999
184
Control Setting Blocks
Use the Direct Drive Control block only on a physical master only axis, or
a servo axis when feedback is off (with feedback on, it has no effect). The
Direct Drive Control block automatically enables the selected axis by
activating the appropriate drive enable output before setting the servo
output to the commanded value. The 16-bit DAC on the motion controller
limits the effective resolution of the Direct Drive Control block to 305 µV
or 0.003%. In addition, the servo output limit (set by the Set Output Limit
function of the Motion Settings block) ultimately limits the actual servo
output voltage when using this block.
To deactivate the selected axis drive enable output, use a Feedback block
(selecting the Feedback Off Type). This zeros the servo output and
disables the drive enable output.
The Direct Drive Control block is most commonly used:
•
to provide an independent programmable analog output
•
to provide a speed reference for a non-servo drive
•
for testing a servo drive.
Reset Fault
Use the Reset Fault block to clear
•
All axis faults on a selected physical or virtual axis
•
A selected fault status on a selected physical or virtual axis
•
1394 system faults
The Reset Fault function block resides on the Main Palette.
The Reset Fault block only removes the fault status. It does not perform
any other recovery (for example, re-enabling feedback).
!
ATTENTION: Be sure to find and correct the cause of the
fault before clearing the fault status. Otherwise, the fault
recurs on program start-up.