Rockwell Automation GMLC Reference Manual User Manual
Page 306
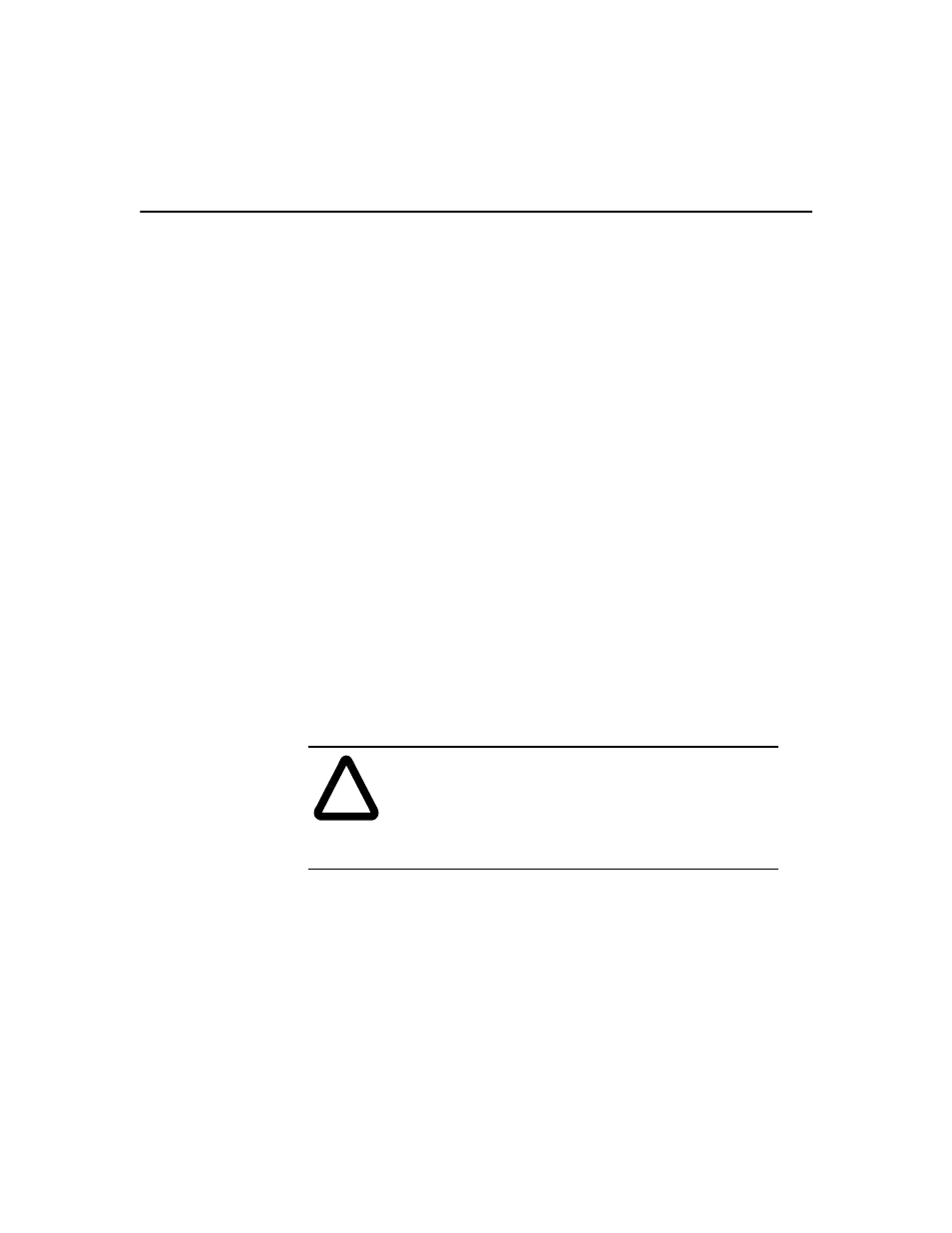
Publication GMLC-5.2 - November 1999
Auto Correction (Configure Cam)
269
Note that the short correction (negative short override) speed, as
represented in the above figure, is faster than the long correction
(negative long override) speed. This optional relationship is typical: short
corrections can be made quickly, while larger corrections are usually less
to avoid exceeding speed or acceleration limitations of the slave axis.
No-Correction Zone
In certain applications, you want to inhibit phase correction motion
during a certain portion of the position-lock cam cycle. For example, it
may be unwise to vary the speed of a cutting axis when cutting occurs.
This could cause damage to either the material being cut, or the cutting
implement.
With No Correction selected, the auto-correction indexer immediately
stops the phase shift move of the slave axis when the controller reaches
the no correction start point. The auto-correction indexer remains paused
until the controller passes the no correction end point, at which point it
resumes the phase shift move of the slave axis to complete the correction.
The slave axis neither decelerates when entering, nor accelerates when
leaving the no-correction zone. With large registration errors and/or high
correction speeds, this can cause a position error fault on the slave axis. If
No Correction had not been selected, the auto-correction phase shift move
would finish without interruption. (As shown by the dotted line in the
correction figure in Auto-Correction section of this chapter.)
!
ATTENTION: The slave axis neither decelerates,
when entering, nor accelerates, when leaving, the no-
correction zone. With large registration errors and/or
high correction speeds, this can cause a position error
fault on the slave axis.