Rockwell Automation GMLC Reference Manual User Manual
Page 266
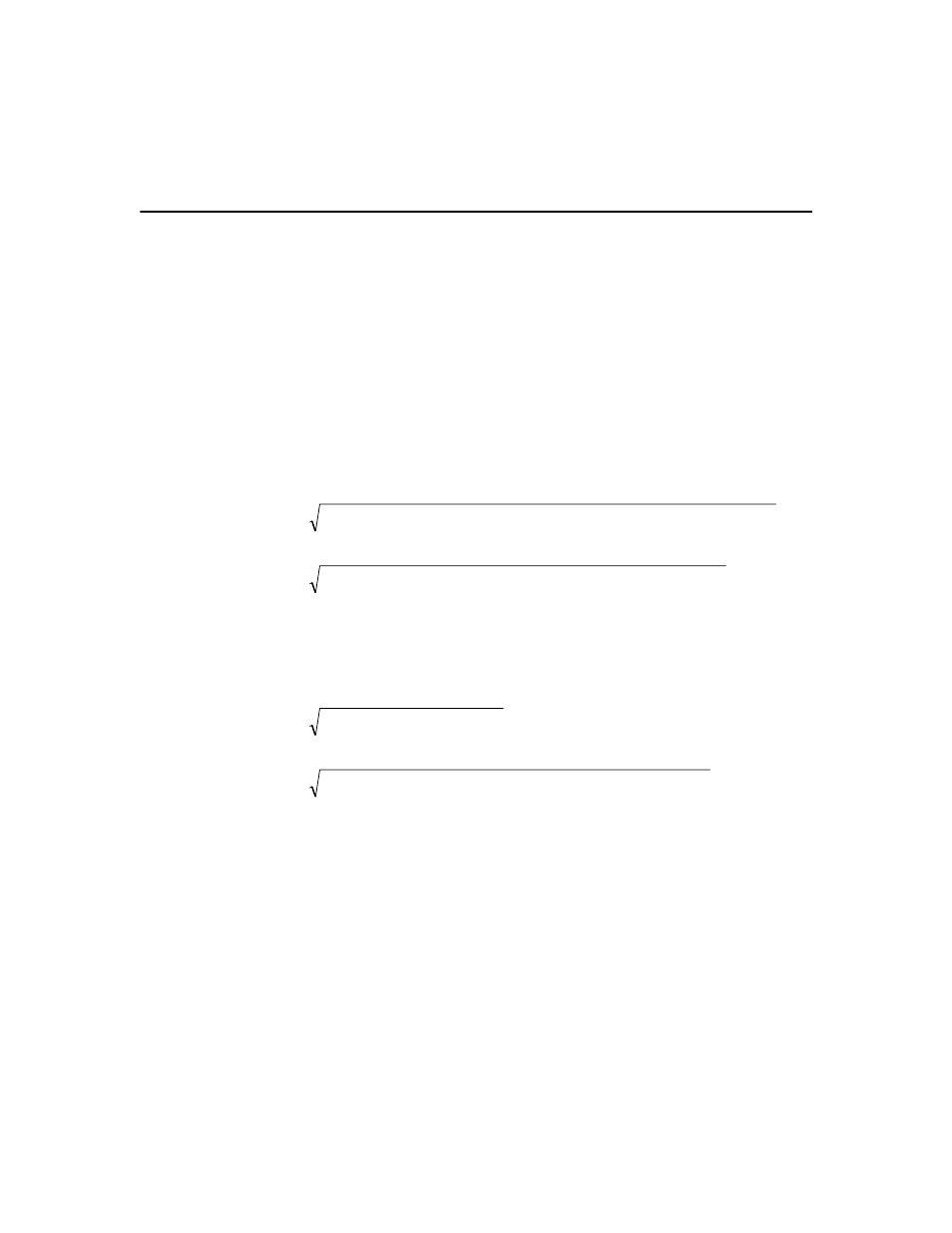
Publication GMLC-5.2 - November 1999
Interpolate Axes
229
The most frequent cause of bad arcs, other than typographical errors, is
incorrect trigonometric calculations, or lack of sufficient precision in the
calculations.
In the motion controller, the bad arc check is implemented by calculating
the radius of the arc at both the start and end points. If the radius of the arc
at the end point differs from the radius of the arc at the start point by more
than ±0.5%, the arc is deemed a bad arc.
In Absolute mode, the radius of the arc at the start point is as shown in the
first equation below and the radius of the arc at the end point is as shown
as in the second equation below.
In Incremental mode, the radius of the arc at the start point is as shown in
the first equation below, and the radius of the arc at the end point is as
shown in the second equation below.
If you get a Bad Arc runtime fault (Runtime_fault = 27), use the formulas
above to calculate the start and end radius of the arc. Then change the
destination or distance values in the Interpolate Axes block as required to
ensure that these two radii are within ±0.5% of each other. Note that
±0.5% is equivalent to three significant digits in the arc parameters.
2
2
(
.
)
(
.
)
Command Pos X
Center X
Command Pos Y
Center Y
−
+
−
2
2
(
)
(
)
Destination X
Center X
Destination Y
Center Y
−
+
−
2
2
(
)
(
)
Center X
Center Y
+
2
2
(
)
(
tan
)
Destination X
Center X
Dis
ce Y
Center Y
−
+
−